Introduction
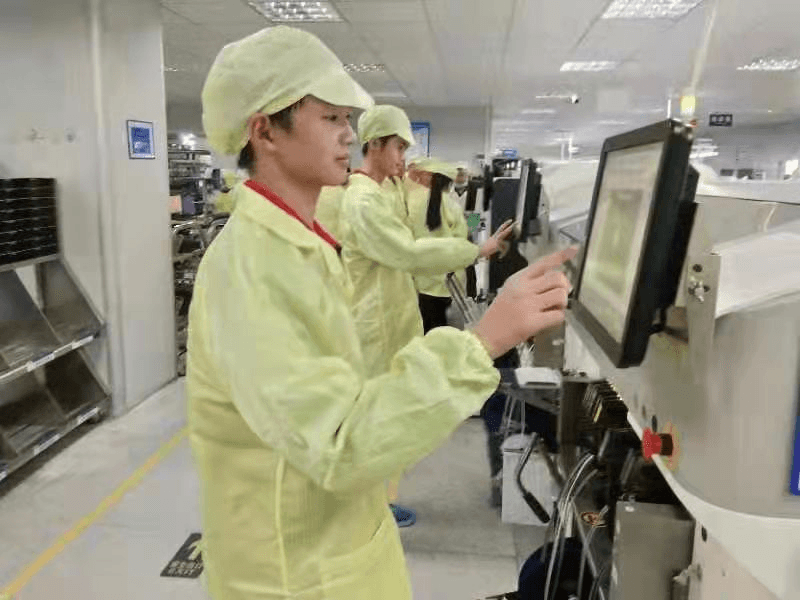
In the ever-evolving landscape of electronics, the demand for efficient and reliable PCB assembly is paramount. At the heart of this process lies the auto insertion machine for PCB assemblies, a pivotal tool that streamlines circuit card assembly. Understanding how these machines operate and their significance in PCB production and assembly can greatly enhance manufacturing efficiency.
Understanding Auto Insertion Machines
Auto insertion machines are designed to automate the placement of electronic components onto printed circuit boards, significantly reducing manual labor and increasing speed. These machines can handle various assembly types, including both through-hole and surface mount technologies, making them versatile for different PCB board assembly requirements. By leveraging advanced technology, manufacturers can achieve high precision in their PCB assembly and manufacturing processes.
Importance of PCB Assembly Efficiency
Efficiency in PCB assembly is not just a buzzword; it directly impacts production costs and time-to-market for electronic products. An effective auto insertion machine for PCB assemblies reduces errors that often occur during manual insertion, thereby minimizing rework and waste in circuit card assembly. As competition intensifies in the electronics sector, optimizing efficiency becomes essential for maintaining a competitive edge.
Key Factors in Machine Selection
When selecting an auto insertion machine for your PCB production and assembly needs, several key factors come into play. First, consider your specific volume requirements—higher volumes may necessitate more advanced automation features to keep up with demand. Additionally, compatibility with various types of PCBs and components is crucial to ensure flexibility as your product lines evolve over time; after all, you want a machine that grows with your business!
Assessing Your PCB Assembly Needs
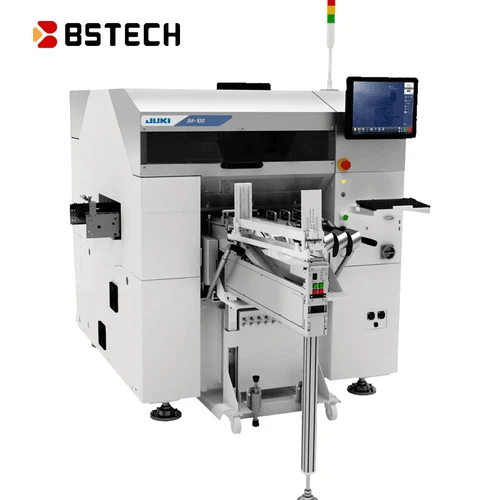
When it comes to selecting the right auto insertion machine for PCB assemblies, understanding your specific assembly needs is crucial. This section will guide you through evaluating circuit card assembly volume, identifying PCB board assembly specifications, and balancing cost with production requirements. By thoroughly assessing these factors, you can make an informed decision that aligns with your production goals.
Evaluating Circuit Card Assembly Volume
The first step in assessing your PCB assembly needs is evaluating your circuit card assembly volume. This involves determining how many units of each design you expect to produce over a given period, which directly influences the type of auto insertion machine for PCB assemblies you'll need. High-volume production may require more advanced machinery capable of handling increased throughput without sacrificing quality.
Understanding the volume not only helps in choosing the right equipment but also impacts overall efficiency and cost-effectiveness in PCB production and assembly. If you're looking at low to medium volumes, a more flexible machine might suffice; however, high-volume operations often necessitate machines designed for speed and precision in PCB assembly and manufacturing. Ultimately, knowing your expected output will guide you toward a solution that meets both current and future demands.
Identifying PCB Board Assembly Specifications
Next on the agenda is identifying the specific specifications required for your PCB board assembly projects. Factors such as board size, component types (like through-hole or surface mount), and complexity all play significant roles in determining which auto insertion machines are suitable for your needs. Different designs may require varying levels of automation and precision; hence understanding these specs helps narrow down options.
Moreover, compatibility with various components can affect how efficiently an auto insertion machine performs during production runs. For instance, if you're working with mixed technology boards that incorporate both surface mount devices (SMDs) and traditional through-hole components, you'll need a versatile machine capable of handling both types seamlessly within one workflow—this flexibility can significantly enhance efficiency in PCB assembly processes.
Balancing Cost and Production Requirements
Finally, balancing cost with production requirements is essential when selecting an auto insertion machine for PCB assemblies. While it's tempting to opt for the cheapest option available, this approach can lead to higher long-term costs due to inefficiencies or maintenance issues down the line—especially if it doesn't meet your specific needs effectively during peak production times.
Consider not just the upfront price tag but also factors like operational costs associated with running different models over time—think energy consumption rates or potential downtime due to maintenance on less reliable machines used in circuit card assemblies. Striking a balance between quality features that enhance productivity while keeping an eye on budget constraints ensures that you invest wisely in equipment that supports sustainable growth within your business's PCB production and assembly endeavors.
Features to Look for in Auto Insertion Machines
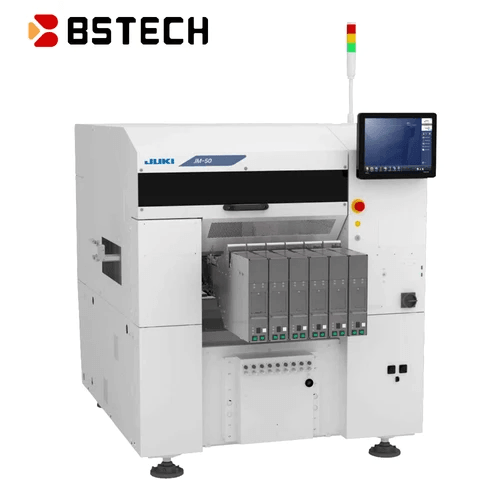
When selecting an auto insertion machine for PCB assemblies, it's crucial to consider the features that will best meet your production needs. The right specifications can significantly enhance your circuit card assembly process, ensuring efficiency and accuracy. This section will delve into the key specifications, automation levels, and compatibility factors that are essential for optimal PCB assembly.
Key Specifications for PCB Assembly and Manufacturing
The specifications of an auto insertion machine directly influence its performance in PCB assembly and manufacturing. Look for machines with high-speed insertion capabilities, as this can drastically reduce cycle times during production runs of circuit card assemblies. Additionally, precision is vital; machines should offer accurate placements to minimize rework and scrap rates in PCB board assembly operations.
Another specification worth noting is the range of component sizes the machine can handle. A versatile auto insertion machine can accommodate various components from tiny surface mount devices (SMDs) to larger through-hole parts, making it adaptable to different PCB designs and assembly requirements. Furthermore, consider the machine's ability to integrate with existing systems; seamless compatibility ensures a smoother workflow in your overall PCB production and assembly process.
Automation Levels for Enhanced Efficiency
Automation plays a pivotal role in enhancing efficiency within PCB assembly lines. An auto insertion machine equipped with advanced automation features can significantly reduce labor costs while increasing throughput rates during circuit card assembly tasks. Look for machines that offer programmable settings, allowing operators to quickly switch between different product lines without extensive downtime.
Moreover, automated inspection systems are invaluable; they help identify defects early in the production process of PCB assemblies, thus reducing costly errors down the line. The level of automation you choose should align with your production volume—higher volumes typically benefit from more sophisticated automated solutions tailored specifically for high-speed PCB assy operations.
Compatibility with Various PCB and Assembly Types
Compatibility is another critical feature when selecting an auto insertion machine for your specific needs in PCB board assembly and manufacturing processes. Ensure that the machine supports various types of PCBs—rigid boards, flexible circuits, or even hybrid designs—to accommodate diverse project requirements effectively. This flexibility not only saves time but also allows you to diversify your product offerings without investing heavily in new equipment.
Additionally, consider how well the machine integrates with other equipment used in your facility; a compatible system ensures smooth transitions between different stages of production—from initial design through final inspection—in your overall PCB production and assembly workflow. Ultimately, choosing an auto insertion machine that is versatile enough to handle multiple types of PCBs will enhance productivity while minimizing disruptions during changes or upgrades.
Brand Reputation and Reliability
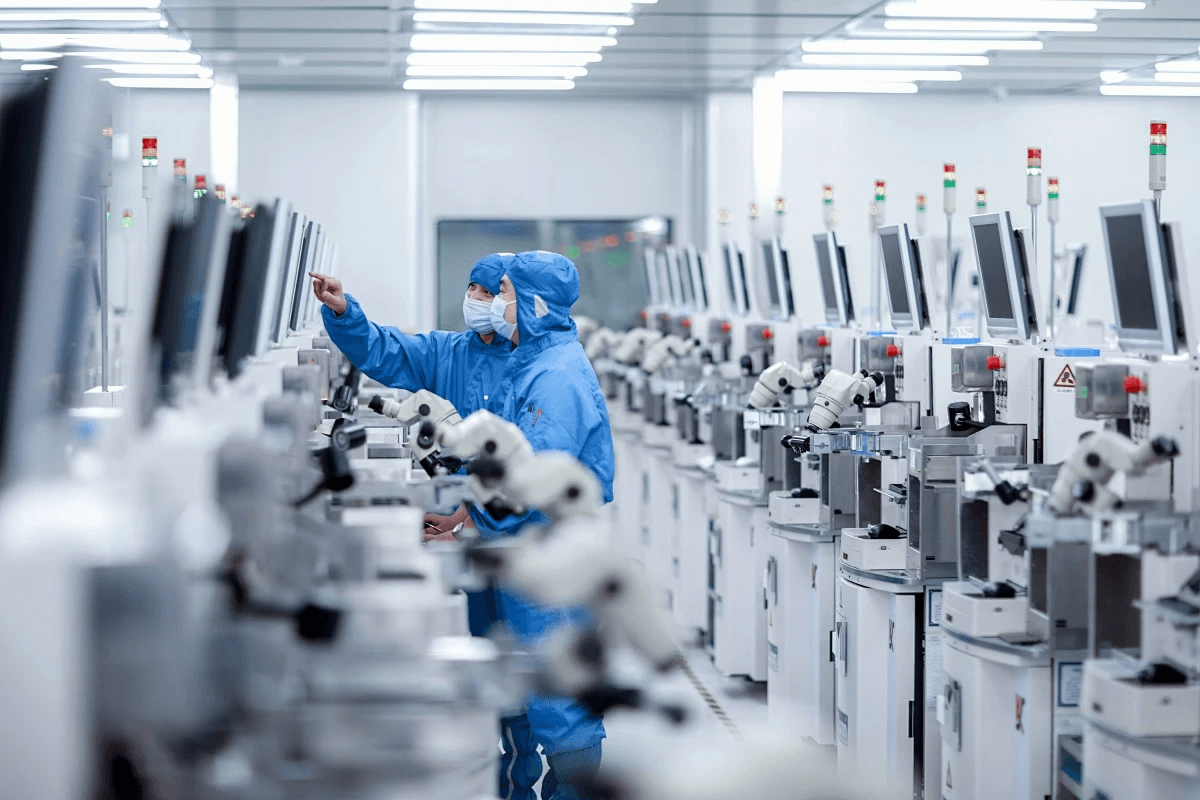
When investing in an auto insertion machine for PCB assemblies, brand reputation and reliability are paramount. The market is filled with various manufacturers, but not all offer the same level of quality or support. Established names in the industry often have a proven track record of delivering durable machines that meet the rigorous demands of PCB assembly and manufacturing.
Reviewing Established Names in the Industry
The landscape of auto insertion machines is dominated by a few key players known for their innovation and reliability. Companies like Panasonic, Juki, and Universal Instruments have made significant strides in circuit card assembly technology, consistently delivering high-quality products tailored to customer needs. Their longstanding presence in the market means they’ve had time to refine their offerings based on user feedback and advancements in PCB production and assembly techniques.
In addition to performance, these established brands often provide extensive resources for training and support, ensuring that customers can maximize their investment in an auto insertion machine for PCB assemblies. When selecting a machine, it’s wise to consider these reputable brands as they typically offer robust warranties and service agreements that can save you from potential headaches down the road.
Bensun Technology: A Case Study
Bensun Technology stands out as a compelling case study within the realm of auto insertion machines for PCB assemblies. Known for its cutting-edge solutions tailored specifically for modern manufacturing challenges, Bensun has carved out a niche by focusing on flexibility and efficiency in circuit card assembly processes. Their machines boast advanced features that cater to both through-hole and surface mount technology, making them versatile options for various types of PCB board assembly.
What sets Bensun apart is its commitment to customer satisfaction; they not only manufacture reliable equipment but also emphasize after-sales support which is crucial when integrating new machinery into existing workflows. By examining Bensun's approach to product development and customer service, businesses can glean important insights into what makes an effective partner in their PCB assembly journey.
Importance of Warranty and Support
When investing significant capital into an auto insertion machine for PCB assemblies, warranty terms should never be overlooked. A solid warranty not only protects your investment but also reflects the manufacturer's confidence in their product's longevity—an essential factor considering the complexities involved in circuit card assembly processes. Moreover, robust after-sales support ensures that any issues arising during operation can be addressed swiftly without disrupting your production schedule.
Reliable support services also include access to spare parts or technical assistance when needed; this capability helps maintain optimal performance levels throughout the life cycle of your equipment used in PCB production and assembly tasks. Ultimately, choosing a machine backed by strong warranty terms and responsive customer service will contribute significantly to your operational efficiency while minimizing downtime risks associated with equipment failures.
Comparing Different Models and Technologies
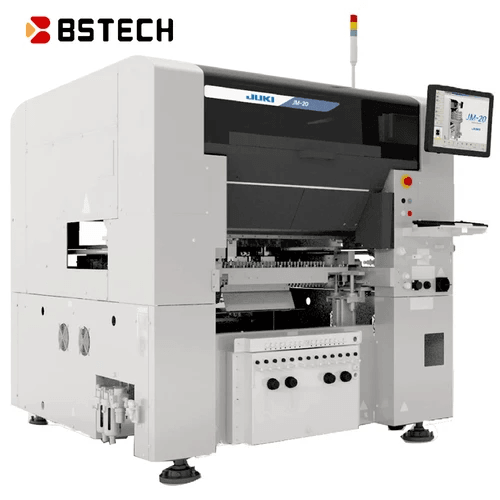
When it comes to selecting the right auto insertion machine for PCB assemblies, understanding the differences between various models and technologies is crucial. This section will delve into the nuances of through-hole versus surface mount technology, explore speed and accuracy metrics, and discuss maintenance considerations that can impact your PCB production and assembly processes.
Through-Hole vs. Surface Mount Technology
Through-hole technology (THT) has been a staple in circuit card assembly for decades, allowing components to be inserted through holes in the PCB board assembly. This method provides excellent mechanical strength but can be more labor-intensive compared to its modern counterpart—surface mount technology (SMT). SMT allows for smaller components to be mounted directly onto the surface of PCBs, facilitating higher density layouts and faster production speeds, making it a popular choice in today’s fast-paced PCB assembly and manufacturing landscape.
Choosing between these technologies often depends on your specific needs in PCB production and assembly. If your projects require robust connections or involve larger components, THT might be preferable. Conversely, if you're aiming for efficiency with compact designs, SMT could be the way to go.
Analyzing Speed and Accuracy Metrics
Speed and accuracy are paramount when evaluating auto insertion machines for PCB assemblies. The throughput of a machine—measured in units per hour—can significantly impact your overall circuit card assembly efficiency. Additionally, accuracy is vital; even minor misalignments during assembly can lead to costly rework or product failures down the line.
When comparing models, look at specifications like placement speed (how quickly components are placed) alongside first-pass yield rates (the percentage of correctly assembled boards on the first attempt). Machines that excel in both areas will enhance your PCB board assembly process while minimizing waste—a win-win situation for any manufacturer focused on quality.
Understanding Maintenance and Longevity
Maintenance plays a critical role in ensuring that your auto insertion machines remain reliable over time. Regular upkeep not only extends the life of your equipment but also helps maintain optimal performance levels during PCB assembly operations. Consider how easy it is to access parts for routine checks or repairs when evaluating different models; some machines offer user-friendly designs that simplify this process.
Additionally, longevity should factor into your decision-making process when selecting an auto insertion machine for PCB assemblies. Investing in equipment known for durability may save you money down the road by reducing downtime associated with repairs or replacements—an essential consideration in high-volume production environments where every minute counts.
Budgeting for Your Investment
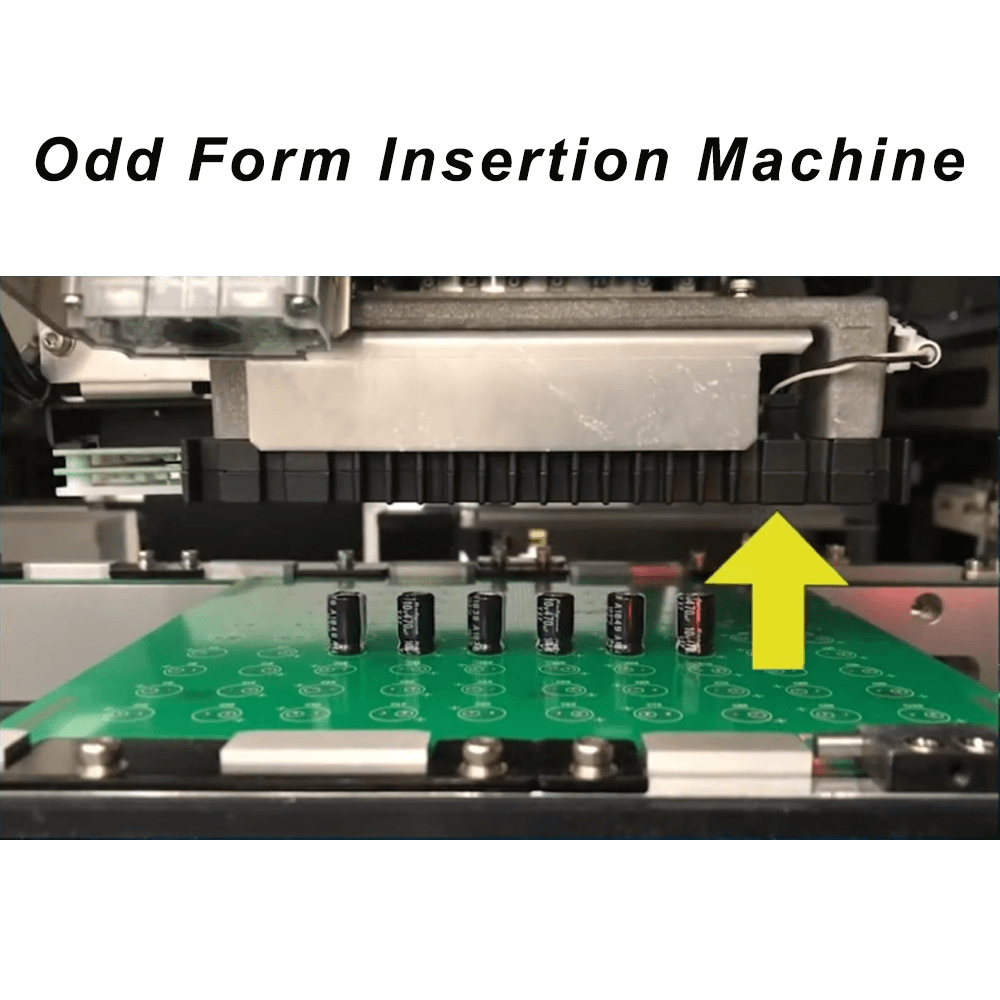
When diving into the world of PCB assembly, budgeting effectively is crucial to ensure a successful investment in an auto insertion machine for PCB assemblies. Understanding the total cost of ownership (TCO) will help you navigate not just the initial purchase price but also ongoing operational expenses. By evaluating all these factors, you can make a more informed decision that aligns with your circuit card assembly needs.
Evaluating Total Cost of Ownership
The total cost of ownership includes not only the upfront costs associated with purchasing an auto insertion machine for PCB assemblies but also maintenance, training, and operational costs over time. Consider aspects such as energy consumption and the cost of replacement parts when calculating TCO; these factors can significantly impact your budget in the long run. Additionally, factoring in potential downtime during maintenance or repairs is essential to get a comprehensive view of what owning a PCB assembly machine entails.
Hidden Costs in PCB Production and Assembly
While evaluating your budget, it's important to be aware of hidden costs that can sneak up on you during PCB production and assembly. For instance, insufficient training for staff on using the new equipment can lead to inefficiencies and errors that ultimately increase production costs. Moreover, consider expenses related to software updates or integration with existing systems; these costs can add up quickly if not planned for ahead of time.
Financing Options for Equipment Purchases
Financing options are often available when investing in high-cost equipment like an auto insertion machine for PCB assemblies, making it easier to manage cash flow while acquiring essential tools for your business. Look into leasing options or loans specifically designed for manufacturing equipment; many financial institutions offer favorable terms tailored to businesses in this sector. Additionally, some manufacturers may provide financing plans directly through their sales teams, which could include attractive rates or deferred payment options tailored specifically to your needs.
Conclusion
In the fast-paced world of electronics, selecting the right auto insertion machine for PCB assemblies is critical for optimizing your circuit card assembly process. The efficiency of your PCB production and assembly hinges on understanding your specific needs, evaluating features, and considering brand reliability. By keeping these key factors in mind, you can streamline your PCB board assembly operations and enhance overall productivity.
Summarizing Key Considerations for Selection
When choosing an auto insertion machine for PCB assemblies, it’s essential to assess both volume and specifications to ensure compatibility with your circuit card assembly requirements. Features like automation levels and adaptability to various types of PCB and assembly processes can significantly impact your efficiency. Additionally, don’t overlook the importance of brand reputation; established names often provide reliable support that can save you headaches down the line.
Making an Informed Decision for PCB Assembly
Making an informed decision in the realm of PCB assembly means weighing all options against your unique production demands. Consider how different models perform regarding speed and accuracy metrics—after all, a fast machine is only as good as its precision! Balancing cost with performance will help you identify which auto insertion machine aligns best with your long-term goals in PCB assembly and manufacturing.
Next Steps for Your PCB Production Journey
Now that you’ve gathered vital information about auto insertion machines for PCB assemblies, it’s time to take action! Start by creating a shortlist of potential models that meet your criteria and arrange demonstrations or trials if possible. This hands-on experience will provide invaluable insights into how each option fits into your existing workflow, setting you up for success in future circuit card assembly projects.