Introduction
In the fast-paced realm of electronics manufacturing, SMT chip mounter machines play a pivotal role in the printed circuit assembly (PCA) process. These sophisticated machines are designed to accurately place components on PCB (printed circuit board) surfaces, ensuring high-quality and efficient production. As technology evolves, understanding the essential features of these machines becomes increasingly important for achieving optimal PCB production and assembly.
Understanding SMT Chip Mounter Machines
SMT chip mounter machines are central to modern PCB assembly lines, where speed and precision are paramount. They utilize advanced technology to automate the placement of tiny components onto chip boards, significantly enhancing productivity compared to manual methods. By integrating systems that manage solder paste application and component handling, these machines streamline the entire PCB design process.
Importance of Key Features
When selecting an SMT chip mounter machine, key features such as speed, accuracy, and flexibility must be considered for effective PCB production and assembly. Speed affects overall throughput, while accuracy ensures that each component is placed correctly—vital for preventing costly errors in printed circuit assemblies. Flexibility allows manufacturers to adapt quickly to different designs or changes in solder paste specifications without extensive downtime.
Overview of the Market
The market for SMT chip mounter machines is diverse and competitive, with numerous brands offering various models tailored to different production needs. Companies are increasingly investing in these technologies as they seek to improve their PCB assembly processes while keeping costs manageable. With ongoing advancements in automation and robotics integration within these machines, manufacturers can expect enhanced capabilities that will shape the future of printed circuit board production.
Essential Features of SMT Chip Mounter Machines
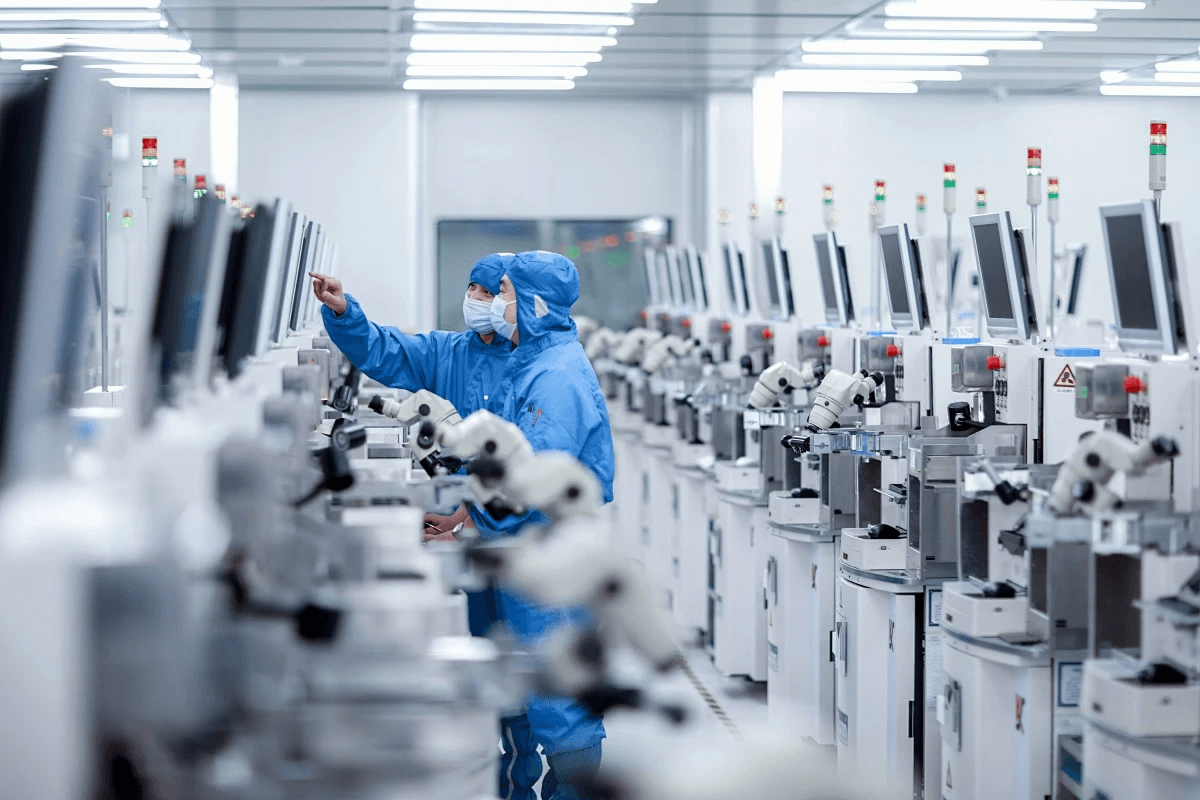
When diving into the world of SMT chip mounter machines, it's essential to grasp the features that make these machines indispensable in printed circuit assembly (PCA). These features directly impact the efficiency and quality of PCB production and assembly, ensuring that your chip boards come out just right. Let’s break down these essential characteristics: speed and efficiency, accuracy and precision, and flexibility in component handling.
Speed and Efficiency
Speed is the name of the game when it comes to SMT chip mounter machines. In a fast-paced manufacturing environment, having a machine that can swiftly place components on PCB designs can significantly reduce production time. More importantly, efficiency translates into lower operational costs—who doesn’t want to save on labor while boosting output?
Modern SMT machines are designed to handle high volumes without sacrificing quality. With advancements in technology, some models can achieve placement speeds that rival even the most seasoned technicians. This remarkable speed means quicker turnaround times for PCB assembly projects, allowing manufacturers to meet tight deadlines without breaking a sweat.
Accuracy and Precision
While speed is crucial, it should never come at the expense of accuracy—especially in printed circuit assembly where even a tiny misalignment can lead to catastrophic failures. SMT chip mounter machines are engineered with cutting-edge technologies that ensure components are placed with pinpoint precision on each PCB design. This level of accuracy minimizes rework and scrap rates, which are costly for any production line.
Additionally, many modern machines incorporate sophisticated vision systems that detect misalignments or defects during the placement process. These systems enhance quality control by ensuring only perfectly assembled chip boards move forward in the production line. As a result, manufacturers can maintain high standards while optimizing their PCB production and assembly processes.
Flexibility in Component Handling
In today's diverse electronics market, flexibility is key for any SMT chip mounter machine worth its salt. The ability to handle various component sizes—from tiny chips to larger capacitors—is essential for adapting to different PCB designs without extensive modifications or downtime. Machines equipped with interchangeable nozzles or feeders allow operators to switch between components seamlessly.
This flexibility extends beyond just component size; it also involves accommodating different solder paste types used in various applications within PCB assembly processes. Whether you’re dealing with traditional solder or newer lead-free options, having a machine capable of adjusting quickly ensures you stay ahead of industry trends while fulfilling client needs efficiently.
Ultimately, investing in an SMT chip mounter machine with these essential features will elevate your manufacturing capabilities significantly—making your printed circuit assembly operations not only faster but also smarter.
Key Technologies in SMT Chip Mounter Machines
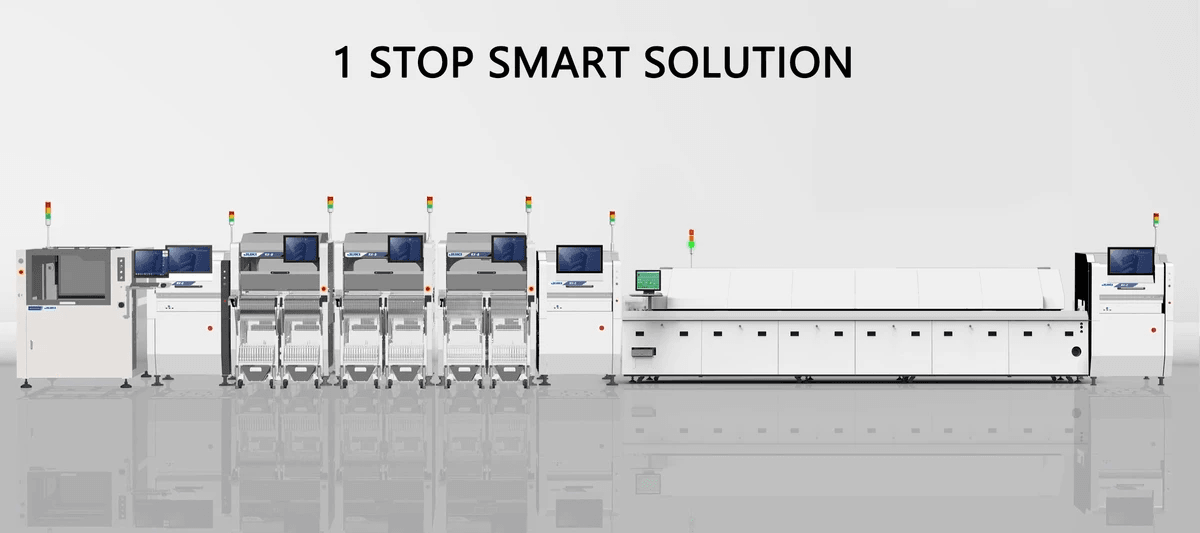
In the world of printed circuit assembly (PCA), the technology behind SMT chip mounter machines plays a pivotal role in determining production efficiency and quality. As the demand for high-quality PCB assembly escalates, manufacturers are increasingly relying on advanced technologies to keep up with industry standards. This section delves into three key technologies that are transforming the landscape of PCB production and assembly: advanced pick and place technology, vision systems for quality control, and automation and robotics integration.
Advanced Pick and Place Technology
At the heart of every efficient SMT chip mounter machine lies its pick and place technology, which is essential for accurate component placement on chip boards. This technology utilizes sophisticated algorithms to ensure that components are positioned with precision, minimizing errors during PCB assembly. The ability to handle various sizes and shapes of components enhances flexibility in production, allowing manufacturers to adapt quickly to changing demands in PCB design.
Moreover, modern pick and place systems have integrated features like multi-function heads that can switch between different tools seamlessly. This adaptability not only speeds up the process but also reduces downtime associated with tool changes during production runs. As a result, companies can achieve higher throughput while maintaining stringent quality standards in their PCB production and assembly processes.
Vision Systems for Quality Control
Quality control is paramount in printed circuit assembly, where even a minor defect can lead to significant failures down the line. Vision systems embedded within SMT chip mounter machines serve as an essential safeguard against such issues by providing real-time inspection capabilities throughout the manufacturing process. These systems utilize high-resolution cameras paired with advanced image processing algorithms to detect misalignments or defects before they become problematic.
The integration of vision systems allows for automated feedback loops that adjust machine operations based on inspection results, ensuring consistently high-quality output in PCB assembly. By catching errors early—such as misaligned solder paste or incorrectly placed components—manufacturers can save time and resources while enhancing product reliability. Ultimately, these technologies contribute significantly to reducing waste in the manufacturing process by ensuring only flawless chip boards move forward.
Automation and Robotics Integration
The future of SMT chip mounter machines is undeniably intertwined with automation and robotics integration, which streamline operations across all stages of PCB production and assembly. Automated material handling systems work hand-in-hand with mounters to ensure that components are delivered precisely when needed without manual intervention—enhancing overall efficiency significantly. Moreover, robotic arms equipped with sophisticated sensors can perform complex tasks at speeds unattainable by human operators.
This level of automation not only boosts productivity but also minimizes human error—a critical factor when dealing with intricate electronic assemblies where precision is key. Additionally, integrating robotics allows for greater scalability; manufacturers can easily ramp up production levels without compromising on quality or speed as market demands fluctuate rapidly in today’s tech-driven world. With these advancements at play, businesses are poised to meet future challenges head-on while maximizing their operational capabilities.
Comparing Top SMT Chip Mounter Brands
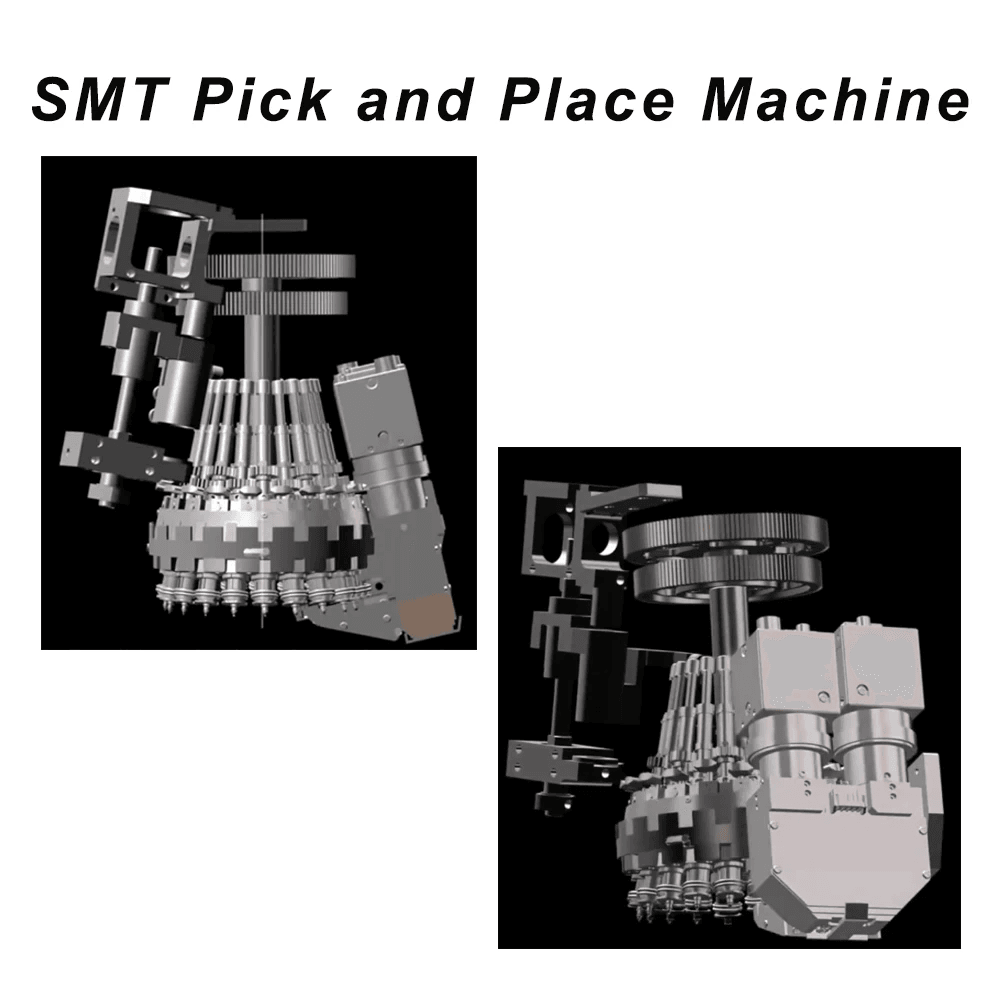
JUKI: Innovation and Reliability
JUKI has built a solid reputation in the SMT chip mounter machine market, emphasizing innovation and reliability in its designs. Their machines excel in accuracy and are equipped with advanced features that enhance PCB assembly processes, ensuring high-quality outputs with minimal defects. With a focus on automating solder paste application and component placement, JUKI’s systems streamline printed circuit assembly while accommodating various chip boards.
JUKI's commitment to research and development means they frequently update their technology to keep pace with industry demands. This dedication not only improves efficiency but also reduces downtime during PCB production and assembly operations. For manufacturers looking for a dependable partner in their SMT journey, JUKI stands out as a top choice.
YAMAHA: Speed Meets Versatility
YAMAHA is synonymous with speed when it comes to SMT chip mounter machines, making them an excellent choice for companies requiring rapid turnaround times without sacrificing quality. Their systems are designed to handle diverse component types seamlessly, offering unmatched flexibility in PCB design options while maintaining high throughput rates during production runs. This versatility allows manufacturers to adapt quickly to changing market demands or product variations.
In addition to speed, YAMAHA machines integrate sophisticated vision systems that enhance precision during the placement of components onto chip boards. The combination of fast operation and accurate placement positions YAMAHA as a leading contender in the competitive landscape of PCB assembly machinery. For businesses aiming for efficiency without compromising on adaptability, YAMAHA delivers robust solutions tailored to modern manufacturing needs.
Panasonic: A Legacy of Quality
Panasonic has long been regarded as a stalwart in the electronics manufacturing sector, particularly known for its high-quality SMT chip mounter machines that stand the test of time. Their products have consistently demonstrated exceptional performance in both speed and accuracy within printed circuit assembly applications. With decades of experience under their belt, Panasonic’s legacy is reflected in their commitment to delivering reliable solutions for PCB production and assembly.
What sets Panasonic apart is its focus on user-friendly interfaces combined with powerful automation features that simplify complex processes like solder paste application or component handling on various chip boards. This ensures operators can achieve optimal results even under tight deadlines or challenging conditions—making them an invaluable asset for any manufacturer striving for excellence in PCB design execution. For those who value quality backed by years of expertise, Panasonic remains a trusted name worth considering.
Maintenance Tips for SMT Chip Mounter Machines
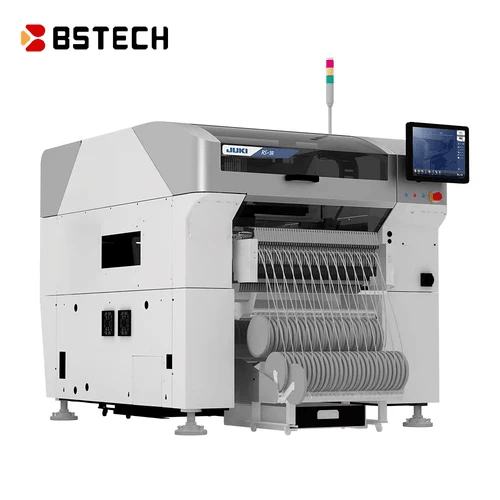
Keeping your SMT chip mounter machine in top shape is crucial for efficient printed circuit assembly (PCA) and overall PCB production and assembly. Regular maintenance not only extends the lifespan of your equipment but also ensures high-quality outcomes in PCB design and manufacturing. Here are some essential tips to keep your machine running smoothly.
Regular Calibration Practices
Calibration is the backbone of precision in SMT chip mounter machines. By regularly calibrating your equipment, you ensure that components are placed accurately on chip boards, reducing the risk of defects during PCB assembly. Schedule calibration sessions based on usage frequency; for busy production lines, consider weekly checks to maintain optimal performance.
Utilize calibration tools specifically designed for SMT machines to measure parameters like placement accuracy and solder paste application. Document all calibration results to track any deviations over time, allowing for proactive adjustments before issues escalate. Remember, a well-calibrated machine leads to fewer errors in PCB production and assembly, enhancing overall productivity.
Cleaning and Lubrication Techniques
Cleaning is an often-overlooked aspect of maintaining an SMT chip mounter machine but is vital for preventing contamination during printed circuit assembly processes. Regularly clean the nozzles, feeders, and other critical components to remove any residual solder paste or dust that can affect performance. Use appropriate cleaning solutions that won’t harm sensitive parts but effectively eliminate grime.
Lubrication also plays a key role in keeping mechanical parts moving smoothly; refer to the manufacturer's guidelines for recommended lubricants specific to your model. Pay special attention to moving parts such as rails and gears—these require regular lubrication to prevent wear and tear that can lead to costly downtimes in PCB production and assembly processes. A well-maintained machine not only performs better but also reduces operational noise levels.
Troubleshooting Common Issues
Even the best-maintained SMT chip mounter machines can experience hiccups from time to time; knowing how to troubleshoot these issues can save you valuable production time. Common problems include misalignment during component placement or inconsistent solder paste application on chip boards—both of which can derail an entire batch of PCBs if not addressed quickly.
Start by checking the calibration settings if you notice alignment issues; this often resolves minor discrepancies without needing extensive repairs. For solder paste problems, inspect the stencil used during application—dirt or damage may hinder its effectiveness during printed circuit assembly operations. Keeping a troubleshooting guide handy with common issues specific to your model will help streamline repairs when they arise.
Choosing the Right SMT Chip Mounter Machine
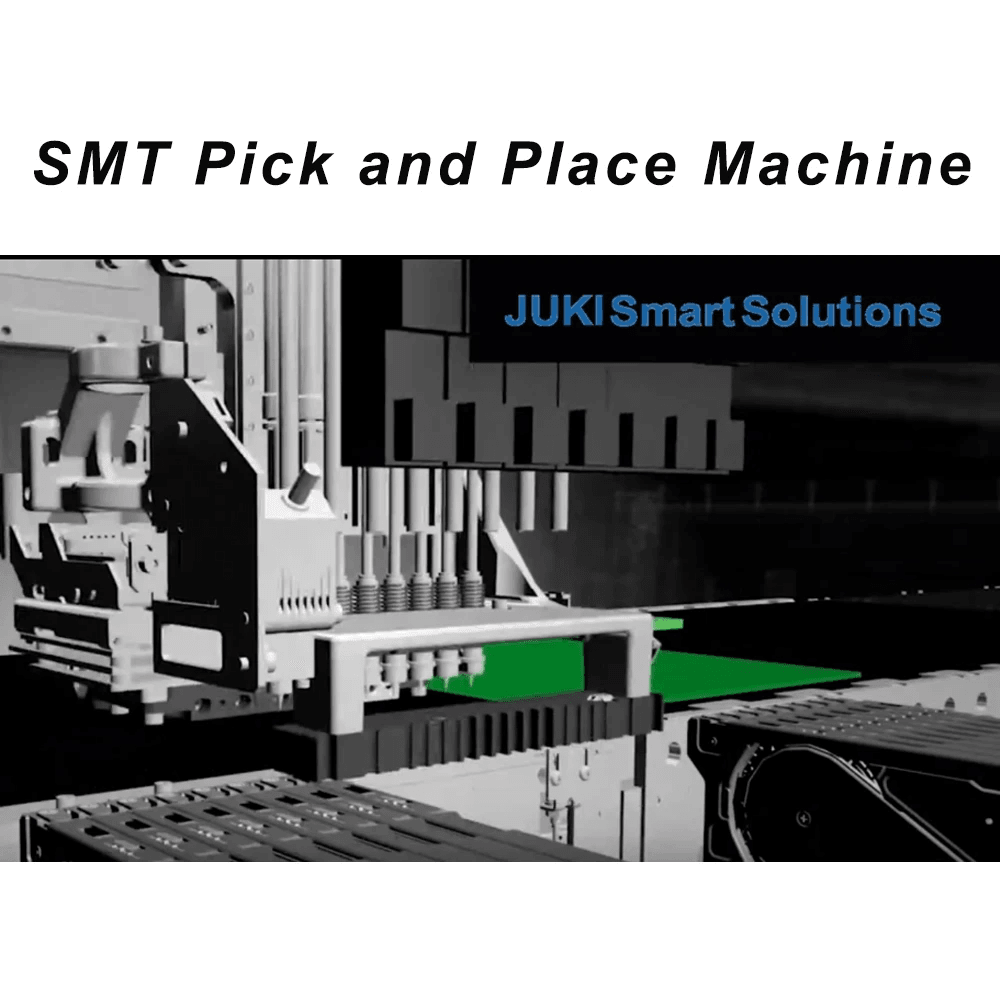
Selecting the perfect SMT chip mounter machine is akin to finding the right partner for a dance—you need to ensure that it fits your production needs, budget, and offers reliable support. With an array of options available in the market, making an informed decision can significantly impact your printed circuit assembly (PCA) efficiency and overall PCB production and assembly quality. As you embark on this journey, keep in mind the critical factors that will help you make a choice that aligns with your operational goals.
Assessing Production Needs
Before diving into the world of SMT chip mounter machines, it's essential to assess your specific production needs thoroughly. Consider factors such as volume requirements, types of components you'll be handling, and whether you're focusing on small batch runs or mass PCB assembly. By identifying these parameters early on, you can narrow down your options to machines that excel in speed and efficiency while maintaining accuracy—crucial for high-quality solder paste application on chip boards.
Moreover, think about future scalability; investing in a machine that accommodates growth can save you from additional costs down the line. If you anticipate changes in PCB design or a shift towards more complex assemblies, flexibility becomes key. Ultimately, understanding your unique requirements will guide you toward an SMT chip mounter machine that not only meets today’s demands but also adapts to tomorrow’s challenges.
Budget Considerations
Analyze both upfront costs and long-term operational expenses including maintenance and potential upgrades. While it might be tempting to go for a lower-priced option initially, consider how features such as advanced pick-and-place technology could enhance efficiency over time.
Additionally, factor in hidden costs like training personnel or downtime during installation when calculating your budget for PCB assembly equipment. A well-chosen machine can yield significant returns through improved productivity and reduced errors in solder paste application during printed circuit assembly processes. Remember: investing wisely now means better profitability later!
Vendor Reputation and Support
As with any significant purchase decision, vendor reputation plays a pivotal role when selecting an SMT chip mounter machine. Research potential suppliers’ track records regarding customer service and technical support; after all, even the best machines may encounter issues requiring expert assistance down the line. Look for vendors who are known not just for their quality products but also for providing comprehensive support throughout the life cycle of their machines.
Additionally, consider seeking out reviews or testimonials from other companies within your industry who have utilized these vendors' services before making a commitment. A reputable vendor will often offer training sessions on proper operation techniques which can enhance productivity during printed circuit assembly tasks right from day one! Partnering with established manufacturers ensures you're not just buying a product but gaining access to valuable resources that contribute positively toward your overall PCB production and assembly goals.
Conclusion
In the ever-evolving landscape of printed circuit assembly (PCA), selecting the right SMT chip mounter machine is crucial for maximizing efficiency and ensuring quality. The features of these machines directly influence the speed and accuracy of PCB production and assembly processes, setting the stage for successful outcomes. By focusing on key attributes such as precision, flexibility, and advanced technologies, businesses can elevate their PCB design capabilities to new heights.
Maximizing Efficiency with the Right Features
To truly maximize efficiency in PCB assembly, it's essential to invest in an SMT chip mounter machine that meets specific production needs. Key features like speed and accuracy play a pivotal role in enhancing throughput while minimizing errors during solder paste application on chip boards. When these machines are equipped with advanced pick-and-place technology and robust vision systems, they not only streamline operations but also ensure that each component is positioned flawlessly.
Moreover, flexibility in component handling allows manufacturers to adapt quickly to varying production demands without sacrificing quality or speed. This adaptability is vital in an industry where rapid changes can occur due to technological advancements or market shifts. Ultimately, choosing the right features will empower companies to achieve optimal performance in their PCB production and assembly efforts.
Future Trends in SMT Technology
The future of SMT technology promises exciting developments that will further revolutionize the printed circuit assembly landscape. Innovations such as artificial intelligence (AI) integration into SMT chip mounter machines are set to enhance decision-making processes during assembly operations, leading to improved efficiency and reduced downtime. Additionally, advancements in automation will likely result in more sophisticated robotics integration within these machines, enabling higher levels of precision during PCB design.
Sustainability is another trend gaining traction within this space; manufacturers are increasingly looking for eco-friendly solutions that minimize waste during PCB production and assembly processes. As companies strive for greener practices while maintaining high-quality standards, we can expect a surge in energy-efficient models designed with sustainability at their core. Keeping an eye on these trends will be crucial for businesses aiming to stay competitive.
Partnering with Bensun for Solutions
For those navigating the complex world of SMT chip mounter machines, partnering with Bensun offers a strategic advantage when it comes to finding tailored solutions for your unique needs. With extensive experience in providing cutting-edge equipment for printed circuit assembly applications, Bensun understands what it takes to optimize your PCB production and assembly processes effectively. Their commitment to customer support ensures you have access to ongoing assistance long after your initial purchase.
By collaborating with Bensun, you gain insights into the latest technologies while benefiting from expert guidance tailored specifically to your business requirements—whether you're focused on improving solder paste application or enhancing overall operational efficiency on your chip boards. In this fast-paced industry where innovation reigns supreme, having a reliable partner like Bensun by your side can help you navigate challenges while unlocking new opportunities for growth.