Introduction
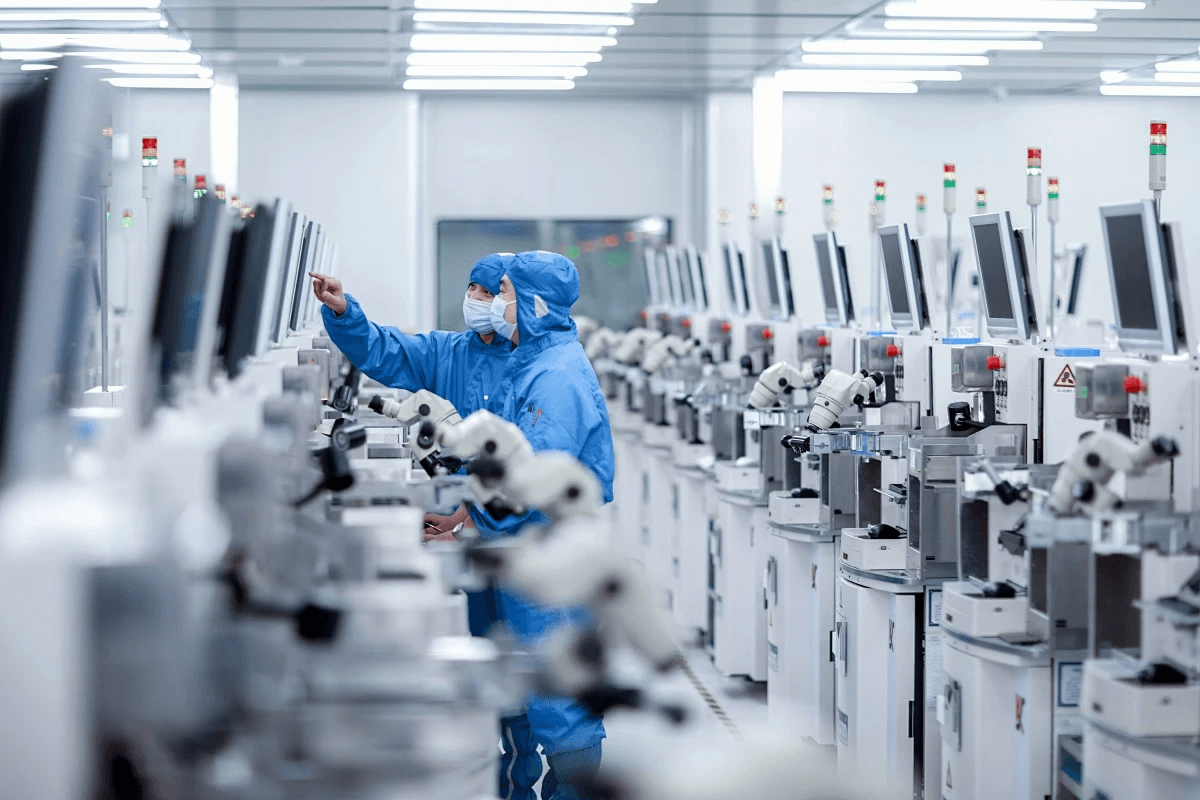
In the realm of electronics manufacturing, understanding the intricacies of an SMT line is crucial for anyone looking to delve into this high-tech industry. The term What is a SMT line? often pops up in discussions about modern production techniques, and for good reason; these lines are at the heart of efficient electronic assembly processes. By utilizing Surface Mount Technology (SMT), manufacturers can achieve higher precision and faster production rates, making it a cornerstone of contemporary electronics.
Understanding SMT Line Basics
An SMT line is essentially a streamlined assembly process designed for mounting electronic components directly onto printed circuit boards (PCBs). This method contrasts with traditional techniques like through-hole technology, offering numerous benefits that cater to the fast-paced demands of today's market. To fully appreciate what an SMT line entails, one must explore its core components and how they work synergistically to enhance productivity.
Importance of SMT in Electronics Manufacturing
The significance of SMT in electronics manufacturing cannot be overstated; it has revolutionized how devices are assembled and has led to smaller, lighter products with enhanced functionality. As consumer electronics continue to evolve, the demand for compact designs necessitates efficient methods like those provided by an SMT line. Understanding What does SMT stand for?—Surface Mount Technology—highlights its pivotal role in meeting these modern challenges.
Advantages of Using SMT Technology
One major advantage of using SMT technology is its ability to accommodate a wide range of component sizes and types, allowing for greater design flexibility compared to older methods such as DIP (Dual In-line Package). Additionally, the reduced footprint that comes with surface-mounted components means more efficient use of space on PCBs, which ultimately leads to lower manufacturing costs. With questions like What is the difference between SMD and SMT? frequently arising, it's clear that understanding these nuances can provide valuable insights into optimizing production lines.
What is a SMT Line?
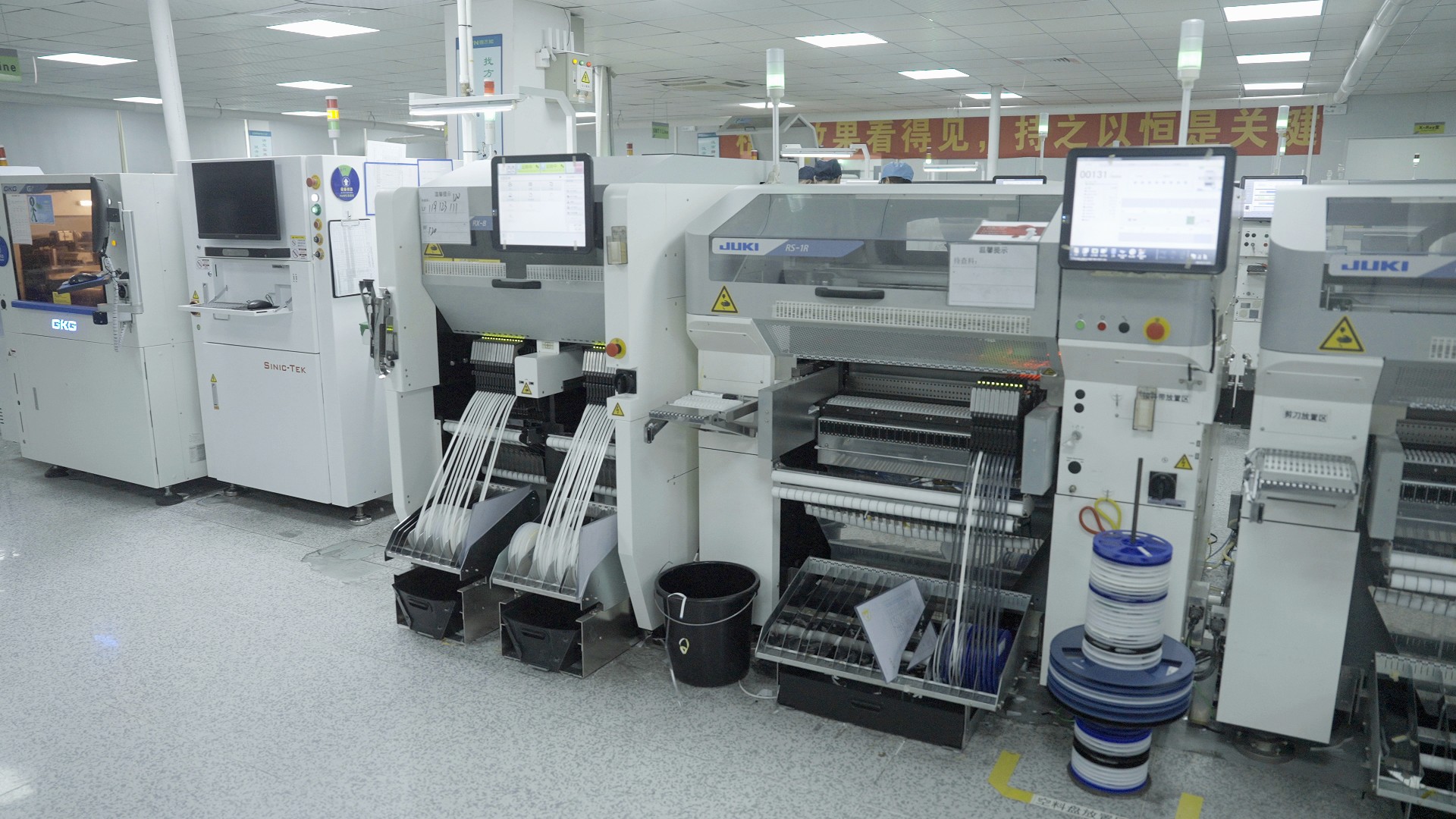
When diving into the world of electronics manufacturing, understanding what a SMT line is becomes essential. A Surface Mount Technology (SMT) line is a specialized assembly line designed for the efficient placement of electronic components directly onto the surface of printed circuit boards (PCBs). This process not only streamlines production but also enhances the overall quality and reliability of electronic devices.
Definition and Purpose of SMT Line
So, what is a SMT line? At its core, it’s an assembly system that automates the mounting of SMD (Surface Mount Device) components onto PCBs. The primary purpose of an SMT line is to optimize the production process by allowing for higher component density and reduced board space compared to traditional methods. This efficiency translates into faster production times and lower costs, making it an attractive option for manufacturers.
Core Components of a SMT Line
The anatomy of a typical SMT line consists of several key components that work in harmony to achieve optimal results. These include solder paste printers, pick-and-place machines, reflow ovens, and inspection systems—all crucial in ensuring precision and quality throughout the assembly process. Each component plays a vital role in answering questions like What is the SMT production line process? as they collectively contribute to seamless integration from start to finish.
Role of Bensun Technology in SMT Lines
Bensun Technology stands out as a leader in providing cutting-edge solutions for SMT lines across various industries. Their innovative equipment enhances efficiency while maintaining high standards in quality control—elements critical when discussing what are SMT Line and DIP Line differences or applications. By incorporating advanced technology into their machinery, Bensun ensures that manufacturers can meet evolving demands while maximizing productivity on their SMT lines.
What Does SMT Stand For?
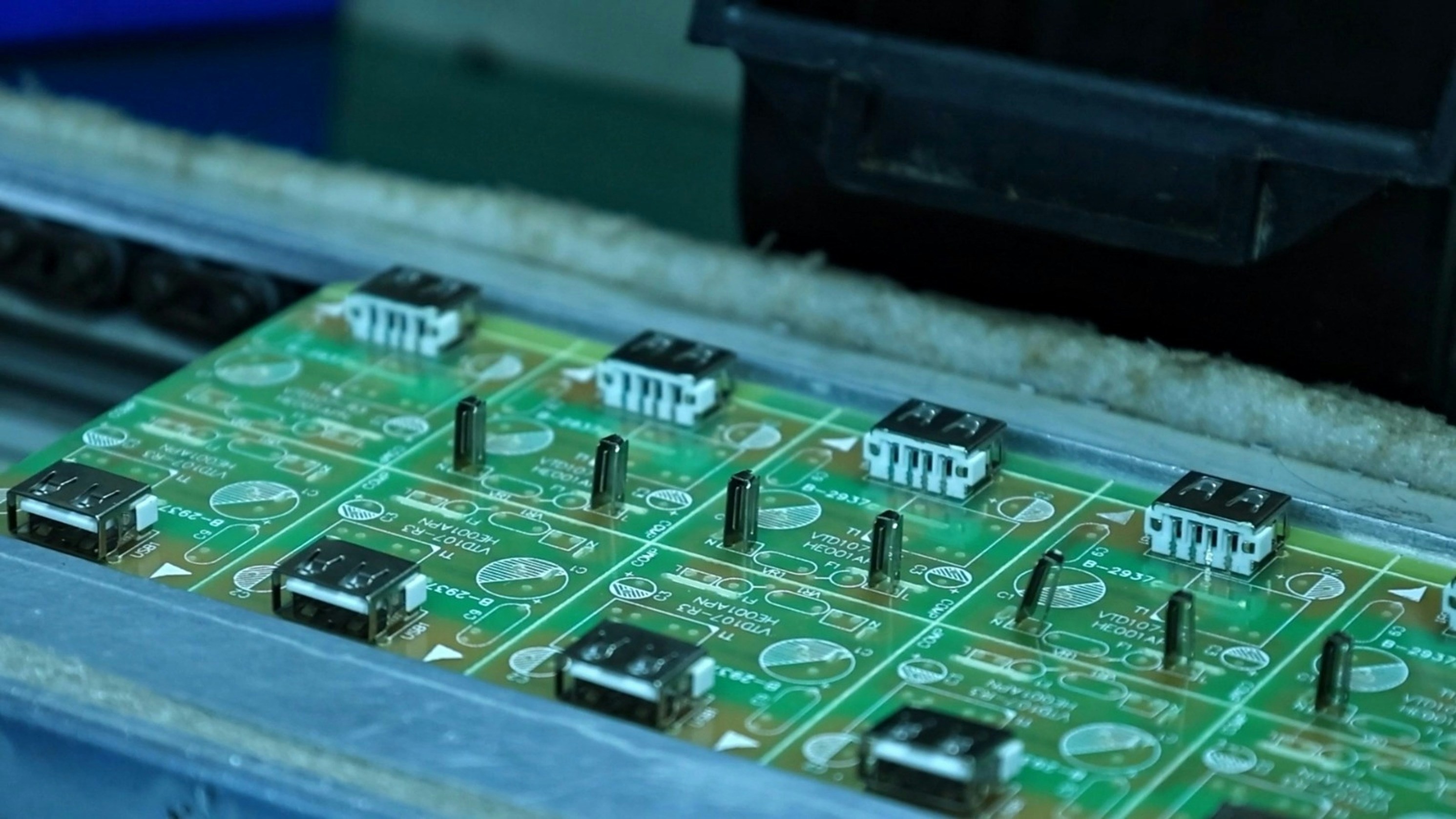
When diving into the world of electronics manufacturing, one term that frequently comes up is SMT, which stands for Surface Mount Technology. This innovative approach revolutionizes how electronic components are mounted onto circuit boards, allowing for more compact designs and improved performance. Understanding what SMT stands for is crucial for anyone involved in the design or production of electronic devices.
Breakdown of Surface Mount Technology
Surface Mount Technology (SMT) refers to a method where electronic components are mounted directly onto the surface of printed circuit boards (PCBs). Unlike traditional through-hole technology, where leads pass through holes in the PCB, SMT allows for a much denser arrangement of components. This not only saves space but also enhances electrical performance and reliability.
In an SMT line, various components such as resistors, capacitors, and integrated circuits can be placed on both sides of the PCB simultaneously. The process typically involves automated machines that accurately position and solder these components onto the board. As a result, understanding what SMT stands for helps manufacturers optimize their production lines while maintaining high quality.
History and Evolution of SMT
The history of Surface Mount Technology dates back to the 1960s when engineers sought ways to improve component density on PCBs. Initially used primarily in military applications due to its complexity and cost, it gradually gained traction in consumer electronics throughout the 1980s and 1990s. Today, what does SMT stand for? It's synonymous with innovation in electronics manufacturing.
The evolution of SMT has been fueled by advances in materials science and automated assembly techniques. With each technological leap, manufacturers have been able to produce smaller yet more powerful devices that meet consumer demands for portability and functionality. The transition from bulky DIP (Dual In-line Package) components to sleek SMD (Surface Mount Device) packages showcases this evolution vividly.
As we explore what is a SMT line today, it’s essential to recognize how far we've come since those early days—transforming not just how we build electronics but also enabling new possibilities in design and application across industries.
Industry Standards and Practices
In any field as dynamic as electronics manufacturing, adhering to industry standards is vital for ensuring quality and compatibility across different systems. Various organizations set forth guidelines that define best practices within Surface Mount Technology (SMT). These standards help manufacturers maintain consistency while navigating challenges like component miniaturization or thermal management.
One critical standard related to what is a SMT line includes IPC-A-610, which outlines acceptability criteria for electronic assemblies using surface mount technology. Compliance with such standards ensures that products meet customer expectations while minimizing defects during production runs—a key aspect when considering what is the SMT production line process.
Additionally, industry practices emphasize continuous improvement through techniques like Lean Manufacturing or Six Sigma methodologies—essentially refining processes over time to enhance efficiency in both SMT lines and traditional DIP lines alike. Understanding these standards not only informs best practices but also equips manufacturers with tools necessary for success in an ever-evolving market landscape.
What is the Difference Between SMD and SMT?
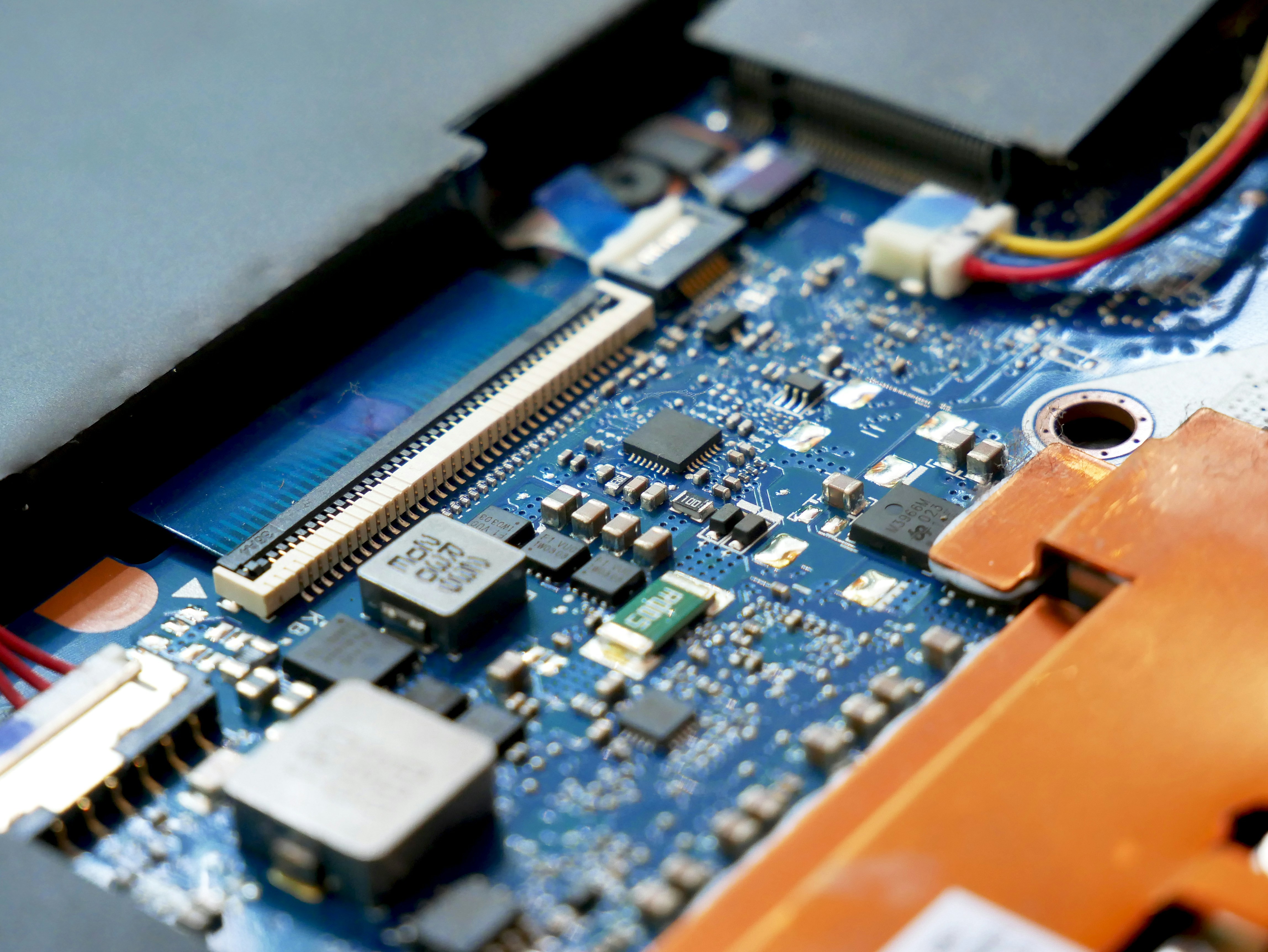
In the world of electronics manufacturing, understanding the distinction between SMD (Surface Mount Devices) and SMT (Surface Mount Technology) is crucial. While they are often mentioned together, they refer to different aspects of the production process. SMD components are specific parts designed for SMT processes, while SMT encompasses the broader technology used for assembling these components onto circuit boards.
Understanding SMD Components
SMD components are miniaturized electronic parts that can be mounted directly onto a printed circuit board (PCB). These components include resistors, capacitors, and integrated circuits that have been specifically designed to occupy less space than traditional through-hole devices. The compact nature of SMDs allows for higher component density on PCBs, which is essential in today’s electronics where space is often at a premium.
One of the key features of SMDs is their flat profile, allowing them to sit flush against the PCB surface. This design not only optimizes space but also enhances performance by reducing lead inductance and improving signal integrity. Understanding these components is vital when exploring what a SMT line entails since they are integral to the entire SMT production line process.
Comparison of SMD and SMT Techniques
While SMD refers to individual components, SMT represents the entire assembly technique used to mount these devices onto PCBs efficiently. In essence, you can think of SMD as the what and SMT as the how. The techniques involved in an SMT line include solder paste application, placement of SMDs using pick-and-place machines, and reflow soldering—all streamlined processes that contribute to high-speed manufacturing.
When comparing techniques, it’s important to note that traditional methods like DIP (Dual In-line Package) require drilling holes into PCBs for component leads—something not needed with an SMT line. This difference allows for more straightforward designs with fewer manufacturing steps when using surface mount technology compared to DIP methods. Additionally, while both methods can produce reliable products, SMT generally offers better performance in terms of electrical characteristics due to shorter lead lengths.
Applications of SMD and SMT in Electronics
SMDs and their associated technologies find applications across various sectors including consumer electronics, automotive systems, telecommunications, and medical devices. With their small size and lightweight characteristics facilitated by an efficient smt line process, these components enable manufacturers to create more compact devices without sacrificing functionality or performance.
Moreover, industries increasingly rely on surface mount technology due to its ability to support high-frequency applications where signal integrity is paramount. As we continue evolving towards smarter technologies—think IoT devices or wearables—the relevance of both SMDs and SMT becomes even more pronounced in meeting consumer demands for smaller yet powerful electronic solutions.
What is the SMT Production Line Process?
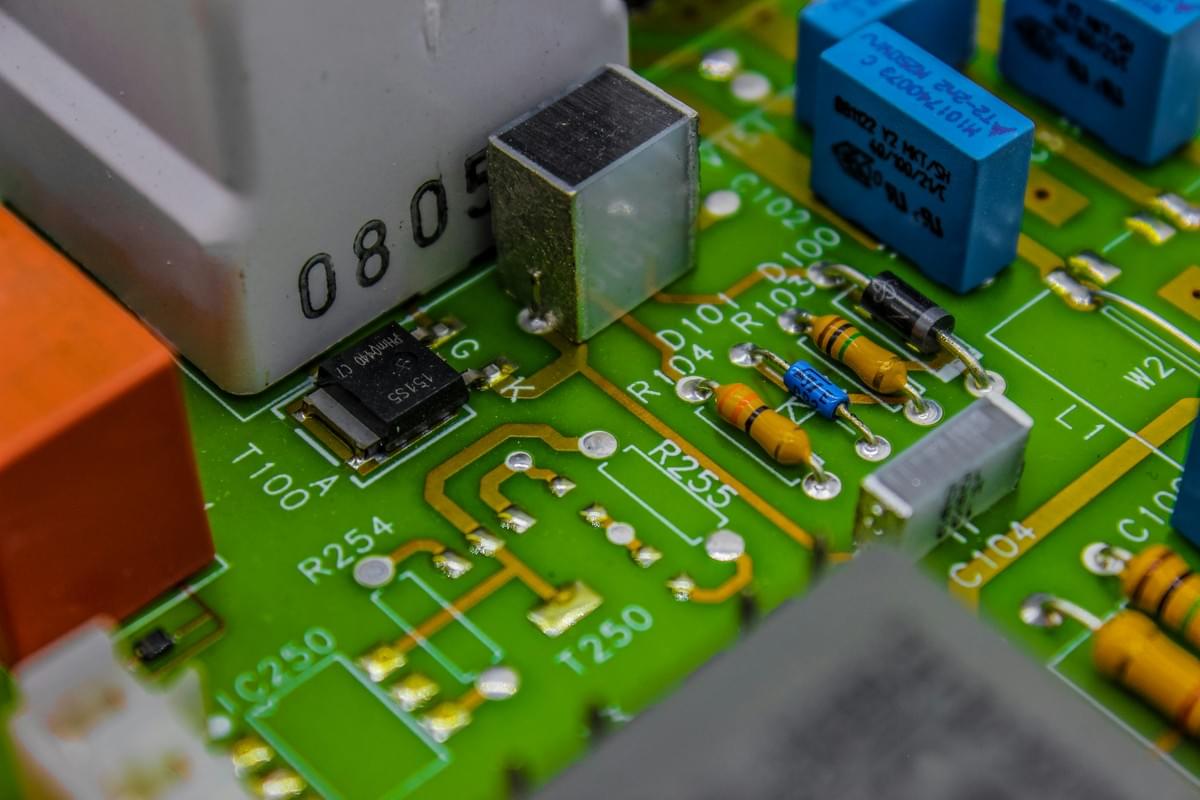
The SMT production line process is a carefully orchestrated series of steps that transform raw materials into fully functional electronic devices. It encompasses everything from the initial design to the final testing, ensuring that each component adheres to high industry standards. Understanding this process is crucial for anyone asking, What is a SMT line? as it highlights the efficiency and precision required in modern electronics manufacturing.
Step-by-Step Overview of SMT Production
The SMT production process begins with PCB (Printed Circuit Board) preparation, where the board is cleaned and coated with solder paste using a stencil printer. Following this, components are placed onto the board through an automated pick-and-place machine, which ensures accurate positioning of SMD (Surface Mount Devices). After placement, the boards undergo reflow soldering to melt the solder paste and secure components in place before moving on to inspection and testing phases.
In essence, each step in the SMT production line is designed to minimize errors while maximizing throughput. For those wondering what does SMT stand for?, it's all about surface mount technology that enables compact designs and efficient assembly processes. This systematic approach not only enhances productivity but also aligns with industry demands for faster turnaround times.
Key Equipment Used in the Process
A variety of specialized equipment plays a pivotal role in ensuring an efficient SMT production line process. The primary machines include stencil printers for applying solder paste, pick-and-place machines for component placement, and reflow ovens for soldering connections securely onto PCBs. Additionally, inspection systems such as AOI (Automated Optical Inspection) ensure quality control by detecting defects early in the process.
Each piece of equipment contributes significantly to answering questions like What is the difference between SMD and SMT? since SMD components are specifically designed for use on these lines due to their size and mounting style. With advancements in technology, newer machines are becoming more automated and capable of handling more complex assemblies while maintaining high levels of accuracy. This evolution highlights why understanding what an SMT production line entails can greatly benefit manufacturers looking to optimize their operations.
Quality Control Measures in SMT
Quality control measures are integral throughout every phase of the SMT production line process to ensure reliability and performance standards are met consistently. These measures include regular inspections at various stages: after solder paste application, post-component placement, and following reflow soldering processes. Implementing rigorous quality checks helps identify any issues early on—saving time and resources down the road.
Moreover, integrating both manual inspection techniques alongside automated systems provides a comprehensive approach to quality assurance within an SMT line environment. For manufacturers considering when to use an SMT vs DIP (Dual In-line Package), understanding how quality control fits into each method can influence their decision-making significantly regarding product design choices. Ultimately, robust quality control practices enhance overall product reliability while fostering consumer confidence in electronic devices produced via surface mount technology.
What are SMT Line and DIP Line?
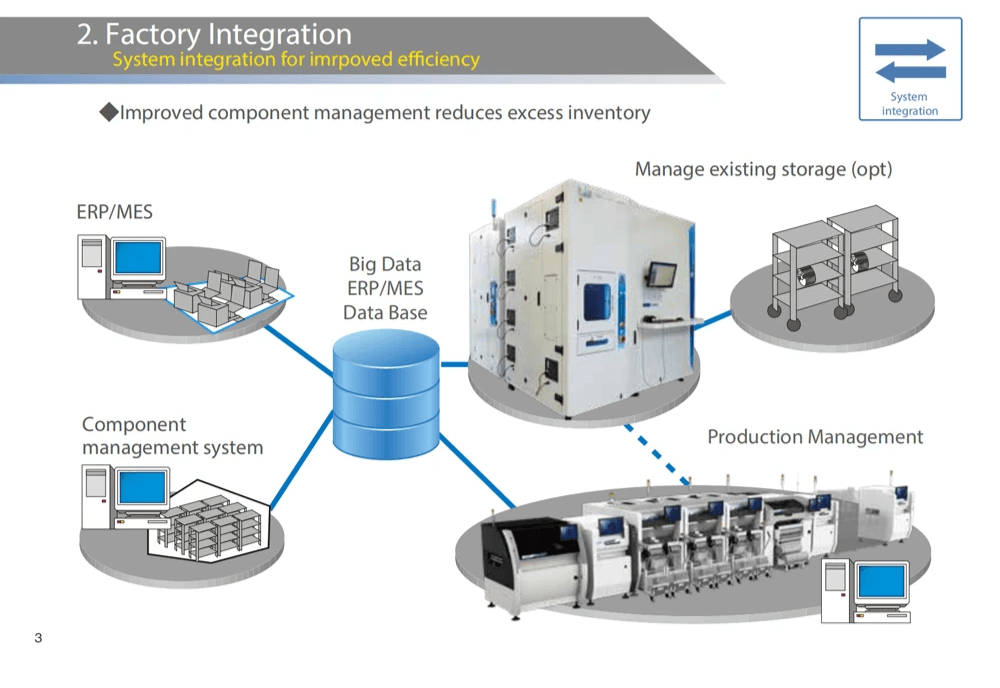
In the world of electronics manufacturing, the terms SMT line and DIP line often come up in discussions about assembly processes. Both lines serve distinct purposes and utilize different technologies to mount components onto printed circuit boards (PCBs). Understanding these differences is crucial for manufacturers looking to optimize their production capabilities.
Differences Between SMT Line and DIP Line
The primary difference between an SMT line and a DIP line lies in how components are mounted onto PCBs. An SMT line uses Surface Mount Technology, where electronic components are placed directly onto the surface of the PCB. In contrast, a DIP (Dual In-line Package) line employs through-hole technology, where leads from components pass through holes drilled in the board before being soldered on the opposite side.
Additionally, SMT lines generally allow for higher component density and smaller PCB sizes compared to DIP lines. This is because SMD (Surface Mount Device) components are typically smaller than their through-hole counterparts, which can take up more space on a board. Furthermore, while SMT production processes tend to be faster due to automated equipment, DIP lines may require more manual labor for assembly.
When to Use SMT vs. DIP
Choosing between an SMT line and a DIP line depends largely on the specific requirements of your project. If you need high-density assemblies with compact designs or if you’re working with modern electronics that require miniaturization, an SMT line is likely your best bet. However, if your project involves larger components that benefit from robust mechanical connections—like power supplies or connectors—then a DIP line might be more appropriate.
Another factor to consider is production volume; high-volume runs generally favor SMT due to its speed and efficiency. On the other hand, low-volume or prototype runs might still find value in using a DIP line for its simpler setup process and ease of handling larger parts. Ultimately, understanding what does SMT stand for helps clarify why it excels in certain applications over traditional methods like those found in a DIP line.
Benefits of Integrating Both Lines
Integrating both an SMT line and a DIP line can offer significant advantages for manufacturers looking to maximize flexibility and efficiency in their production processes. By leveraging both technologies, companies can produce complex assemblies that incorporate both small SMD components as well as larger through-hole devices without compromising on quality or performance.
Moreover, having access to both types of lines enables manufacturers to cater to diverse client needs while optimizing inventory management across various projects. This dual approach not only enhances product versatility but also allows businesses to adapt quickly as market demands shift—a key advantage in today’s fast-paced electronics landscape.
By understanding what are SMT Line and DIP Line differences along with when it's best to use each method, manufacturers can make informed decisions that enhance productivity while maintaining high standards of quality control throughout the entire SMT production line process.
Conclusion
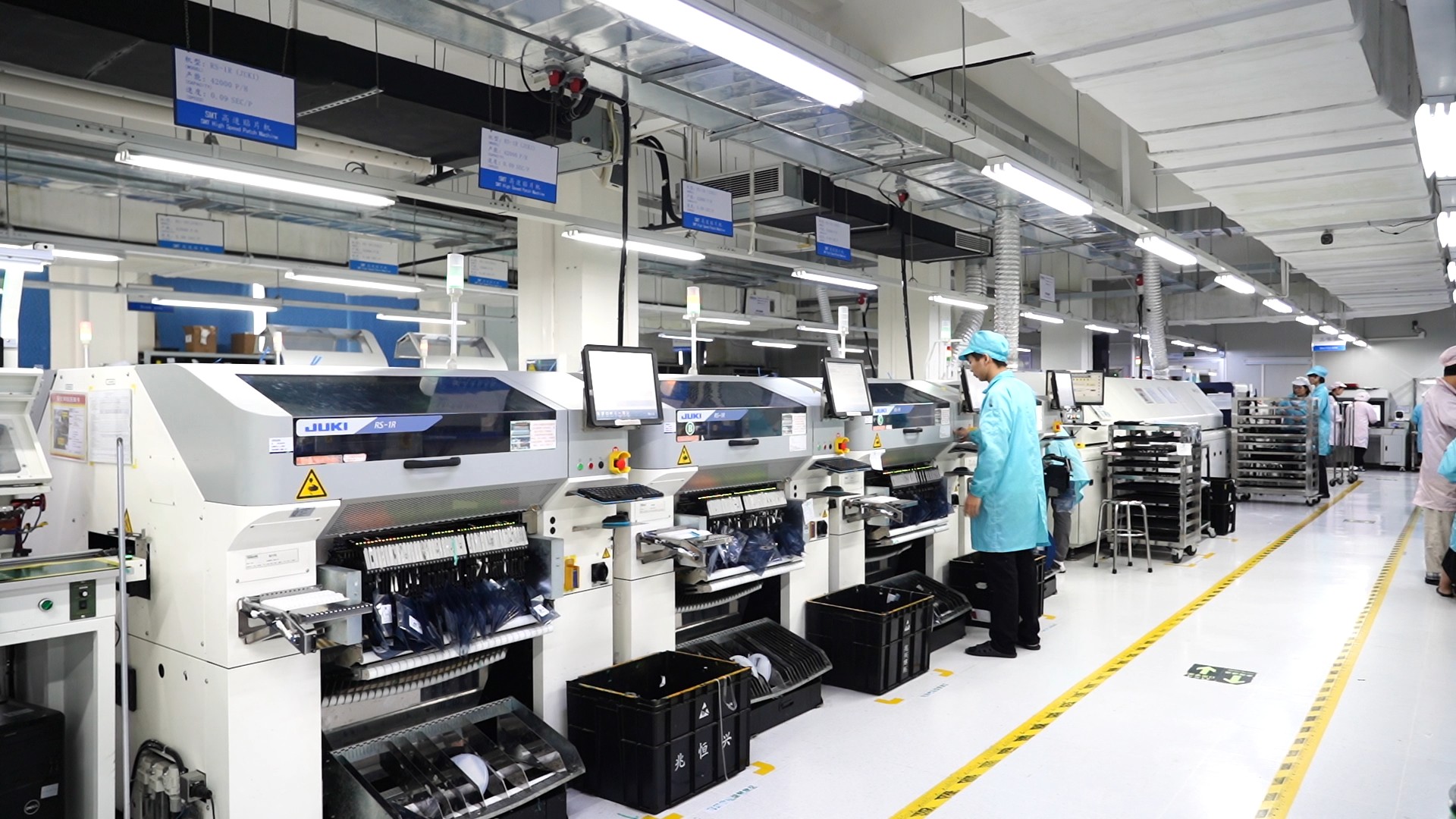
In the rapidly evolving world of electronics, the significance of the SMT line cannot be overstated. As we look to the future, it's clear that Surface Mount Technology (SMT) will continue to play a pivotal role in shaping how electronic devices are manufactured. With advancements in technology and increasing demands for efficiency, understanding what a SMT line entails is essential for manufacturers aiming to stay competitive.
The Future of SMT in Electronics
The future of SMT in electronics is bright, with innovations driving improvements in speed and precision. As we delve deeper into what does SMT stand for, it becomes evident that its core principles will adapt to meet emerging challenges such as miniaturization and sustainability. Manufacturers are increasingly integrating smart technologies into their SMT production line processes, ensuring they remain agile and responsive to market needs.
Choosing the Right SMT Solution with Bensun Technology
When considering what is the difference between SMD and SMT, it's crucial to recognize that selecting the right solution can significantly impact efficiency and cost-effectiveness. Bensun Technology stands out by offering tailored solutions designed for specific production requirements, ensuring that clients can maximize their operations on both SMT lines and DIP lines. By leveraging their expertise, businesses can confidently navigate through these options and choose an approach that best suits their manufacturing goals.
Final Thoughts on SMT Efficiency and Innovation
In conclusion, understanding what are SMT Line and DIP Line provides valuable insights into optimizing production processes within electronics manufacturing. The integration of innovative technologies within these lines enhances overall productivity while reducing lead times—a win-win situation for manufacturers striving for excellence. Embracing this evolution not only fosters efficiency but also paves the way for groundbreaking advancements in electronic device development.