Introduction
In the ever-evolving world of electronics, understanding the nuances of assembly methods is crucial for designers and manufacturers alike. Among these methods, SMT surface mount technology has gained significant traction due to its efficiency and compactness. However, exploring through-hole technology offers valuable insights into traditional practices that still hold relevance today.
Understanding SMT Surface Mount Basics
SMT, or surface mount technology, revolutionizes how electronic components are attached to circuit boards. Unlike traditional methods, where components are inserted through holes in the board, SMT allows components to be mounted directly onto the surface. This shift not only optimizes space but also enhances performance by minimizing signal paths and improving thermal management.
Exploring Through-Hole Technology Insights
Through-hole technology (THM) has been a staple in electronics manufacturing for decades, offering robust connections ideal for high-stress environments. It involves inserting component leads through holes drilled into a printed circuit board (PCB) and soldering them on the opposite side. While THM provides certain advantages in terms of durability and ease of handling larger components, it often falls short in terms of space efficiency compared to SMT.
Importance of Choosing the Right Method
Choosing between SMT and THM isn't merely a matter of preference; it's about aligning with specific project requirements and constraints. Factors such as design flexibility, production efficiency, reliability, and cost all play pivotal roles in this decision-making process. By thoroughly understanding what is the surface mount technology process SMT entails versus its through-hole counterpart, designers can make informed choices that optimize both performance and budget considerations.
Definition and Overview
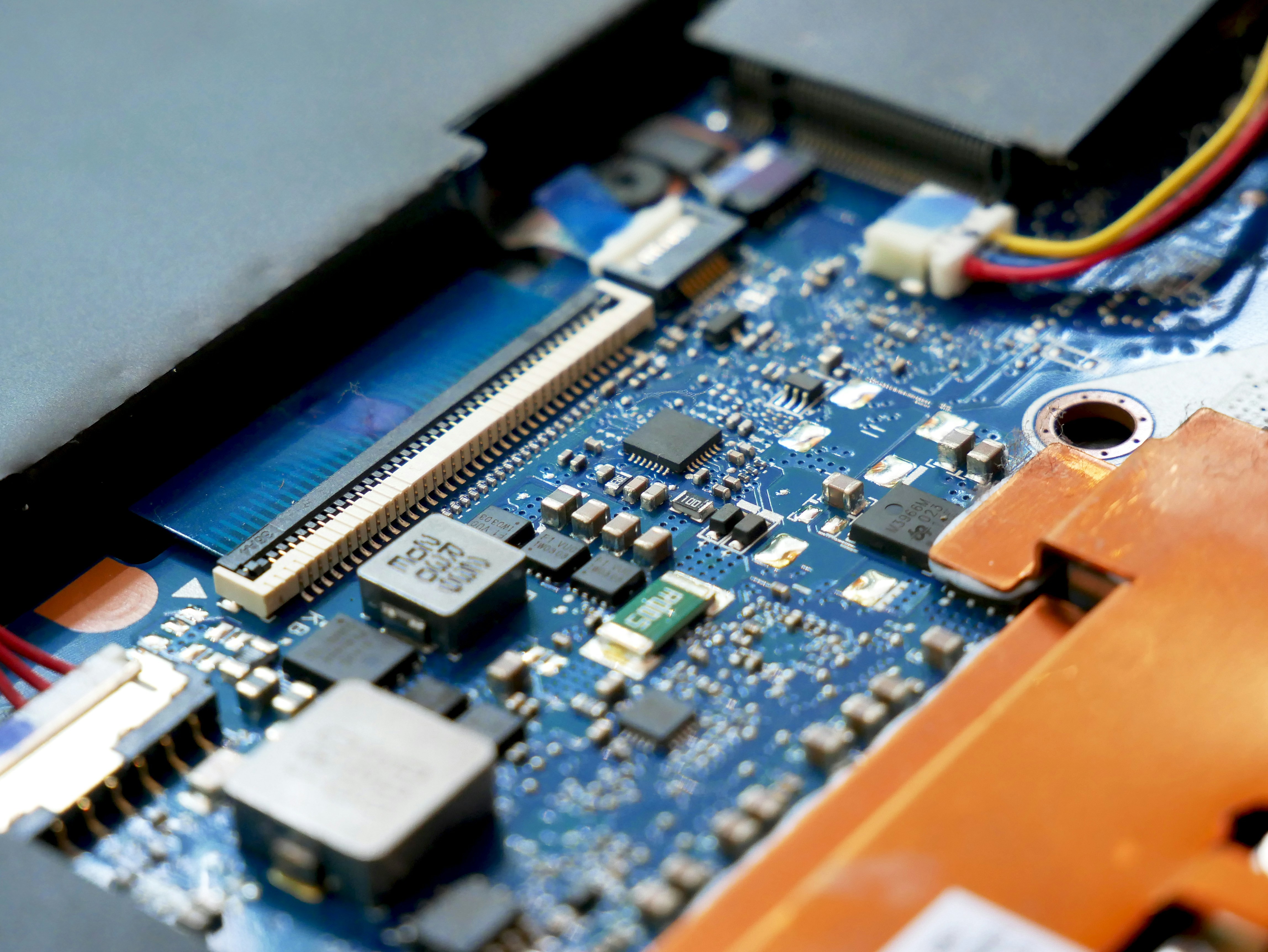
In the ever-evolving world of electronics, understanding the fundamental differences between surface mount technology (SMT) and through-hole technology (THM) is crucial for making informed design decisions. These two methods serve as the backbone of modern circuit board assembly, each with its unique characteristics and applications. Let’s dive into what makes SMT tick, explore the key features of THM, and see how Bensun Technology plays a pivotal role in this landscape.
What is Surface Mount Technology?
Surface mount technology (SMT) refers to a method where electronic components are mounted directly onto the surface of printed circuit boards (PCBs). This process allows for smaller components to be used, enabling more compact designs that can accommodate complex circuitry. The surface mount technology process involves various steps including solder paste application, component placement using automated machines, and reflow soldering to secure components in place.
When comparing SMT vs SMD (surface-mounted devices), it's essential to note that SMDs are the actual components used in SMT processes. Essentially, all SMDs are designed for use with SMT techniques; however, not all SMT processes involve SMDs exclusively—there could be exceptions based on design requirements. Understanding these nuances helps clarify what sets SMT apart from traditional assembly methods like THM.
Key Features of Through-Hole Technology
Through-hole technology (THM), on the other hand, involves inserting leads of electronic components through holes drilled into a PCB and then soldering them on the opposite side. This method offers robust mechanical support due to the physical connection created by soldering leads through holes in the board. The key features of THM include greater durability for high-stress applications and ease of repair or replacement for individual components.
However, when discussing what is the difference between SMT and THM, one must consider size constraints; THM requires more space on a PCB compared to its surface-mount counterpart. Additionally, while THM can handle higher power applications better due to larger component sizes and heat dissipation capabilities, it often falls short in terms of production efficiency when compared with modern SMT processes.
The Role of Bensun Technology in SMT
Bensun Technology has carved out a niche within the realm of surface mount technology by providing innovative solutions tailored specifically for efficient PCB assembly using SMT processes. Their expertise not only streamlines manufacturing but also enhances quality control measures throughout production cycles. By integrating advanced automation technologies into their operations, Bensun stands at the forefront of optimizing both speed and precision in assembling SMDs onto PCBs.
The company’s commitment to excellence ensures that clients benefit from reduced lead times while maintaining high standards for reliability—a critical factor when evaluating performance metrics associated with both SMT and THM approaches. In an industry where every second counts and precision is paramount, Bensun's contributions significantly elevate overall efficiency within electronic manufacturing sectors.
Manufacturing Process Comparison
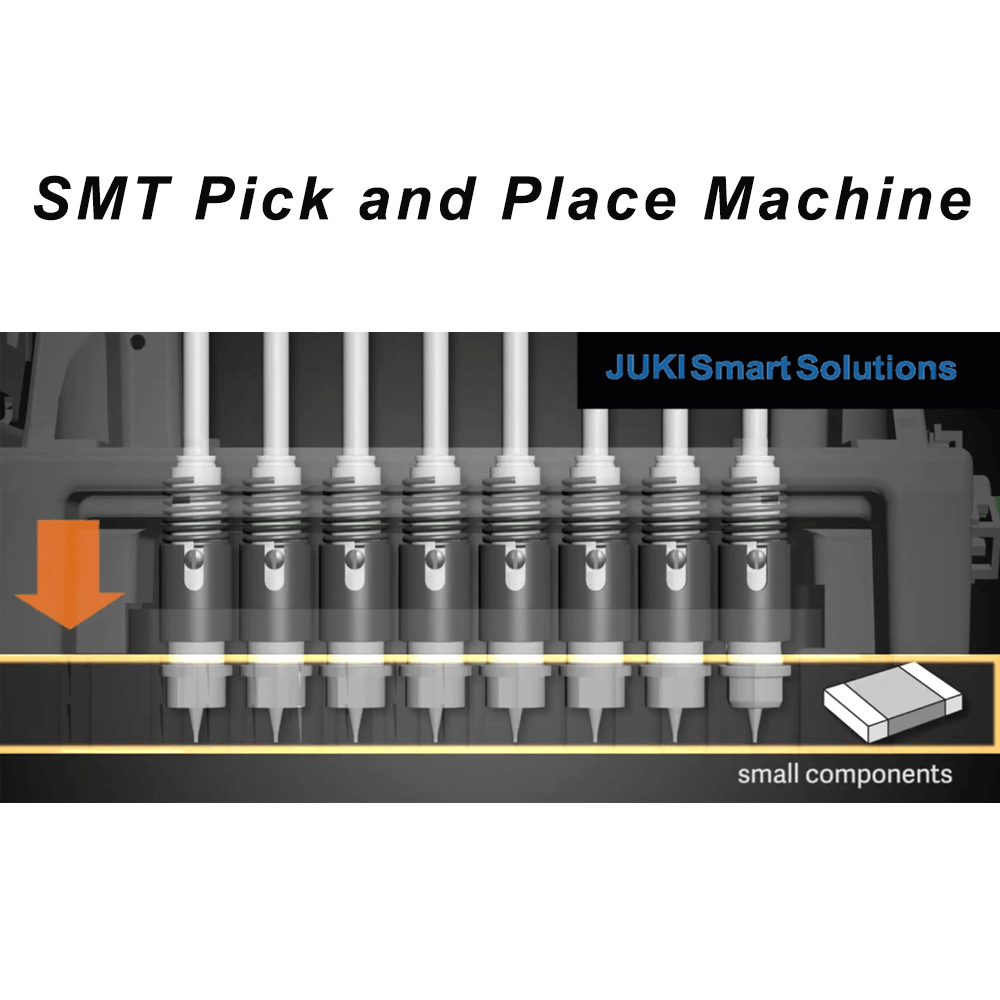
SMT Surface Mount Process Explained
The SMT surface mount process involves placing electronic components directly onto the surface of printed circuit boards (PCBs) rather than inserting them through holes as in traditional methods. This process begins with applying solder paste to the PCB using a stencil, followed by placing components onto the paste using pick-and-place machines. Once all components are positioned, they undergo reflow soldering, where heat is applied to melt the solder and secure the components in place.
What is the surface mount technology process SMT? It’s a streamlined approach that allows for higher component density on PCBs, which can lead to smaller and lighter devices. Additionally, this method often results in faster assembly times compared to through-hole techniques due to automation and reduced handling.
Through-Hole Technology Process Details
Through-hole technology (THM) consists of a different assembly approach where leads from components are inserted into drilled holes on a PCB and then soldered on the opposite side. The process starts with drilling holes into the PCB followed by inserting leads through these holes before soldering them either manually or via wave soldering techniques. While this method provides strong mechanical bonds and durability for larger components, it can be labor-intensive and time-consuming.
What is the difference between SMT and THM? Primarily, THM is suited for larger components requiring robust connections but lacks some design flexibility found in SMT processes. In contrast, through-hole methods can limit component placement options due to their size constraints compared to surface-mounted designs which offer more versatility.
Efficiency in Production: SMT vs THM
When evaluating efficiency in production between SMT surface mount and THM, it's clear that SMT generally holds an advantage due to its automated processes and ability for high-density component placement. With machines capable of placing thousands of components per hour versus manual insertion methods used in THM, manufacturers often experience shorter lead times with SMT setups.
Moreover, what is the difference between SMD (Surface Mount Device) and SMC (Surface Mount Component)? While both refer to similar technologies involving surface mounting techniques, SMD typically refers specifically to devices designed for use with these techniques while SMC encompasses all types of passive or active electronic parts used in conjunction with them.
In summary, while both manufacturing processes have their merits based on specific applications or requirements—SMT tends toward greater efficiency and compactness whereas THM offers robust connections—the choice ultimately depends on project goals regarding cost-effectiveness and design needs.
Component Placement and Design
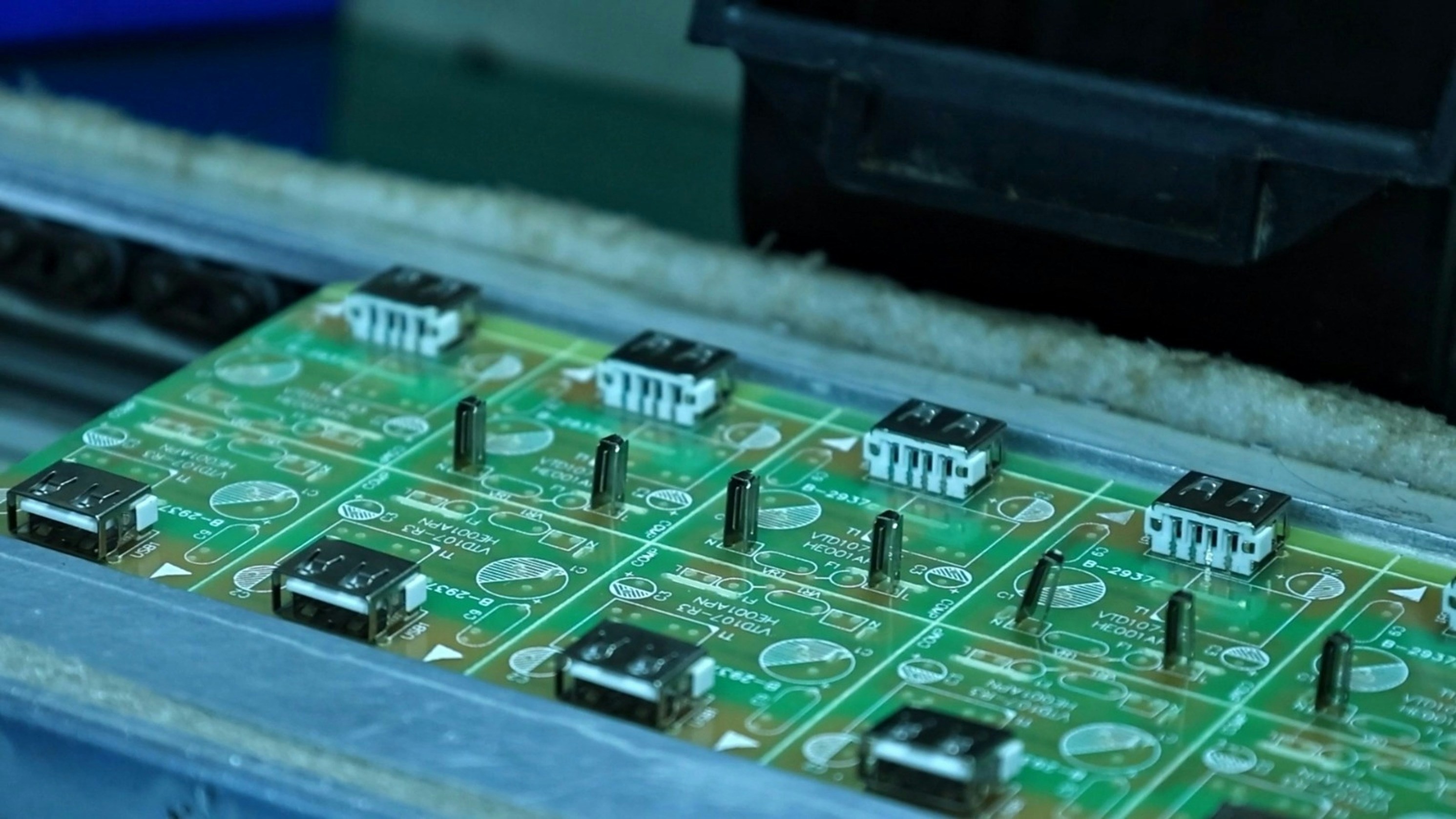
When it comes to component placement and design, the choice between SMT (Surface Mount Technology) and THM (Through-Hole Mounting) can significantly impact the overall efficiency and functionality of a circuit board. SMT surface mount technology offers unparalleled flexibility in design, allowing engineers to create compact layouts that maximize space utilization. This section delves into the advantages of SMT, the limitations of through-hole placements, and real-world applications that showcase the effectiveness of SMT.
Advantages of SMT in Design Flexibility
One of the standout features of SMT surface mount technology is its ability to facilitate intricate designs without compromising on performance. With smaller components that can be placed on both sides of a PCB (Printed Circuit Board), designers have more leeway to experiment with complex configurations. Additionally, this increased density not only saves space but also enhances electrical performance by reducing the length of connections—something that’s crucial in high-frequency applications.
Moreover, using SMT allows for automated assembly processes which streamline production timelines and minimize human error during component placement. This automation is vital for scaling up production while maintaining quality control standards. When comparing what is SMT vs SMD (Surface-Mounted Device), it becomes clear that both terms refer to similar technologies; however, SMD specifically denotes components designed for use with surface mount techniques.
Limitations of Through-Hole Component Placement
While through-hole technology has its merits—such as providing robust mechanical support—its limitations are hard to ignore in today’s fast-paced electronic landscape. One significant drawback is the larger footprint required for through-hole components, which can hinder design flexibility and lead to wasted space on PCBs. This limitation makes it challenging to create compact devices that are increasingly demanded by consumers.
Additionally, through-hole mounting often involves more manual labor during assembly due to its more complex insertion process compared to what is the surface mount technology process SMT? The labor-intensive nature not only slows down production but can also increase costs significantly when compared with automated surface mount assembly methods. As engineers weigh their options between SMT and THM, these limitations become pivotal considerations in their decision-making process.
Real-World Applications Highlighting SMT
The versatility of smt surface mount technology shines brightly in various real-world applications across multiple industries. From smartphones packed with tiny circuits to advanced medical devices requiring precise engineering, SMT has proven indispensable for modern electronics manufacturing. In sectors like automotive or aerospace where reliability is paramount, employing smt ensures optimal performance while keeping weight low—a critical factor for fuel efficiency.
Furthermore, consumer electronics benefit immensely from the rapid advancements made possible by using surface mount techniques; think about how sleek your latest gadget looks! By leveraging what is the difference between SMD and SMC (Surface Mount Components), manufacturers can fine-tune their designs even further based on specific requirements or constraints posed by their products’ functionalities or environments they operate within.
In summary, as we explore component placement options within electronic design frameworks, it's evident that smt offers substantial advantages over traditional through-hole methods while also presenting exciting possibilities for future innovations.
Reliability and Performance Factors
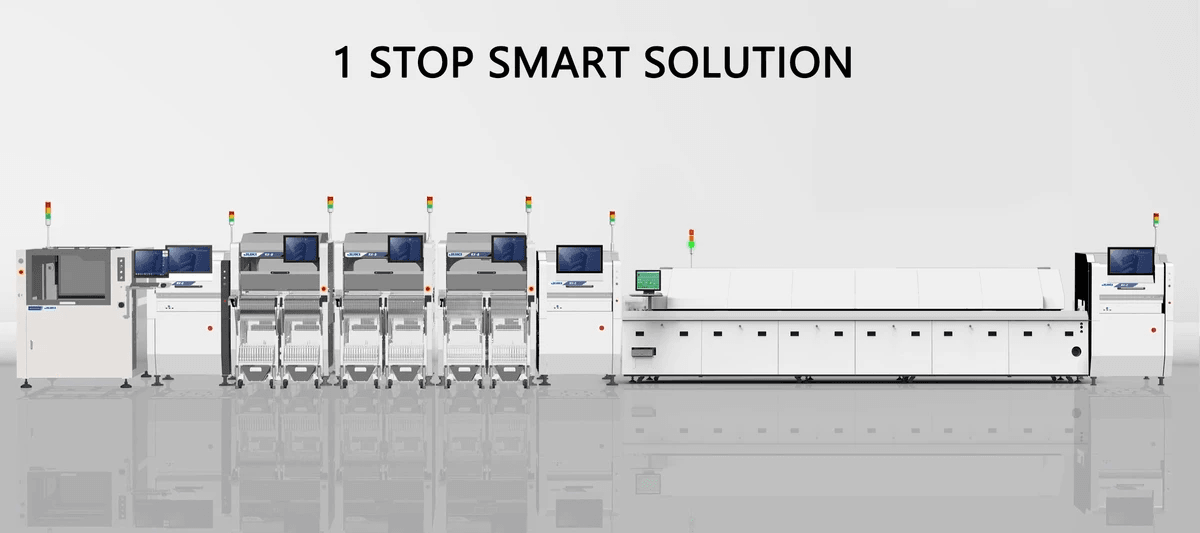
Reliability and performance are crucial when comparing different electronic assembly methods. In this section, we will delve into the nuances of SMT surface mount technology, investigate what sets it apart from SMD (Surface Mount Device), and explore how these factors affect production efficiency. Understanding these elements can help manufacturers make informed decisions about component placement technologies.
Comparing Reliability: SMT vs SMD
When discussing reliability in the context of SMT surface mount technology, it's essential to clarify that SMD refers to the components themselves, while SMT is the process used to attach these components to a printed circuit board (PCB). Thus, comparing SMT vs SMD boils down to evaluating how well the process supports component reliability. Generally, SMT tends to offer enhanced mechanical stability due to its compact design and lower profile, which can be particularly beneficial in high-vibration environments.
Moreover, as we consider what is the surface mount technology process SMT entails, it becomes clear that this method often results in fewer solder joint failures compared to traditional through-hole methods. This leads us into a discussion about how effective soldering techniques within SMT contribute significantly to long-term reliability. Ultimately, understanding these distinctions helps manufacturers choose between various technologies while ensuring optimal performance for their applications.
Surface Mount vs Through-Hole in Production
The production dynamics of surface mount technology versus through-hole mounting (THM) reveal several advantages for SMT. One major difference between SMT and THM lies in their assembly speed; the surface mount technology process allows for automated placement of components on both sides of a PCB simultaneously. This capability not only increases throughput but also reduces labor costs associated with manual assembly processes typical of through-hole methods.
Additionally, when evaluating reliability during production phases, it’s evident that SMTs tend to have better thermal management properties due to their smaller footprint. This leads us back to our earlier point regarding mechanical stability; less thermal stress translates into fewer defects over time when compared with THM systems. Understanding these differences equips manufacturers with insights necessary for optimizing production lines based on specific project requirements.
Performance Metrics of SMT Technology
Performance metrics play a pivotal role in assessing the effectiveness of any manufacturing method—especially when comparing smt surface mount technology against alternatives like THM or even SMC (Surface Mount Component). Key metrics often include defect rates during assembly and overall product longevity post-assembly; here again, SMR tends to shine brightly due primarily because its design minimizes stress on solder joints.
Furthermore, what is the difference between SMD and SMC? While both terms relate closely within the realm of surface mounting technologies—SMD being more focused on component type while SMC encompasses broader applications—their performance metrics must also be evaluated under similar conditions for meaningful comparisons. With lower defect rates attributed largely due improved soldering techniques inherent in smt processes combined with advanced inspection methods employed today—manufacturers can confidently lean toward this technology for reliable outcomes.
In conclusion, understanding reliability factors associated with smt surface mount provides valuable insights into component placement choices available today while ensuring optimal performance across various applications.
Cost Implications for Assembly
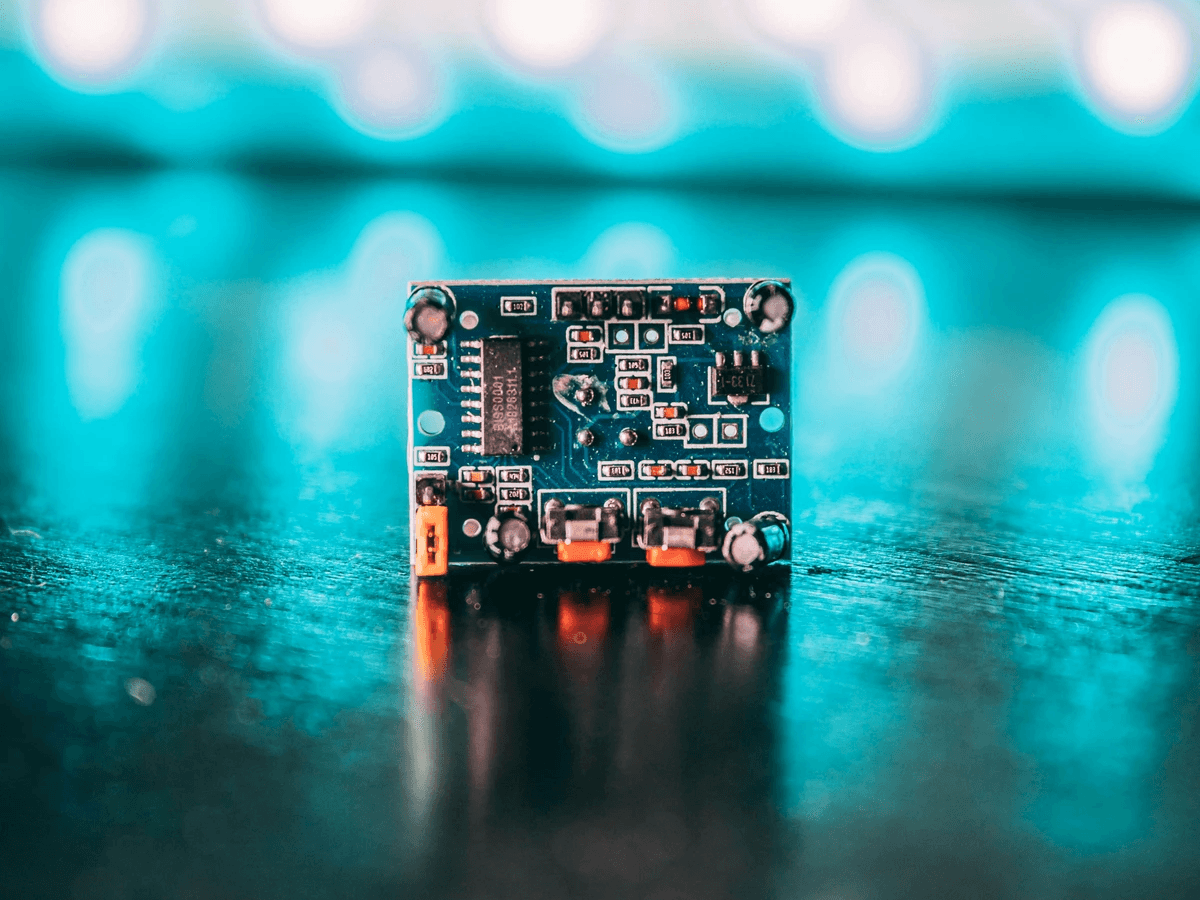
When it comes to assembly, cost implications can significantly influence the decision between SMT surface mount and through-hole technology (THM). Understanding the financial aspects of each method is crucial for manufacturers looking to optimize their production processes. In this section, we’ll delve into the cost efficiency of SMT surface mount, examine financial considerations for through-hole assembly, and ultimately help you navigate the budgetary landscape.
Cost Efficiency in SMT Surface Mount
SMT surface mount technology has gained popularity largely due to its cost efficiency. The surface mount technology process allows for higher component density on printed circuit boards (PCBs), which reduces material costs and saves space. Additionally, because SMT components are often smaller and lighter than their through-hole counterparts, shipping and handling costs can also be lowered.
Another factor contributing to cost efficiency in SMT is the speed of assembly. Automated pick-and-place machines can quickly position components on a PCB, reducing labor costs associated with manual assembly found in THM processes. This rapid production capability means that companies can achieve economies of scale more easily when utilizing SMT surface mount technology.
Moreover, since the manufacturing process for SMT typically requires fewer steps than traditional THM methods, companies can save on both time and resources. The streamlined nature of the surface mount technology process not only enhances productivity but also minimizes waste, further driving down overall costs.
Financial Considerations for Through-Hole Assembly
While through-hole assembly may have been a staple in electronics manufacturing for decades, its financial implications often raise eyebrows when compared to SMT options. One significant drawback is that through-hole components tend to be larger and more expensive than their surface-mounted equivalents. This size difference not only impacts material costs but also leads to increased shipping expenses due to bulkier packaging requirements.
Additionally, the manual labor involved in THM can inflate production costs considerably. Assembling through-hole components usually requires more time-consuming processes like drilling holes in PCBs and soldering each component individually—tasks that demand skilled laborers whose wages add up quickly over time. Consequently, businesses might find themselves grappling with higher overheads as they rely on traditional methods.
Furthermore, as electronic devices become increasingly miniaturized and complex, relying solely on THM may limit design possibilities and lead to obsolete inventory issues down the line. This potential waste adds another layer of financial concern that manufacturers need to consider when weighing their options between SMT vs SMD or even comparing SMD with SMC technologies.
The Bottom Line: Choosing Based on Budget
Ultimately, choosing between SMT surface mount and through-hole technology boils down to budgetary constraints alongside performance needs. For companies aiming for high-volume production at lower costs per unit while maintaining quality standards, investing in SMT is often a no-brainer due to its inherent efficiencies and scalability advantages over traditional methods like THM.
However, it's essential not just to look at initial setup costs but also long-term implications such as maintenance expenses or potential redesigns if market demands shift towards more compact solutions requiring advanced technologies like SMD or even SMC approaches down the road.
In conclusion, while both methodologies have their merits depending on specific project requirements—such as what is the difference between SMT and THM—the growing trend leans heavily toward embracing smt surface mount techniques given their affordability without sacrificing reliability or performance metrics.
Conclusion
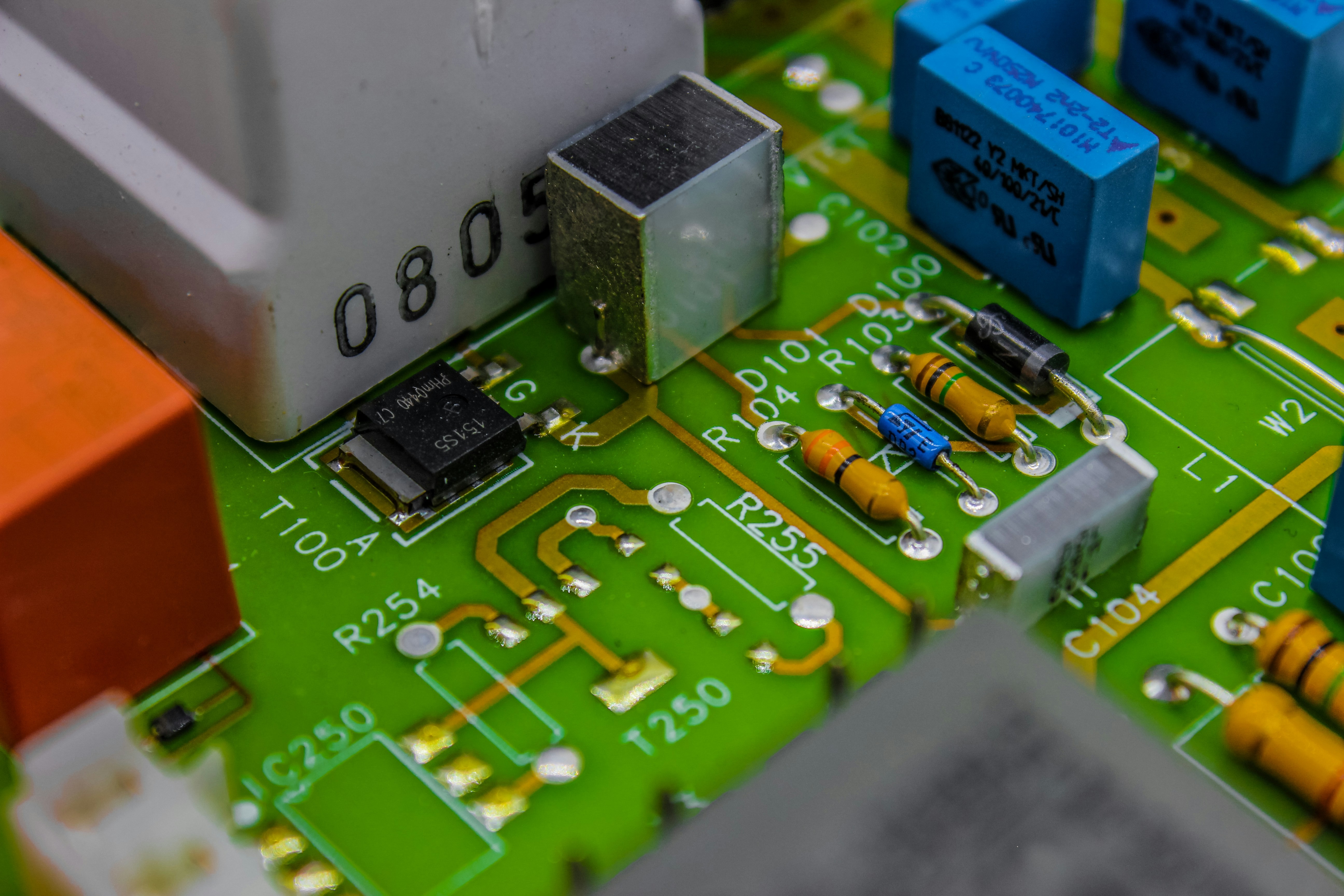
In the world of electronics, understanding the differences between SMT surface mount technology and through-hole mounting (THM) is crucial for making informed decisions. Each method has its unique advantages and applications that cater to specific needs, whether it’s in terms of design flexibility, manufacturing efficiency, or cost implications. Ultimately, the choice between SMT and THM can significantly influence the performance and reliability of your electronic devices.
Key Takeaways on SMT Surface Mount vs THM
When comparing SMT surface mount technology with through-hole mounting (THM), several key takeaways emerge. First, SMT offers a more compact design that allows for greater density of components on a circuit board, which is invaluable in modern electronics where space is at a premium. In contrast, THM provides stronger mechanical connections but often results in larger boards with limited component placement options.
Furthermore, the surface mount technology process streamlines production cycles by enabling automated assembly techniques that reduce labor costs and improve efficiency. Understanding what is SMT vs SMD also highlights that while both involve surface mounting techniques, SMD refers specifically to discrete components designed for this method. Thus, knowing these distinctions helps manufacturers optimize their designs according to their specific needs.
Final Thoughts on Component Placement Choices
Choosing between SMT surface mount technology and through-hole mounting involves evaluating various factors such as component size, application requirements, and production capabilities. While SMT excels in high-density applications where miniaturization is essential, THM might be preferable for prototyping or when dealing with larger components requiring robust connections. Ultimately, understanding what is the difference between SMT and THM will empower engineers to make choices that align with their project goals.
Moreover, considering real-world applications can provide insights into how these technologies perform under different conditions—whether it’s consumer electronics or industrial machinery—each has its place depending on reliability needs and environmental factors. Both methods have their merits; it's about finding the right fit for your project.
Selecting the Right Technology for Your Needs
In conclusion, selecting the right technology—be it SMT surface mount or through-hole—depends heavily on your specific requirements and constraints such as budgetary considerations and desired performance metrics. If speed and efficiency are paramount in production processes or if you're working with compact designs where every millimeter counts, then embracing SMT may be your best bet. Conversely, if you prioritize strength over size or are working with larger components that require firm grounding on circuit boards, then exploring through-hole options could serve you well.
Ultimately, weighing all these factors against your project's unique demands will help you navigate the complexities of electronic assembly processes effectively. Remember: whether you choose SMT or THM can significantly impact not just production costs but also product longevity and performance down the line.