Introduction
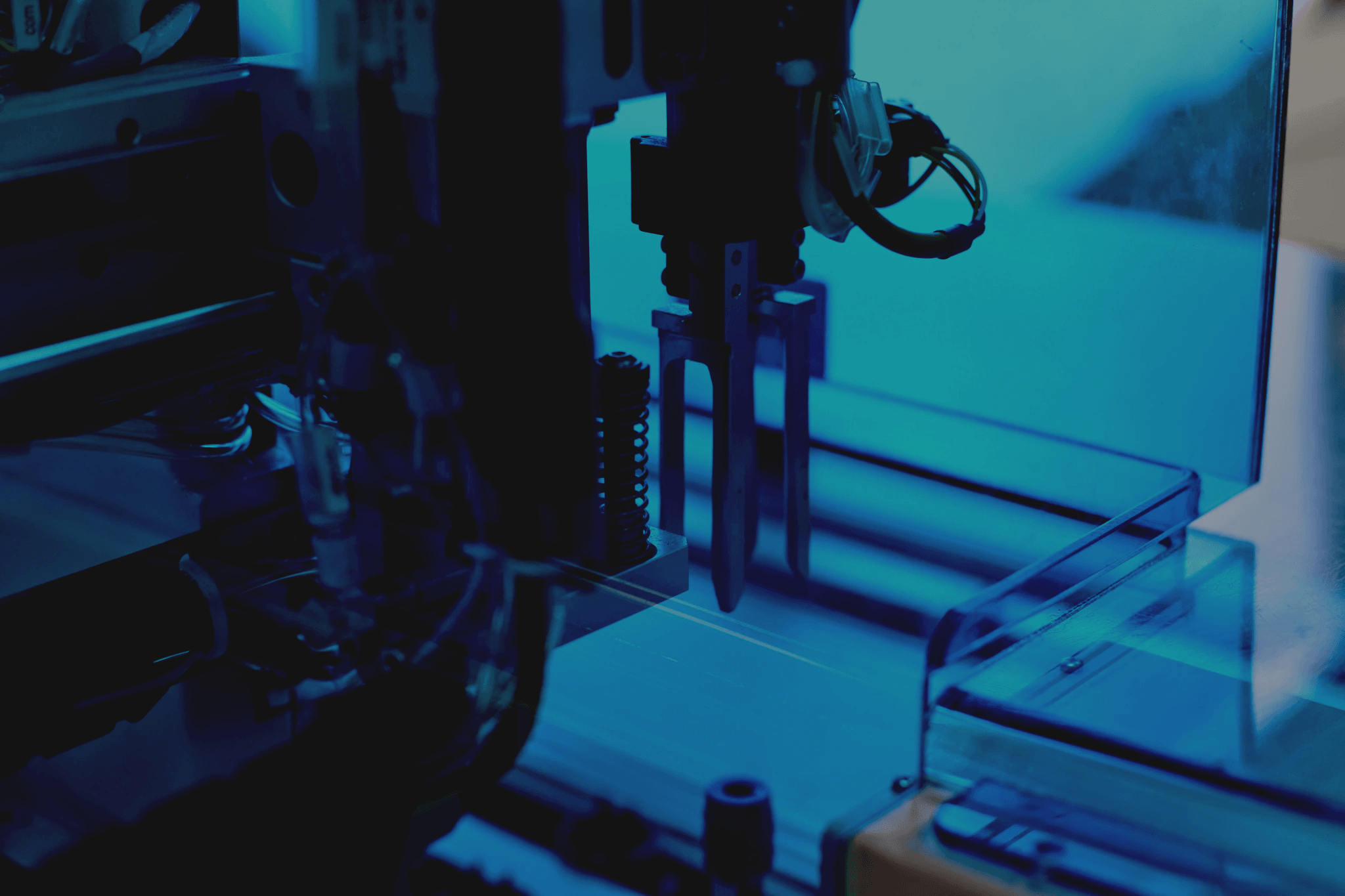
In the fast-paced world of manufacturing, efficiency is key, and automatic insertion machines are at the forefront of this revolution. These sophisticated devices automate the process of inserting components into printed circuit boards (PCBs), significantly enhancing production speed and accuracy. Understanding how these machines operate and their various benefits can provide insight into their critical role in modern manufacturing.
Understanding Automatic Insertion Machines
An automatic insertion machine is designed to streamline the assembly process by quickly and accurately placing components like resistors, capacitors, and jumper wires onto PCBs. Utilizing advanced technology, these machines operate on principles that combine robotics with precision engineering to ensure each component is inserted correctly every time. The design of an automatic insertion machine varies based on its intended use, but they all share a common goal: maximizing efficiency while minimizing human error.
Benefits of the Auto Insertion Process
The Auto Insertion Process offers numerous advantages over traditional manual methods, primarily in terms of speed and consistency. By automating component placement, manufacturers can increase production rates while maintaining high quality standards—crucial factors in today’s competitive market. Additionally, reducing reliance on manual labor not only cuts costs but also minimizes the risk of errors that can arise from human oversight during assembly.
How Insertion Types Differ: Radial vs Axial
Radial insertion involves components being placed perpendicular to the PCB surface, while axial insertion features components aligned parallel to it; each method has its unique set of applications and benefits. Understanding these differences is essential for manufacturers looking to optimize their processes—whether they require efficient jumper wire insertion or are exploring specific industry applications for radial or axial configurations.
What Is an Automatic Insertion Machine?
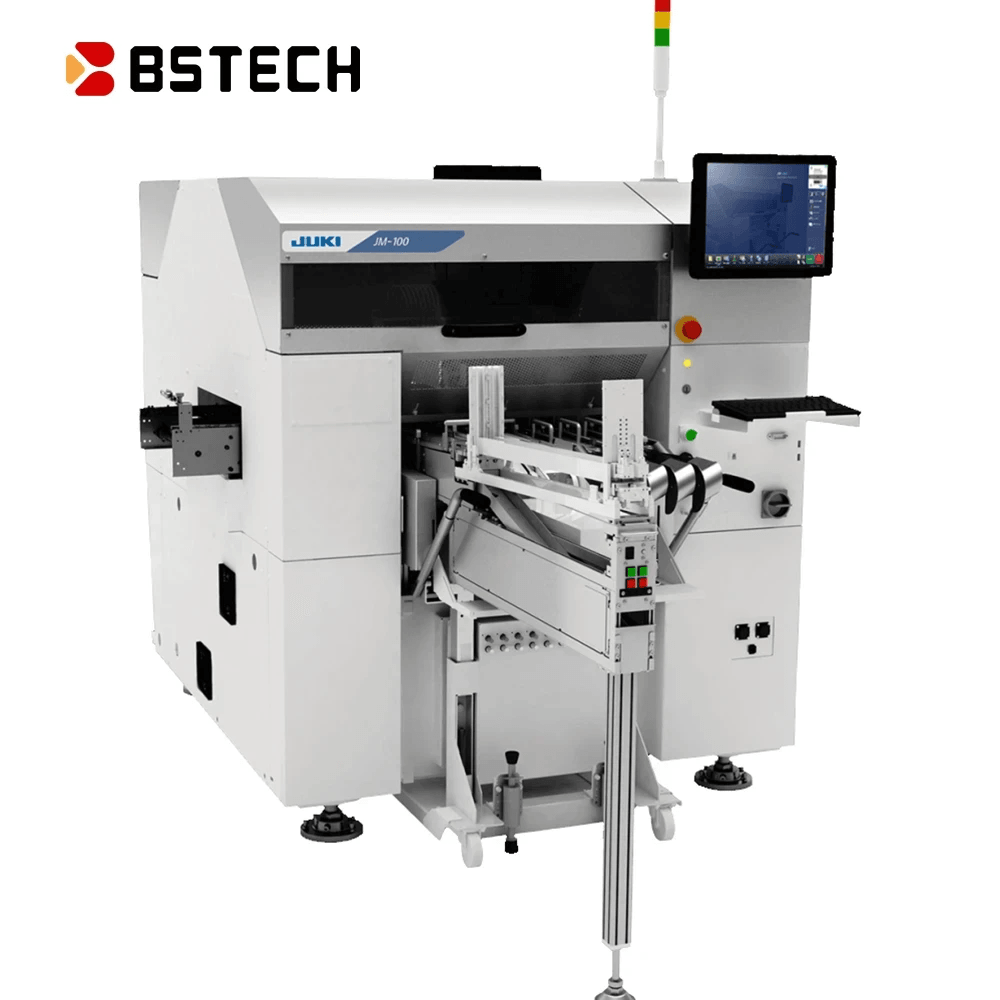
Automatic insertion machines are game-changers in the world of manufacturing, designed to streamline the process of inserting components into printed circuit boards (PCBs). These machines automate what was once a labor-intensive task, significantly improving efficiency and accuracy. By utilizing advanced technologies, they ensure that components such as resistors, capacitors, and jumper wires are placed precisely where needed.
Definition and Operating Principles
At its core, an automatic insertion machine is a sophisticated piece of equipment that automates the placement of electronic components onto PCBs. It operates using a combination of mechanical arms and vision systems to identify and insert components with high precision. The Auto Insertion Process allows for both radial insertion and axial insertion methods, enabling flexibility depending on the design requirements.
The machine's operating principles involve feeding components from reels or trays into a designated area where they are picked up by robotic arms. These arms then position the component accurately before inserting it into the board with controlled force. This level of automation not only reduces human error but also speeds up production times significantly.
Key Components of the Machine
An automatic insertion machine comprises several key components that work in harmony to achieve efficient operation. These include feeders for different types of components, robotic arms for precise placement, and control systems that manage all functions from start to finish. Each part plays a crucial role in ensuring that both radial insertion and axial insertion processes run smoothly.
Feeders can be designed for various component types including jumper wires, which require special handling due to their unique shapes and sizes. The robotic arms must be agile enough to navigate tight spaces on PCBs while maintaining accuracy during component placement. Finally, advanced software controls coordinate all activities within the machine, optimizing speed while minimizing errors throughout the Auto Insertion Process.
Role in Modern Manufacturing
In modern manufacturing environments, automatic insertion machines have become indispensable due to their ability to enhance productivity and reduce costs. With industries moving towards faster production cycles, these machines provide solutions that meet high-volume demands without compromising quality or precision. The incorporation of automatic insertion technology has revolutionized how manufacturers approach assembly lines.
Moreover, these machines facilitate complex designs by allowing for both radial insertion and axial insertion techniques within one system—making them versatile tools in electronics manufacturing. As more companies adopt this technology for tasks like jumper wire insertion or other intricate placements, we can expect continued advancements in automation techniques across various sectors.
The Auto Insertion Process Explained
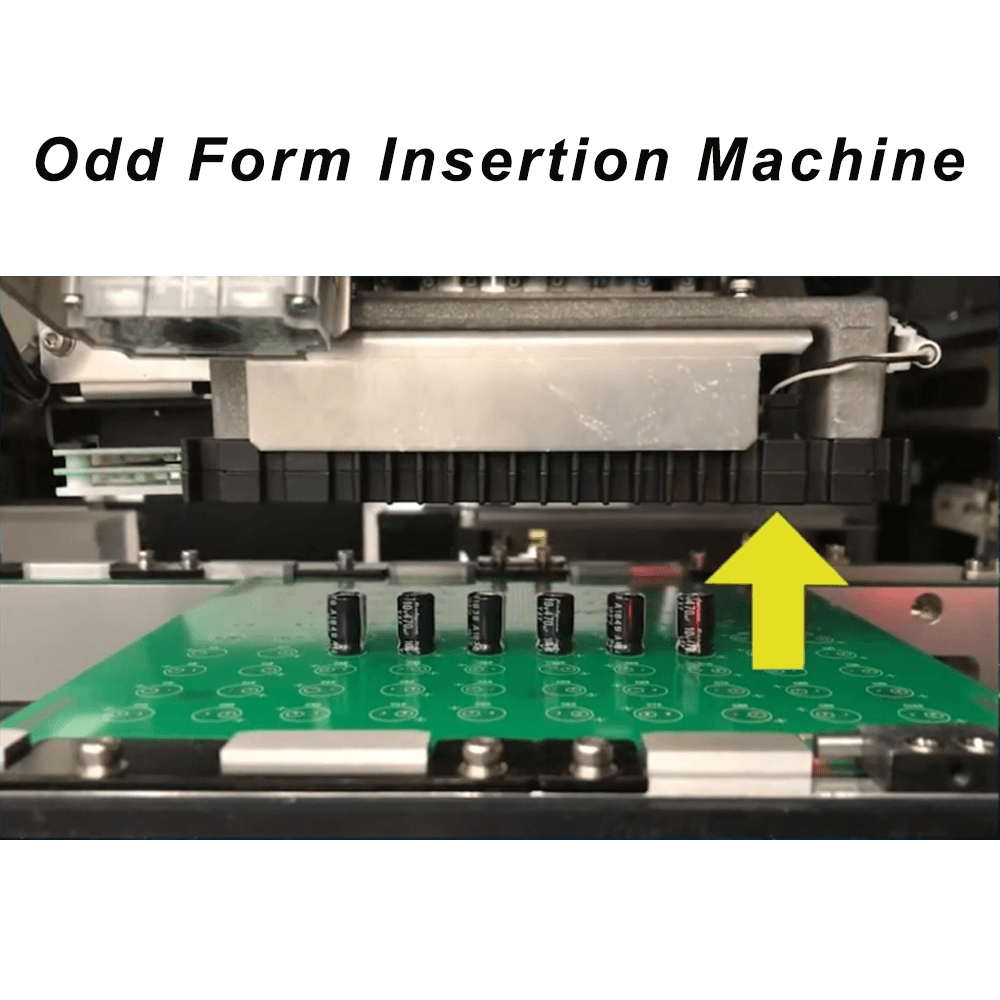
The Auto Insertion Process is a pivotal aspect of modern manufacturing, transforming how components are integrated into electronic assemblies. This process utilizes advanced machinery, specifically automatic insertion machines, to streamline the assembly line, ensuring precision and consistency. By automating tasks that were once done manually, manufacturers can significantly enhance productivity and reduce errors.
Overview of the Insertion Methodologies
Insertion methodologies in the context of an automatic insertion machine can be broadly categorized into Radial Insertion and Axial Insertion. Radial insertion involves components being inserted perpendicular to the circuit board, while axial insertion sees components aligned parallel to the board's surface. Each methodology has its own set of advantages and applications; for instance, Jumper Wire Insertion is often more efficient with radial methods due to easier access and placement.
These methodologies employ various techniques such as pick-and-place systems that accurately position components before they are soldered or pressed into place. The choice between these methods often depends on factors like component type, board layout, and production volume. Understanding these differences allows manufacturers to optimize their processes for better results.
Efficiency and Speed of Automation
The efficiency gained from using an automatic insertion machine cannot be overstated; it drastically reduces cycle times compared to traditional manual methods. Automation accelerates the process of inserting various components—be it resistors, capacitors, or Jumper Wires—allowing for rapid production without compromising quality. This speed translates directly into cost savings as companies can produce more units in less time.
Moreover, automated systems are designed for high repeatability; once programmed correctly, they can perform tasks with consistent accuracy across multiple runs. This reliability is crucial in industries where even minor errors can lead to significant issues down the line. Ultimately, embracing automation through techniques like Radial Insertion or Axial Insertion positions manufacturers at a competitive advantage in today’s fast-paced market.
Comparison with Manual Insertion
When comparing manual insertion with automated processes like those found in an automatic insertion machine setup, several key differences emerge that highlight automation's superiority. Manual insertion relies heavily on human skills and judgment; while this may work fine for small-scale operations or prototyping projects, it becomes increasingly inefficient as production scales up. Errors due to fatigue or oversight can lead to costly rework or defective products.
In contrast, automated systems excel at maintaining high levels of accuracy while operating continuously without breaks—ideal for large production runs involving complex assemblies that include Jumper Wire Insertion and other intricate tasks. Additionally, automated machines can handle variations in component types effortlessly by simply adjusting program settings rather than requiring retraining of personnel each time a change occurs. Thus, investing in automation not only boosts productivity but also enhances overall product quality.
Jumper Wire Insertion: A Special Case
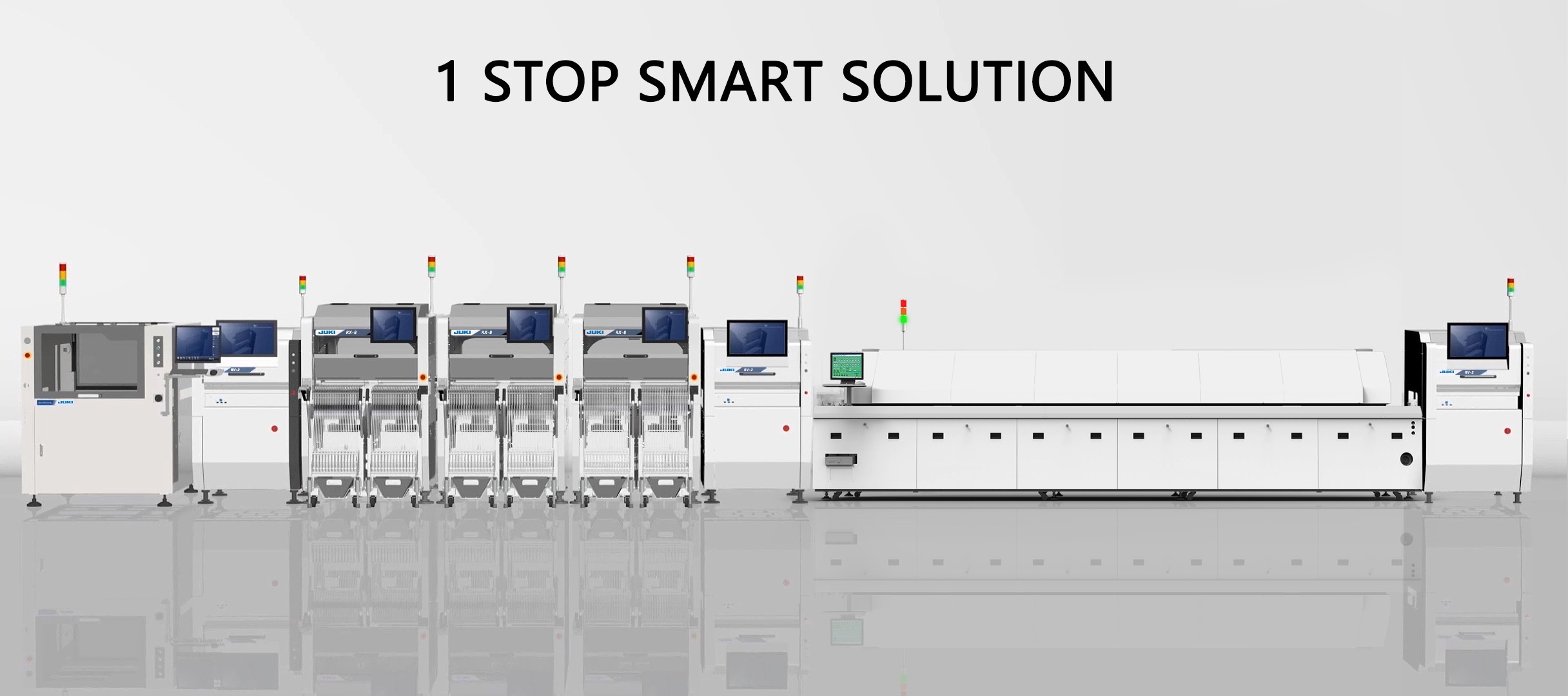
Jumper wire insertion is a pivotal aspect of circuit design and assembly, acting as the connective tissue that links various components together. These wires provide essential pathways for electrical signals, ensuring that circuits function seamlessly. In the realm of automatic insertion machines, jumper wire insertion has become increasingly efficient, transforming how manufacturers approach circuit assembly.
Importance of Jumper Wires in Circuits
Jumper wires are crucial for establishing connections between different parts of a circuit board, especially when direct traces on the PCB are impractical. They allow for flexibility in design and can rectify issues like routing errors or space constraints without requiring a complete redesign of the board. The significance of jumper wire insertion cannot be overstated; it ensures reliability and functionality in electronic devices ranging from simple gadgets to complex machinery.
How Automatic Insertion Enhances Efficiency
The integration of automatic insertion machines into the jumper wire insertion process has revolutionized efficiency in manufacturing environments. These machines streamline operations by quickly and accurately placing jumper wires where they need to go, reducing manual labor and minimizing human error. With the Auto Insertion Process, manufacturers can achieve higher production rates while maintaining quality control—an irresistible combination for any industry looking to stay competitive.
Applications in Various Industries
Jumper wire insertion finds applications across numerous industries, including automotive, aerospace, consumer electronics, and telecommunications. In these sectors, precision and reliability are paramount; thus, employing an automatic insertion machine becomes not just beneficial but essential for meeting stringent standards. Whether it's enhancing connectivity within a car's electronic system or ensuring seamless communication between devices in telecommunications networks, efficient jumper wire insertion plays a vital role.
Diving into Radial Insertion
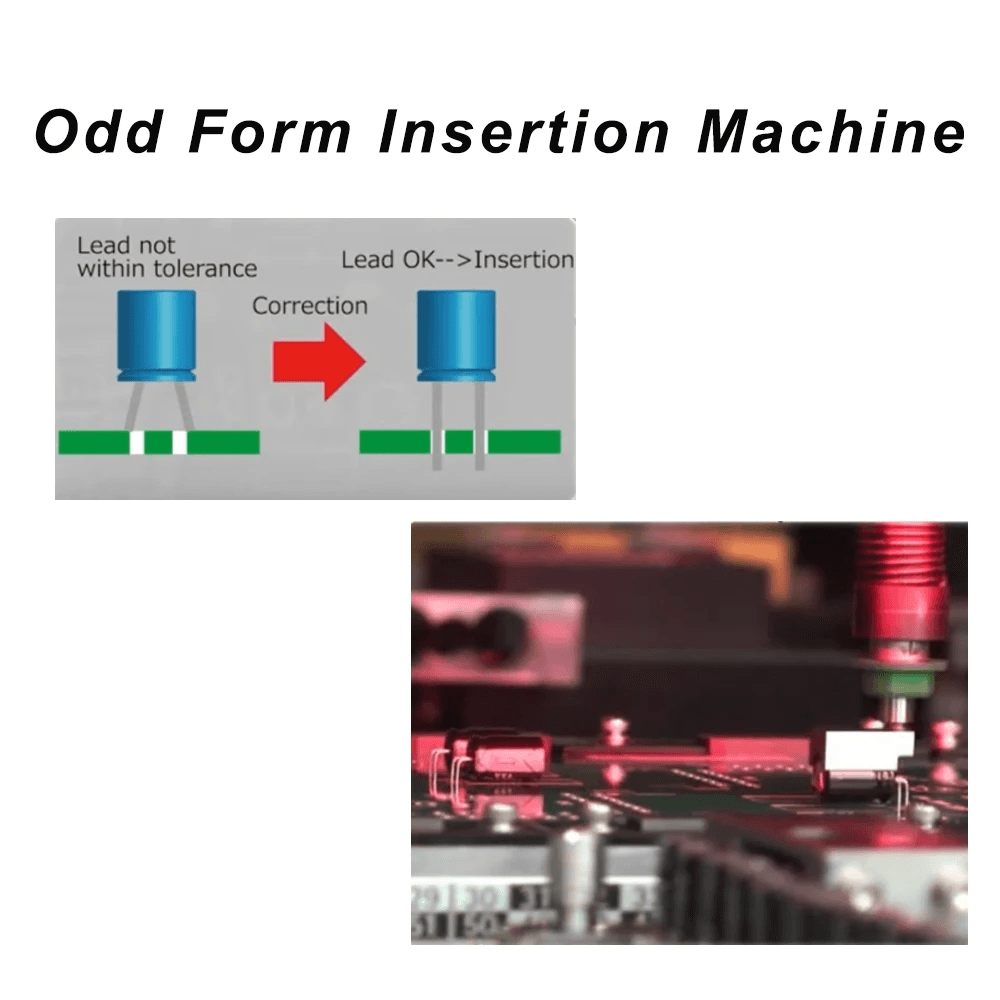
Radial insertion is a fascinating aspect of the Auto Insertion Process, particularly when it comes to how components are placed onto printed circuit boards (PCBs). This method involves inserting components with leads that extend radially from their body, allowing for efficient placement in tight spaces. Understanding the intricacies of radial component insertion helps manufacturers optimize their production lines and enhance overall efficiency.
Understanding Radial Component Insertion
Radial component insertion is characterized by its unique approach to placing electronic components on a PCB. In this method, components such as resistors and capacitors are inserted into holes on the board with leads that radiate outward, resembling spokes on a wheel. This design not only facilitates quick assembly but also ensures that components can be densely packed without compromising performance.
The automatic insertion machine plays a crucial role in this process by precisely positioning each component before soldering them into place. Advanced technology allows these machines to handle various component sizes and types, making them indispensable in modern manufacturing environments. By leveraging radial insertion techniques, companies can streamline production while maintaining high quality.
Advantages Over Other Insertion Methods
One of the standout advantages of radial insertion is its ability to maximize space efficiency on PCBs compared to axial insertion methods. With leads extending radially, multiple components can fit snugly together without risking interference or damage during assembly or operation. This compact arrangement not only saves space but also reduces material costs and improves overall circuit design.
Moreover, when it comes to Jumper Wire Insertion, radial methods offer an edge in terms of adaptability and versatility in circuit designs. The automatic insertion machine can easily accommodate different lead lengths and configurations, ensuring compatibility across various applications. As a result, manufacturers benefit from increased flexibility while reducing assembly time significantly.
Lastly, radial insertion often results in improved reliability due to better mechanical stability once the components are soldered into place. The configuration allows for stronger connections that withstand vibrations and thermal stresses more effectively than other methods like axial insertion might allow.
Real-World Applications and Case Studies
Radial component insertion finds its niche across many industries where high-density circuits are essential—think automotive electronics or consumer devices like smartphones and tablets. For instance, automotive manufacturers rely heavily on this method for assembling control units where space is at a premium yet reliability remains critical for safety features like anti-lock braking systems.
A notable case study involves an electronics manufacturer who transitioned from manual assembly processes to automated radial insertion using advanced automatic insertion machines. The switch resulted in a 40% increase in production speed while simultaneously decreasing defects by over 25%. Such success stories highlight how embracing modern technologies can revolutionize traditional manufacturing practices.
In summary, diving into radial insertion reveals its significant advantages over other methods like axial insertion within the realm of electronic manufacturing. With applications spanning numerous industries—from automotive to consumer electronics—this technique showcases how innovation continues shaping the future of PCB assembly through efficient automatic processes.
Exploring Axial Insertion
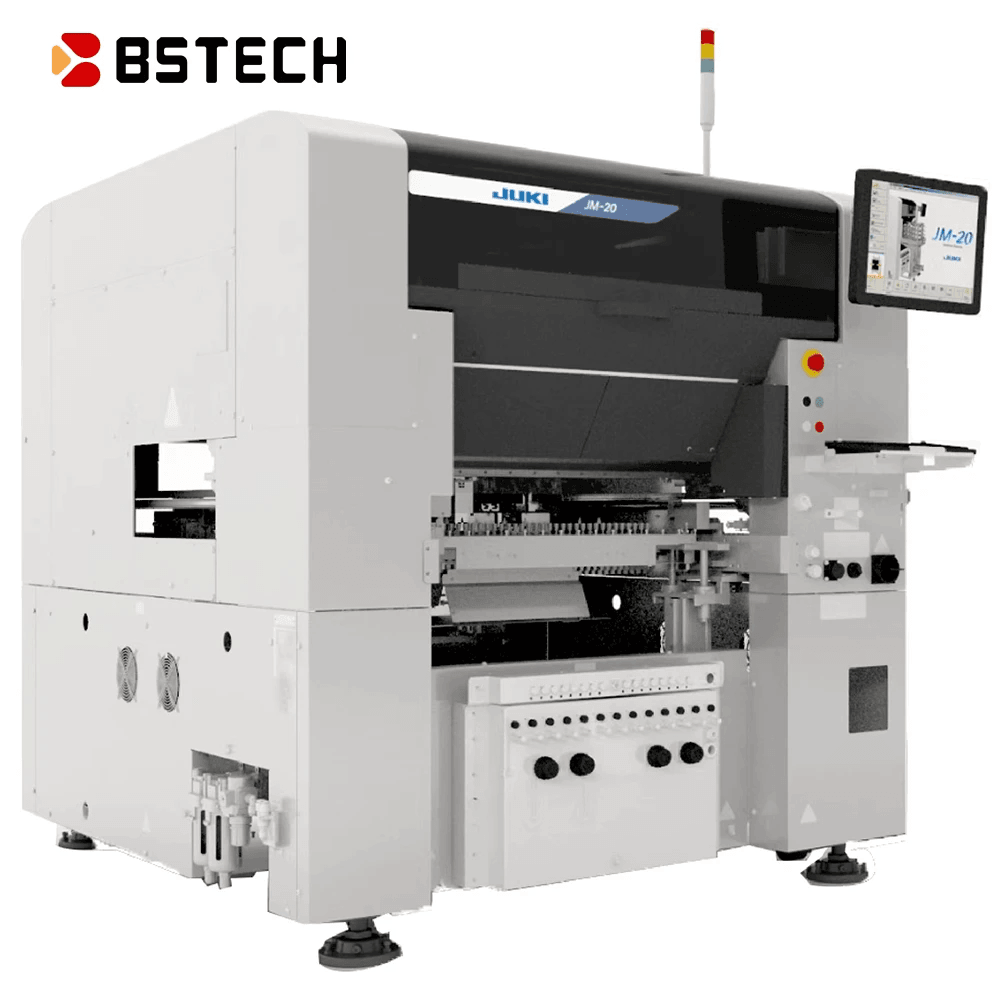
Axial insertion is a fascinating aspect of the automatic insertion machine landscape. This method involves placing components in a straight line along the axis of a circuit board, which offers distinct advantages over other insertion types, such as radial insertion. The precision and efficiency of axial insertion make it an invaluable process in modern manufacturing environments.
What Makes Axial Insertion Unique
What sets axial insertion apart from its counterparts is its streamlined approach to component placement. The design allows components to be inserted directly into the board without requiring multiple rotations or adjustments, significantly reducing cycle times during the Auto Insertion Process. This direct alignment not only enhances speed but also improves accuracy, ensuring that each component is perfectly positioned for optimal performance.
In addition to speed and precision, axial insertion supports a wider variety of component types, including resistors and capacitors. This versatility means that manufacturers can simplify their production processes by utilizing one method for multiple components instead of switching between radial and axial methods. As industries evolve and demand increases for more efficient production lines, axial insertion stands out as a key player in meeting these challenges.
Industry Applications and Benefits
Axial insertion finds its niche across various industries due to its unique capabilities and benefits. For instance, in the electronics sector, where speed and reliability are paramount, this method excels by ensuring rapid assembly without compromising quality. Additionally, industries such as automotive manufacturing leverage axial insertion for producing reliable circuit boards that power everything from entertainment systems to safety features.
One notable benefit is cost-effectiveness; by implementing an automatic insertion machine with axial capabilities, companies can reduce labor costs associated with manual assembly processes. Furthermore, the reduced error rates lead to less waste and rework—factors that are critical in maintaining profitability amid competitive pressures. With applications extending into telecommunications and medical devices as well, it's clear that axial insertion plays a pivotal role in diverse sectors.
How Bensun Technology Excels in Axial Insertion
Bensun Technology has emerged as a leader in advancing axial insertion techniques within the realm of automatic insertion machines. Their innovative designs focus on maximizing efficiency while minimizing downtime during production runs—key factors that enhance overall productivity for manufacturers using their equipment. By integrating cutting-edge technology with user-friendly interfaces, Bensun ensures that clients can easily adapt their operations to take full advantage of axial insertion's benefits.
Moreover, Bensun's commitment to quality control means that each automatic insertion machine undergoes rigorous testing before it reaches customers' hands. This dedication translates into reliable performance on the factory floor where Jumper Wire Insertion may also be required alongside other components like resistors or capacitors—showcasing true versatility in operation. As industries continue evolving toward automation solutions like those offered by Bensun Technology, companies can confidently invest knowing they have access to top-tier machinery designed specifically for modern manufacturing needs.
Conclusion
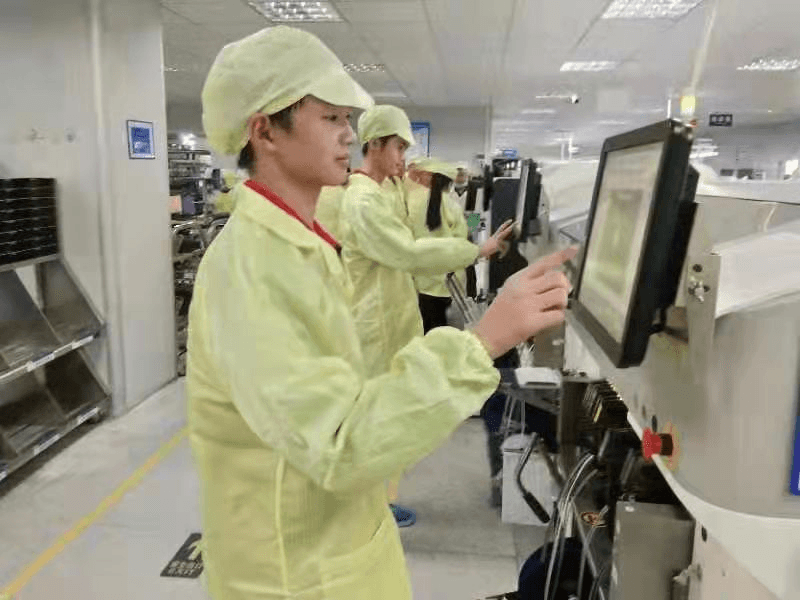
In the rapidly evolving landscape of manufacturing, automatic insertion machines are becoming indispensable. The Auto Insertion Process not only streamlines production but also enhances precision, making it a game-changer in various industries. As we look ahead, the future promises even more innovations that will further optimize these machines and their applications.
The Future of Automatic Insertion Machines
The future of automatic insertion machines is bright and filled with potential advancements. With ongoing developments in technology, we can expect improvements in speed, accuracy, and flexibility within the Auto Insertion Process. Innovations such as artificial intelligence and machine learning will likely enable these machines to adapt to different component types seamlessly, enhancing capabilities like Jumper Wire Insertion and both Radial and Axial Insertion methods.
Moreover, sustainability is becoming a key focus in manufacturing processes. Automatic insertion machines will likely incorporate eco-friendly practices that reduce waste while maintaining high efficiency levels during production runs. This shift towards greener technologies will not only benefit manufacturers but also appeal to environmentally-conscious consumers.
Tailoring Solutions with Bensun Technology
Bensun Technology stands at the forefront of innovation in the realm of automatic insertion machines. Their commitment to tailoring solutions for diverse client needs ensures that businesses can maximize their productivity through optimized Auto Insertion Processes. Whether it's enhancing Jumper Wire Insertion or refining Radial and Axial Insertion techniques, Bensun offers customizable options that cater specifically to industry demands.
Additionally, Bensun's expertise allows them to stay ahead of market trends by integrating cutting-edge technology into their designs. This proactive approach enables clients to benefit from enhanced operational efficiencies while keeping pace with evolving industry standards. Ultimately, partnering with Bensun Technology translates into a competitive edge for manufacturers looking to streamline their processes.
Final Thoughts on Insertion Types and Processes
Understanding the distinctions between Radial and Axial Insertion methods is crucial for any manufacturer looking to optimize their production line effectively. Each method has its unique advantages; choosing between them depends largely on specific application requirements and component types involved in the assembly process. The ability to leverage automatic insertion machines for both methodologies significantly boosts efficiency while minimizing human error.
In conclusion, as industries continue embracing automation, the role of automatic insertion machines will only grow more prominent. The integration of advanced technologies will enhance traditional processes like Jumper Wire Insertion while setting new standards for Radial and Axial Insertion applications across various sectors. By staying informed about these developments, manufacturers can position themselves advantageously within an increasingly competitive landscape.