Introduction
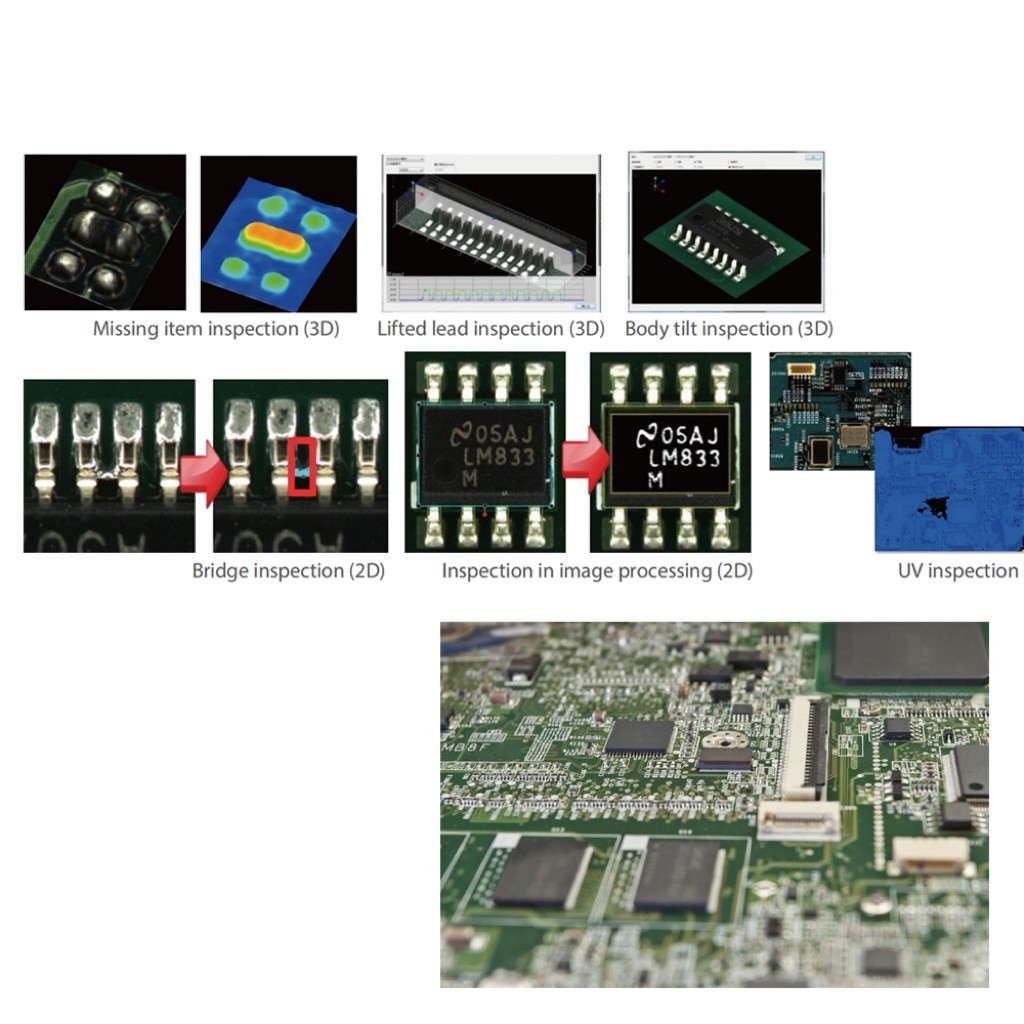
In the ever-evolving world of electronics, understanding SMD (Surface Mount Device) technology is crucial for anyone looking to navigate the terrain of modern circuit design. So, what does SMD mean in electronics? It refers to components that are mounted directly onto the surface of printed circuit boards (PCBs), allowing for a more compact and efficient assembly compared to traditional methods. As we explore SMT (Surface Mount Technology) further, we'll uncover its significance in revolutionizing how devices are built and their impact on overall performance.
What Is SMD in Electronics?
SMD in electronics signifies a leap towards miniaturization and efficiency, catering to the demand for smaller, more powerful devices. These tiny components can be found in everything from smartphones to medical devices, highlighting their versatility and importance. By understanding what SMD means in electronics, one can appreciate how it shapes our daily tech interactions.
Exploring SMT Technologies
Diving into SMT technologies reveals a landscape rich with innovation and advancement. This technique not only streamlines production but also enhances the reliability of electronic products through improved soldering processes and reduced component stress during assembly. As we delve deeper into these technologies, it becomes clear that they play a pivotal role in the future of electronic manufacturing.
Importance of SMD vs SMT
The distinction between SMD vs SMT is vital for grasping how modern electronics are designed and produced. While SMD refers specifically to the components themselves, SMT encompasses the broader methodology used for assembling these components onto PCBs efficiently. Understanding this difference highlights why manufacturers prioritize these technologies when optimizing device performance and functionality.
Overview of SMD and SMT
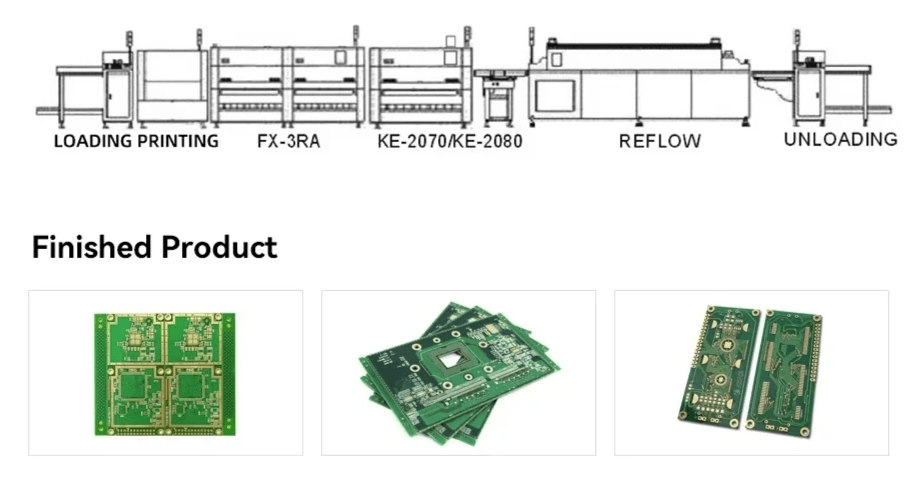
In the realm of electronics, understanding the distinction between SMD (Surface-Mount Device) and SMT (Surface-Mount Technology) is crucial for engineers and enthusiasts alike. These terms are often used interchangeably, but they refer to different aspects of electronic component assembly. So, what does SMD mean in electronics? Simply put, SMD refers to the actual components designed for surface mounting, while SMT encompasses the entire process of attaching these components to a PCB (Printed Circuit Board).
Definition of SMT and SMD
SMD is a type of electronic component that is designed to be mounted directly onto the surface of a PCB rather than through holes like traditional components. This design allows for smaller sizes and lighter weight, making them ideal for modern electronics that demand efficiency. On the other hand, SMT is the method by which these components are assembled onto PCBs; it involves techniques such as solder paste application and reflow soldering.
When exploring what is SMD vs SMT?, it's essential to recognize that one refers to the parts themselves (SMD), while the other describes how those parts are integrated into devices (SMT). This distinction becomes particularly important when discussing manufacturing processes or troubleshooting issues in electronic devices.
Key Differences Explained
The key differences between SMD and other types of components primarily lie in their construction and installation methods. Unlike through-hole components that require drilling holes into a PCB, SMDs have leads that are soldered directly onto pads on the board's surface—this results in reduced space requirements and increased design flexibility. Additionally, while both technologies serve similar functions in circuit boards, their applications can vary significantly based on size constraints and performance needs.
Understanding what is the difference between SMD and PCB helps clarify their respective roles in electronics manufacturing. The PCB serves as a foundational platform where various electronic components—including both SMDs and traditional ones—are mounted to create functional circuits. While PCBs provide structural support, it’s ultimately the choice between using SMD or other types that can affect overall device performance.
SMD vs PCB: Understanding the Roles
To further clarify this relationship: think of a PCB as a canvas upon which an artist paints with various types of electronic components—the brush strokes being either traditional or surface-mount techniques like those used with SMD Technologies. Each approach offers unique benefits; however, opting for SMD often leads to more compact designs which are particularly advantageous in consumer electronics where space is at a premium.
Moreover, discussing what is the difference between SMD and SMC (Surface-Mount Component) reveals another layer; while both involve surface mounting techniques, an SMC typically refers to specific types or classifications within broader categories like capacitors or resistors designed for surface mounting applications. Thus understanding these nuances can help engineers make informed decisions based on their project requirements.
In summary, distinguishing between these terms enhances comprehension not only about individual component functionality but also about how they interact within larger systems—making it easier than ever to navigate today's complex landscape of smd electronics manufacturing.
Advantages of SMT
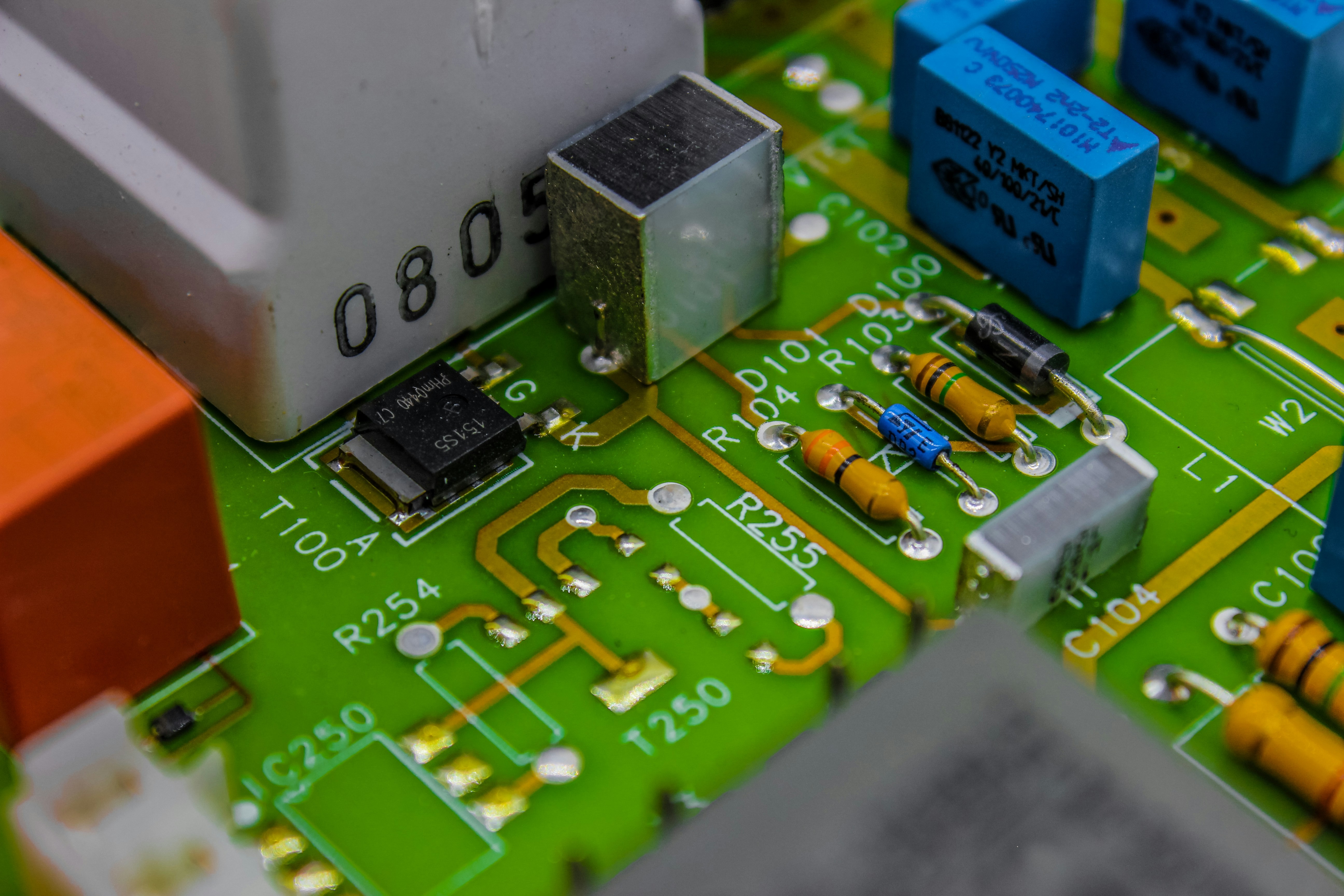
Surface Mount Technology (SMT) has revolutionized the world of electronics by offering a range of advantages that make it a preferred choice for many manufacturers. Among these benefits are space-saving capabilities, higher component density, and improved reliability and performance. Understanding these advantages can illuminate why SMT is often favored over traditional methods like through-hole technology.
Space-Saving Benefits
One of the most compelling advantages of SMT is its ability to save space on printed circuit boards (PCBs). By using smaller components that can be mounted directly onto the surface of the PCB, manufacturers can maximize the available real estate. This compact design is particularly beneficial in modern electronics where devices are becoming smaller and more portable, making SMD electronics indispensable in today’s tech landscape.
Moreover, this space efficiency allows for more intricate designs without compromising functionality. Engineers can fit more features into a device while keeping it lightweight and sleek—a crucial factor in consumer electronics like smartphones and laptops. Ultimately, this space-saving benefit not only enhances aesthetics but also contributes to overall system performance.
Higher Component Density
Higher component density is another remarkable advantage offered by SMT. Unlike traditional methods that require larger footprints for components, SMD technologies enable the placement of numerous small components in close proximity to one another on a single PCB. This increased density leads to enhanced functionality within a limited area, which is vital as electronic devices continue to evolve.
Additionally, higher component density facilitates complex circuit designs that were previously unattainable with older technologies like SMC (Surface Mount Components). The ability to incorporate more features into smaller spaces means engineers can innovate without being restricted by size constraints. As such, understanding what SMD means in electronics becomes crucial for anyone looking to grasp modern manufacturing techniques.
Improved Reliability and Performance
The reliability and performance enhancements associated with SMT cannot be overstated. With solder joints that are less prone to mechanical stress compared to their through-hole counterparts, SMD electronics typically exhibit superior durability under various conditions. This quality makes them particularly suitable for applications requiring long-term reliability—think automotive or aerospace sectors where failure is not an option.
Furthermore, the shorter electrical paths between components reduce signal loss and improve overall performance by enhancing speed and efficiency in data transmission. This improvement plays a significant role when comparing SMD vs SMT; while both technologies have their merits, SMT tends to provide better operational characteristics due to its design principles. As we delve deeper into SMD technologies in modern manufacturing, it becomes clear how these advantages contribute significantly toward innovation across industries.
Disadvantages of SMT
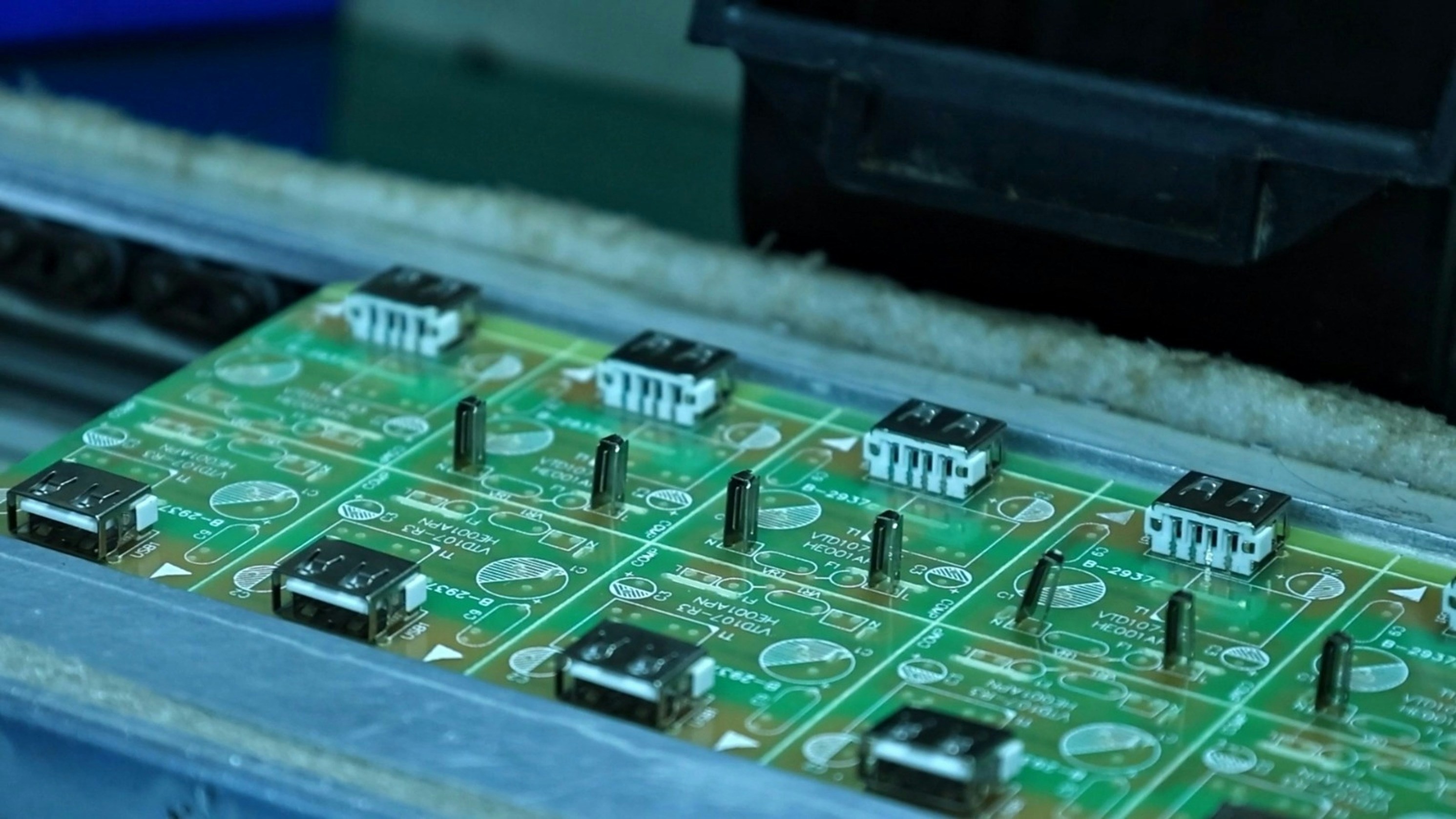
While Surface Mount Technology (SMT) has revolutionized the world of electronics, it does come with its own set of challenges that can be a bit daunting. Understanding these drawbacks is essential for anyone considering SMD technologies in their manufacturing processes. Let's delve into some of the key disadvantages associated with SMT.
Complexity in Repair and Maintenance
One major downside to using SMT is the complexity involved in repair and maintenance. When components are mounted directly onto the surface of a printed circuit board (PCB), accessing them for repairs can be quite tricky. Unlike traditional through-hole components, which can be easily desoldered and replaced, SMD electronics often require specialized tools and techniques that can complicate even routine maintenance tasks.
Equipment and Setup Costs
Another significant drawback lies in the initial investment required for equipment and setup costs when adopting SMT processes. The machines needed for placing SMD components are typically more expensive than those used for traditional soldering methods. Additionally, there’s often a learning curve associated with operating this equipment effectively, which can lead to increased training costs and longer setup times.
Challenges in Component Handling
Handling SMD components presents its own set of challenges that manufacturers must navigate carefully. These tiny parts are often more susceptible to damage during assembly or transport due to their size and fragility compared to larger through-hole components. Moreover, improper handling can lead to issues like static discharge damage or misalignment during placement on PCBs, further complicating the manufacturing process.
SMD Technologies in Modern Manufacturing
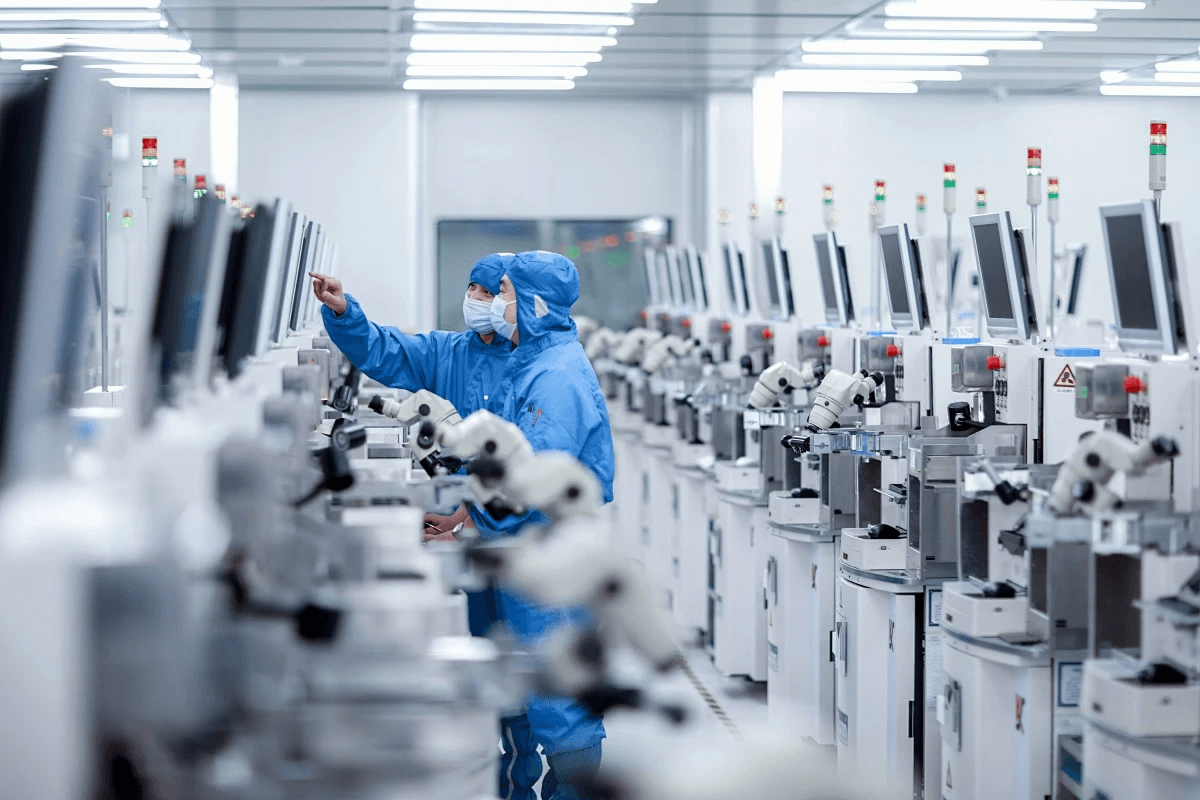
SMD technologies have revolutionized modern manufacturing, enabling a more efficient and compact design for electronic devices. In the realm of SMD electronics, companies are constantly pushing the envelope to enhance performance and reliability. This section will explore innovations by Bensun Technology, adaptive solutions for diverse needs, and the critical role of quality assurance in production.
Innovations by Bensun Technology
Bensun Technology has emerged as a leader in developing cutting-edge SMD technologies that cater to various industries. Their commitment to research and development has led to breakthroughs that redefine what SMD means in electronics today. From advanced soldering techniques to automated assembly processes, Bensun is setting new standards that enhance both efficiency and effectiveness in SMD manufacturing.
One notable innovation is their proprietary software that optimizes the placement of components on PCBs, significantly reducing errors during assembly. This software not only improves accuracy but also accelerates production timelines—an essential factor when considering what is the difference between SMD and PCB manufacturing processes. With such advancements, Bensun showcases how SMD technologies can lead to significant cost savings while maintaining high-quality output.
Furthermore, Bensun's focus on eco-friendly materials reflects a growing trend towards sustainability in electronics. By incorporating greener practices into their SMD technologies, they address environmental concerns while still delivering exceptional performance. This dedication not only benefits manufacturers but also aligns with consumer demands for sustainable products.
Adaptive Solutions for Diverse Needs
In today's fast-paced market, adaptability is key; hence, many manufacturers are seeking adaptive solutions within their SMD technologies. What does SMD mean in electronics? It signifies flexibility—something that companies like Bensun embrace wholeheartedly by offering customizable options tailored to specific industry requirements. Whether it’s automotive applications or consumer electronics, these solutions ensure that every client finds a perfect fit.
Moreover, as industries evolve and new challenges arise—such as miniaturization or increased functionality—the need for versatile SMD components becomes paramount. The difference between SMD and SMT lies not just in component type but also in how these components can be adapted for various applications across sectors. With innovative designs and robust engineering practices at play, manufacturers can swiftly pivot their strategies without compromising on quality or performance.
This adaptability extends beyond just product offerings; it encompasses entire production lines equipped with state-of-the-art machinery designed for quick adjustments based on demand fluctuations or technological advancements. Such agile systems make it easier than ever to integrate new features into existing designs without extensive downtime—a crucial advantage when considering what is the difference between SMD and SMT operational efficiencies.
Quality Assurance in Production
Quality assurance stands at the forefront of any successful manufacturing process involving SMD technologies; after all, consistent quality ensures reliability across all electronic devices produced using these methods. Companies like Bensun prioritize rigorous testing protocols throughout each phase of production to guarantee that every component meets stringent industry standards before reaching consumers' hands.
Understanding what is the difference between SMD and PCB requires recognizing how critical quality checks impact overall performance; a single faulty component could lead to device failure down the line—a risk no manufacturer can afford! Therefore, implementing comprehensive quality control measures—from initial design assessments through final inspections—becomes non-negotiable within this sphere of electronics manufacturing.
Additionally, advancements such as real-time monitoring systems allow manufacturers to detect issues early on during production runs rather than post-production—a significant leap forward compared with traditional methods where problems often went unnoticed until later stages (if at all). With such proactive approaches embedded into their processes around SMD technologies, companies ensure they remain competitive while delivering top-notch products consistently.
Comparing SMD and SMC
When diving into the realm of electronics, understanding the nuances between SMD (Surface Mount Device) and SMC (Surface Mount Component) becomes essential. While both technologies are integral to modern electronics manufacturing, they serve distinct purposes and come with unique characteristics. This section will illuminate what sets these two apart and help you grasp their applications in various industries.
Understanding SMD and SMC
To truly understand what does SMD mean in electronics, one must recognize that it refers to components designed for surface mounting on PCBs (Printed Circuit Boards). On the other hand, SMC encompasses a broader category that includes any surface-mounted component, whether it be resistors, capacitors, or integrated circuits. In essence, while all SMDs are technically SMCs due to their mounting style, not all SMCs qualify as SMDs since some may not adhere strictly to the smaller size criteria typical of SMD technologies.
Application Differences in Industry
When discussing the difference between SMD and PCB technology, it's crucial to consider their applications across various industries. For instance, in consumer electronics like smartphones and tablets where space is at a premium, manufacturers often prefer using compact surface mount devices for efficiency. Conversely, in industrial applications where robustness is key—think heavy machinery or automotive systems—surface mount components may be utilized for their durability but can sometimes take on larger sizes for better handling during repairs or replacements.
Choosing the Right Technology
Choosing between using an SMD or an SMC boils down to your specific needs within a project. If you're leaning towards high-density designs with space-saving benefits—like those found in modern smartphones—SMD technologies would likely be your best bet. However, if your application demands more ruggedness or easier maintenance without sacrificing too much space efficiency, then opting for standard surface mount components might be more prudent.
Conclusion
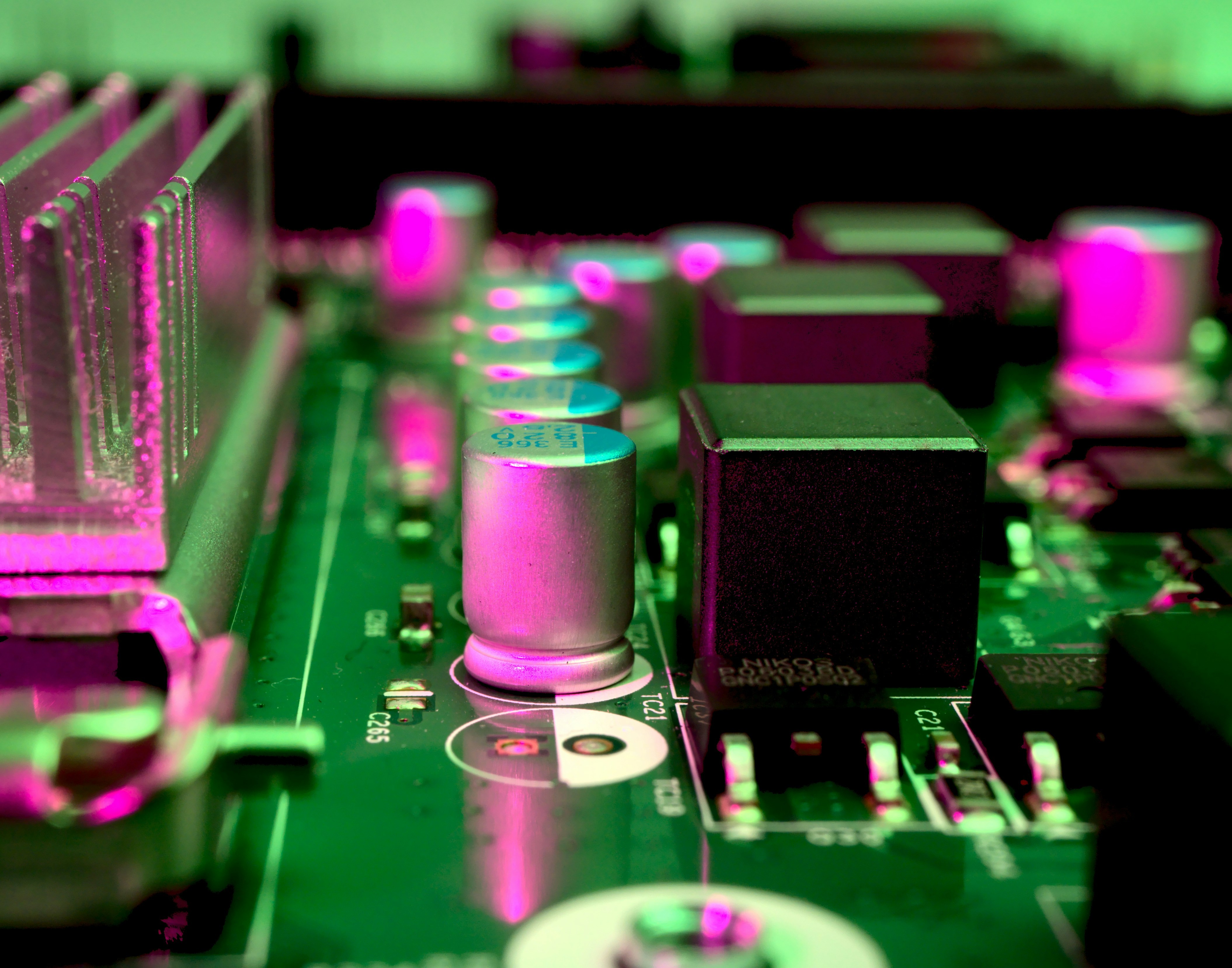
In wrapping up our exploration of SMD electronics, it’s clear that Surface Mount Device (SMD) technology has revolutionized the electronics landscape. The advantages of SMT, including space-saving benefits and enhanced performance, make it an attractive choice for modern manufacturing. However, understanding the nuances between SMD vs SMT and their respective applications is essential for making informed decisions in your projects.
Key Takeaways on SMT Advantages
One of the most significant advantages of SMT is its ability to facilitate higher component density on printed circuit boards (PCBs). This means that manufacturers can pack more functionality into smaller devices, a crucial factor in today’s compact electronic designs. Additionally, improved reliability and performance are hallmarks of SMD technologies, making them a preferred option for industries where precision is paramount.
Pitfalls to Consider with SMT
Despite its numerous benefits, there are pitfalls to consider when working with SMD technologies. Complexity in repair and maintenance can pose challenges; once an SMD component fails, replacing it may require specialized skills or equipment not readily available in all workshops. Moreover, the initial setup costs can be daunting for small businesses looking to adopt these advanced techniques.
Future Trends in SMD Technologies
Looking ahead, the future trends in SMD technologies promise exciting developments that could further enhance their utility across various industries. Innovations such as adaptive solutions tailored to specific manufacturing needs will likely emerge, enabling even greater flexibility and efficiency in production processes. As we continue to push the boundaries of what is possible with electronics design and fabrication, staying informed about advancements will be key for engineers and manufacturers alike.