Introduction
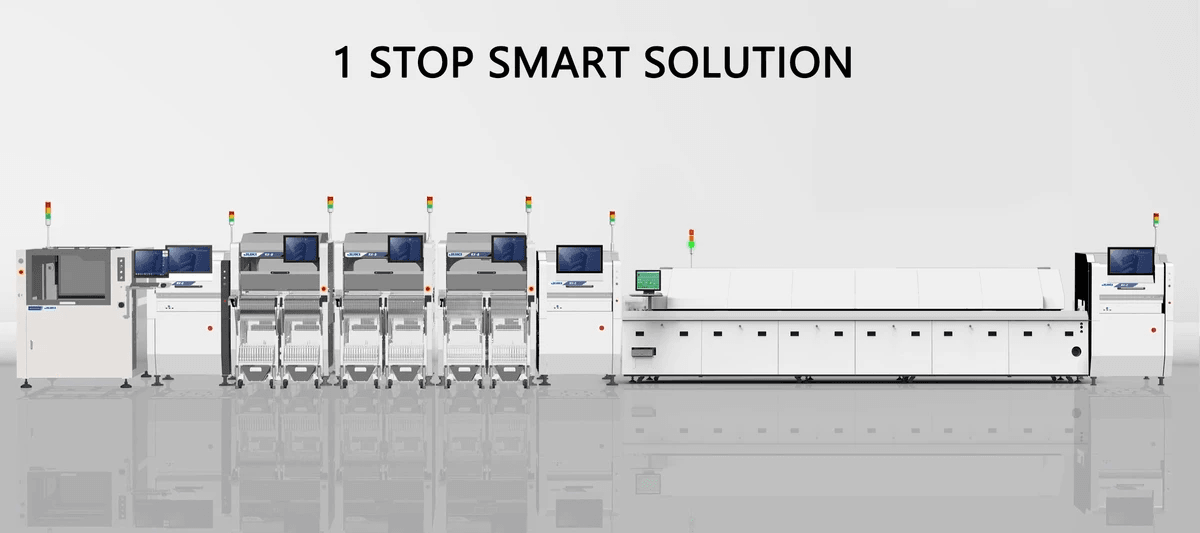
In today's fast-paced electronics manufacturing environment, understanding SMT technology is crucial for staying competitive. Surface Mount Technology (SMT) has revolutionized the way electronic components are assembled, allowing for smaller, more efficient designs. At the heart of this transformation lies the SMT mounter, a machine that has become indispensable in modern production lines.
Understanding SMT Technology
Surface Mount Technology (SMT) involves mounting electronic components directly onto the surface of printed circuit boards (PCBs), eliminating the need for through-holes and enabling a more compact design. This method not only enhances performance but also streamlines production processes, making it an essential aspect of contemporary electronics manufacturing. As we delve deeper into SMT technology, it's important to appreciate how these advancements have paved the way for innovations in machine pick and place systems.
Importance of Pick and Place Machines
Pick and place machines play a pivotal role in SMT production lines by automating the placement of components on PCBs with remarkable precision and speed. These machines significantly reduce human error while increasing throughput, making them vital for high-volume production environments. The efficiency gained from using a pick & place machine directly impacts product quality and overall operational costs.
Overview of SMT Mounter Production Line
An SMT mounter production line is typically structured to maximize efficiency through streamlined workflows and integrated technologies. Each component of the line works in harmony—from solder paste application to component placement—ensuring that every step is optimized for speed and accuracy. Understanding how these elements come together can help manufacturers leverage surface mount SMT processes to achieve better outcomes.
What is an SMT Mounter Machine?
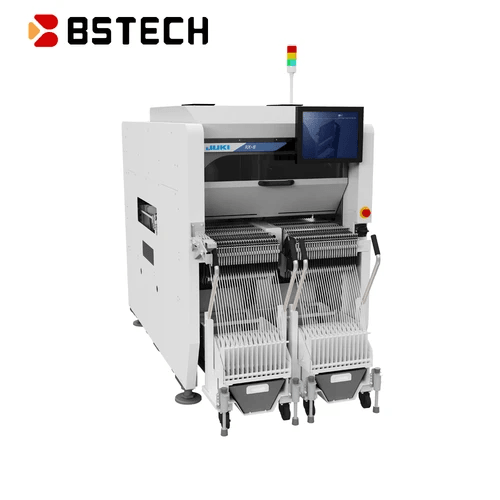
An SMT mounter machine, often referred to as a pick and place machine, is a crucial piece of equipment in the realm of surface mount technology (SMT). Its primary function is to accurately place electronic components onto printed circuit boards (PCBs) with precision and speed. The evolution of these machines has significantly streamlined the manufacturing process, enhancing efficiency and productivity in electronics assembly.
Definition and Functionality
An SMT mounter machine automates the placement of surface-mounted devices (SMDs) onto PCBs, which are essential for modern electronic devices. These machines utilize advanced vision systems to identify component types and positions on the board, ensuring precise placement within tight tolerances. By minimizing human error and maximizing speed, pick & place machines are integral to achieving high-quality production in SMT technology.
Key Components of SMT Mounters
The key components of an SMT mounter include feeders for component supply, a vision system for alignment verification, and a robotic arm for accurate placement. Feeders can be configured for various component types, allowing flexibility in production runs; they ensure that components are delivered efficiently to the mounting area. The robotic arm employs sophisticated algorithms to execute rapid movements while maintaining accuracy—essentially making it the heart of any reliable pick and place machine.
Role in Surface Mount Technology
The role of SMT mounters in surface mount technology cannot be overstated; they are pivotal in transitioning from traditional through-hole assembly methods to more efficient surface mount processes. By enabling higher component density on PCBs, these machines facilitate smaller device designs without compromising performance or reliability. Moreover, advancements in smt technology continuously enhance their capabilities, leading to innovations that further drive the electronics manufacturing industry forward.
How SMT Production Lines are Structured
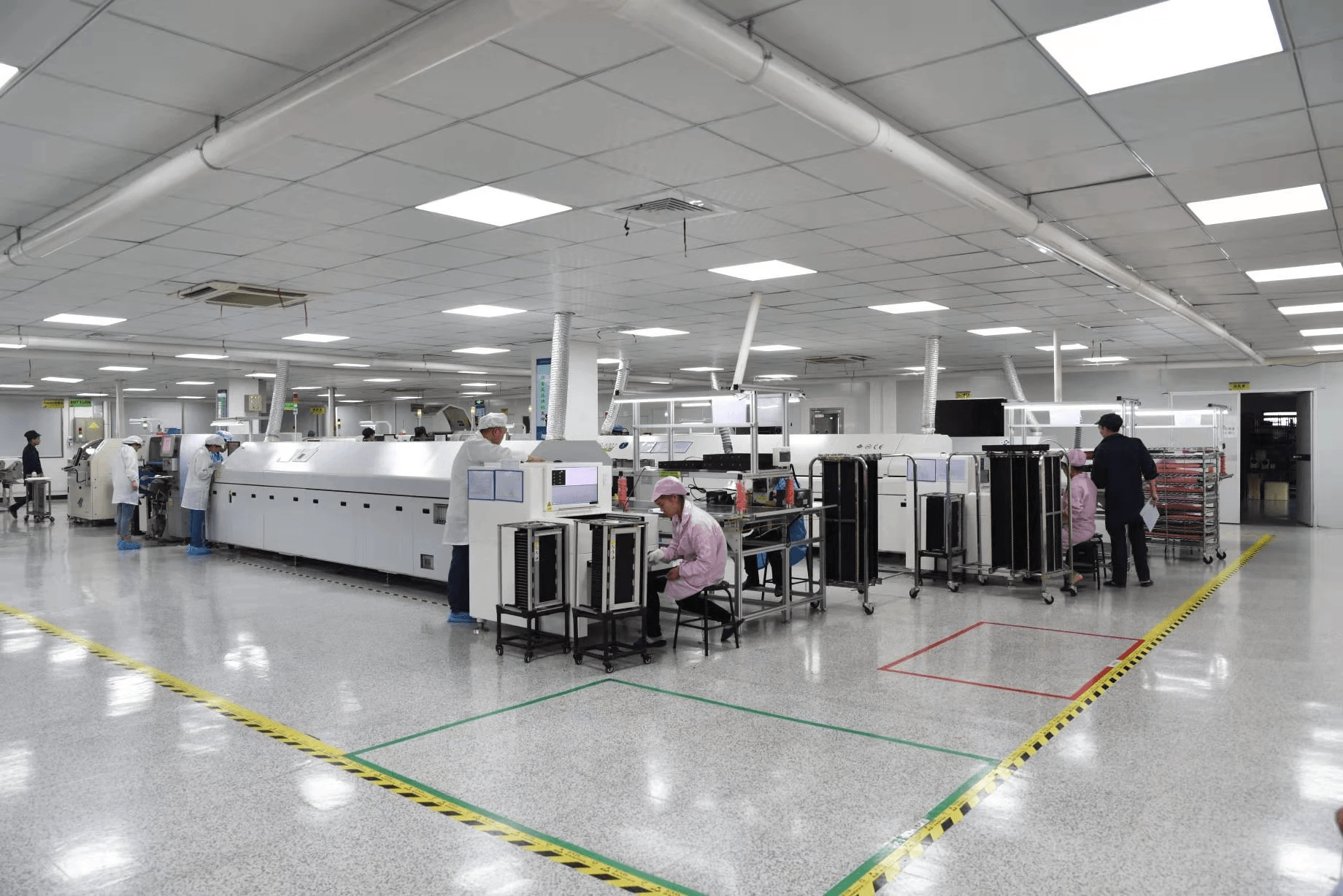
In the world of surface mount technology (SMT), the structure of production lines is crucial for achieving efficiency and quality in manufacturing. A well-organized SMT production line maximizes the capabilities of pick and place machines while ensuring smooth workflow from component placement to final assembly. Understanding how these lines are laid out and integrated can significantly impact overall productivity.
Layout of a Typical SMT Production Line
A typical SMT production line features a series of workstations that facilitate various stages of assembly, starting with printed circuit board (PCB) preparation and ending with inspection and testing. The layout generally follows a linear flow, which allows for easy movement between stations, minimizing bottlenecks that can hinder production efficiency. Each workstation is equipped with specialized equipment such as solder paste printers, reflow ovens, and, most importantly, SMT mounters or pick & place machines that handle component placement with precision.
The arrangement often includes dedicated areas for material storage, assembly lines for manual interventions, and zones for quality control checks. This structured approach not only streamlines operations but also enhances collaboration among team members who work at different stages in the process. Ultimately, an effective layout supports the seamless integration of machine pick and place systems into the overall workflow.
Integration of Machine Pick and Place Systems
Integrating machine pick and place systems into an SMT production line is essential for maximizing throughput while maintaining high standards of accuracy in component placement. These advanced machines utilize sophisticated vision systems to identify components accurately before picking them from feeders or trays—ensuring that every piece lands exactly where it should on the PCB. This level of integration allows manufacturers to automate repetitive tasks while reducing human error.
Moreover, modern pick & place machines can be programmed to handle a variety of components ranging from small resistors to larger capacitors without needing extensive reconfiguration between runs. This flexibility makes them invaluable in environments where product variations are common or where rapid changes in demand require quick adjustments on the fly. As such, integrating these systems not only enhances operational efficiency but also enables manufacturers to respond swiftly to market changes.
Workflow and Efficiency Enhancements
Enhancing workflow within an SMT production line involves careful coordination among all components—from material handling to final inspection processes—ensuring each step contributes effectively toward overall output goals. By leveraging automation through advanced pick and place machines alongside other technologies such as conveyor systems and automated optical inspection (AOI), companies can significantly reduce cycle times while improving accuracy rates in assembly processes.
Additionally, continuous monitoring tools help track performance metrics across various stages in real-time; this data-driven approach enables quick identification of any inefficiencies or potential issues before they escalate into larger problems affecting production quality or timelines. Furthermore, implementing lean manufacturing principles within this structured environment fosters a culture focused on waste reduction—allowing teams to optimize their use of resources while enhancing productivity levels across all operations.
The Pick and Place Process Explained
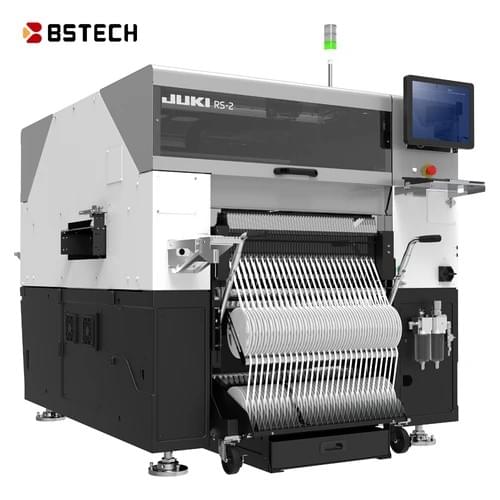
Understanding the pick and place process is crucial for anyone involved in SMT technology. This process, executed by a machine pick and place system, involves several meticulous steps that ensure components are accurately placed on printed circuit boards (PCBs). Let's dive into the details of how this vital operation unfolds.
Steps Involved in Component Placement
The pick and place machine begins its work by identifying the components required for assembly from a feeder system. Once selected, the machine uses suction cups or grippers to pick up these components with precision. Following that, it moves to the designated location on the PCB where it carefully places each component, ensuring alignment with solder pads for effective soldering during reflow.
After placement, the SMT mounter often performs a visual inspection or utilizes sensors to confirm that each component is correctly positioned before moving onto the next one. This step is critical because even a slight misalignment can lead to significant issues during soldering or circuit functionality. Thus, effective communication between various machines in an SMT production line enhances overall efficiency and accuracy.
Calibration and Precision in SMT Mounters
Calibration is paramount when it comes to maintaining precision in smt mounters. Regular calibration ensures that every movement of the machine pick and place system is accurate within microns—essential for high-density surface mount technology applications where space is at a premium. By adjusting parameters such as speed, force, and placement accuracy, manufacturers can optimize their SMT processes for different types of components.
Moreover, advanced vision systems integrated into modern pick & place machines allow for real-time adjustments based on feedback received during operation. This capability not only enhances precision but also minimizes errors caused by component variations or misalignments during production runs. Ultimately, well-calibrated smt mounters contribute significantly to improved yield rates and reduced waste.
Benefits of Automated Placement
Automated placement through a pick & place machine brings numerous benefits to surface mount technology operations. First and foremost, it drastically increases production speed compared to manual assembly methods; machines can operate continuously with minimal downtime while maintaining high levels of accuracy across large batches of PCBs.
Additionally, automation reduces labor costs as fewer operators are needed per production line while enhancing safety by minimizing human error risks associated with manual handling of delicate electronic components. With consistent performance over time, automated systems also enable manufacturers to achieve better quality control standards within their smt surface mount technology processes.
In conclusion, understanding the intricacies of the pick and place process reveals how vital these machines are in modern electronics manufacturing—ensuring efficiency without compromising quality.
Major Players in SMT Technology
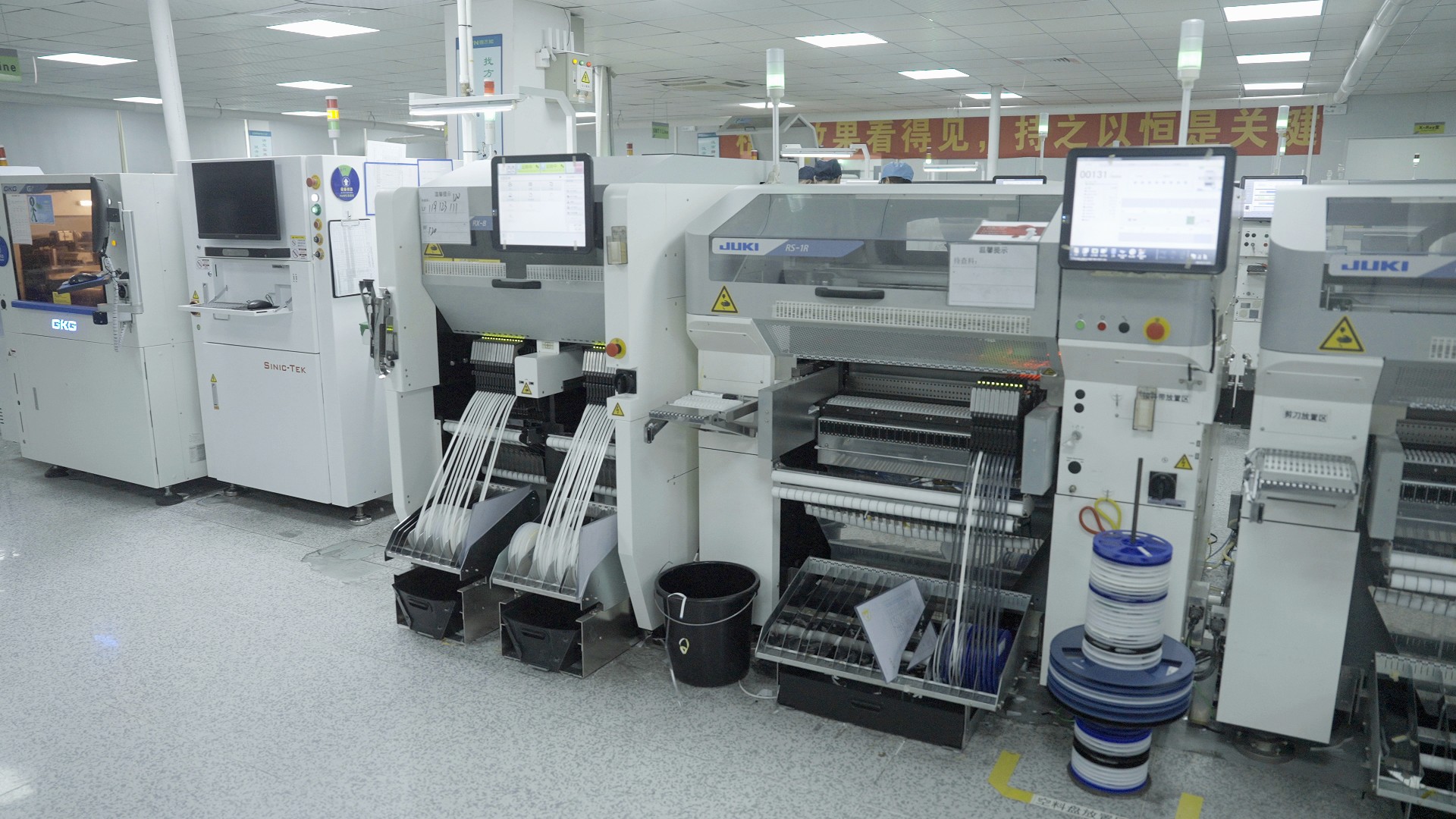
In the rapidly evolving landscape of surface mount technology (SMT), several key players have emerged, each contributing to the advancement of SMT mounters and pick and place machines. These companies not only manufacture equipment but also push the boundaries of innovation, enhancing efficiency and precision in SMT production lines. Among these players, Bensun Technology stands out for its notable contributions, while industry leaders continue to shape the market with their cutting-edge solutions.
Bensun Technology's Contributions
Bensun Technology has made significant strides in the field of SMT technology, particularly with its range of high-performance pick and place machines. Their commitment to quality and innovation has led to the development of advanced smt mounters that enhance production efficiency while maintaining high precision in component placement. By integrating smart technologies into their equipment, Bensun is setting new standards for reliability and performance in surface mount SMT processes.
Moreover, Bensun's focus on customer needs ensures that their smt mounter solutions cater to a diverse range of applications across various industries. This adaptability makes them a preferred choice among manufacturers looking for reliable machine pick and place systems that can handle different components with ease. Their continued investment in research and development underscores their role as a major player driving advancements within SMT technology.
Industry Leaders in SMT Equipment
The landscape of SMT equipment is dominated by several industry giants known for their pioneering technologies and robust product offerings. Companies like Panasonic, Yamaha, and Juki have established themselves as leaders by continually innovating their pick & place machines to meet the growing demands of modern manufacturing environments. These companies are recognized for producing highly efficient smt mounters that integrate seamlessly into sophisticated production lines.
Panasonic’s commitment to precision engineering has resulted in some of the most advanced pick and place machines on the market today, capable of handling complex assemblies with remarkable accuracy. Similarly, Yamaha's innovative approach focuses on automation features that enhance workflow efficiency within surface mount technology environments. As these industry leaders continue to innovate, they set benchmarks that other manufacturers aspire to achieve.
Innovations in Surface Mount Technology
Innovation is at the heart of surface mount technology (SMT), driving improvements across all facets from design to production processes. Recent advancements include AI-driven algorithms integrated into smt mounters that optimize component placement based on real-time data analysis—enhancing accuracy while reducing cycle times significantly. Additionally, developments such as modular machine designs allow manufacturers greater flexibility when scaling operations or adapting production lines for different products.
Furthermore, innovations like 3D inspection systems are becoming increasingly common within automated assembly lines; they ensure quality control by detecting defects before components are soldered onto PCBs (printed circuit boards). The rise of IoT (Internet of Things) capabilities also enables better monitoring and predictive maintenance for pick & place machines—minimizing downtime while maximizing output efficiency in surface mount processes overall. As these innovations unfold, they promise a bright future for SMT technology.
Challenges in SMT Mounter Operations
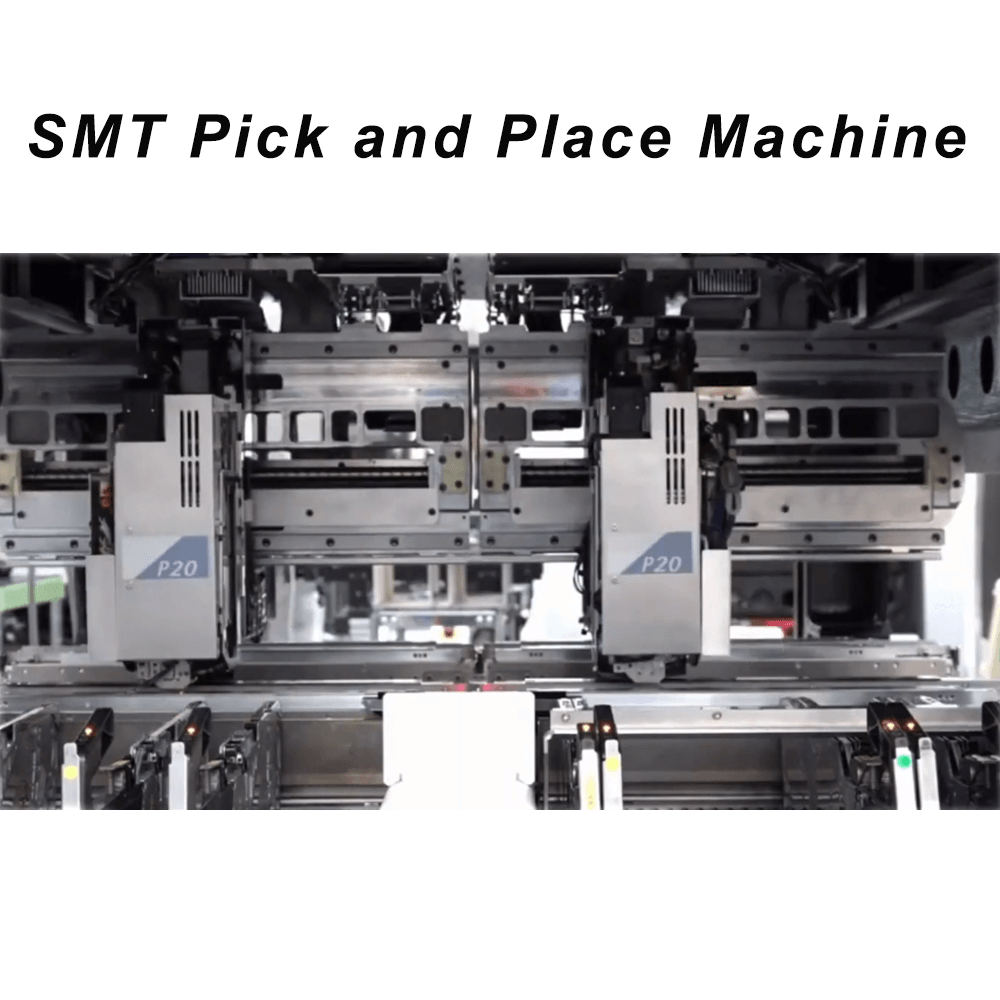
While SMT technology has revolutionized the electronics manufacturing industry, operating SMT mounters and pick and place machines is not without its challenges. From equipment malfunctions to the complexities of managing production workflows, these issues can significantly impact efficiency and output quality. Understanding these challenges is crucial for manufacturers aiming to optimize their surface mount technology processes.
Common Issues Faced in Production Lines
One of the most prevalent issues in SMT mounter operations is misalignment during component placement, which can lead to costly defects and rework. This misalignment often stems from inadequate calibration of the pick & place machine or wear and tear on critical components over time. Additionally, component shortages or inconsistencies in part specifications can disrupt production schedules, causing delays that ripple through the entire manufacturing process.
Another common challenge involves maintaining optimal speed without sacrificing accuracy. While modern surface mount technology allows for rapid assembly, faster speeds can sometimes compromise precision if not managed correctly. Manufacturers must find a delicate balance between throughput and quality control to ensure that their SMT production lines remain competitive while delivering high-quality products.
Quality Control in SMT Processes
Quality control is paramount in any surface mount technology operation; however, achieving consistent quality with SMT mounters can be challenging due to various factors. One major concern is ensuring that all components are correctly placed and soldered without defects like tombstoning or solder bridging. Implementing rigorous inspection protocols using automated optical inspection (AOI) systems can help identify defects early on but requires additional investment.
Moreover, variations in environmental conditions such as humidity and temperature can affect soldering processes, leading to potential issues with adhesion or component reliability. To maintain high standards of quality control within SMT processes, manufacturers need to establish stringent monitoring systems that account for these variables while also training personnel on best practices for handling materials and equipment.
Strategies for Overcoming Challenges
To tackle the challenges associated with SMT mounter operations effectively, manufacturers should prioritize regular maintenance schedules for their pick & place machines and other equipment involved in surface mount technology processes. By conducting routine inspections and calibrations, companies can minimize downtime caused by unexpected malfunctions while extending the lifespan of their machinery.
Investing in advanced software solutions that facilitate real-time monitoring of production metrics is another strategic approach worth considering. These tools allow manufacturers to track performance data closely, enabling quick identification of bottlenecks or inefficiencies within the workflow—ultimately leading to enhanced productivity levels across the board.
Lastly, fostering a culture of continuous improvement among employees through training programs focused on both technical skills and problem-solving techniques will empower teams to address challenges proactively rather than reactively. By embracing a holistic approach that combines technology enhancements with human expertise, companies can position themselves for long-term success within the ever-evolving landscape of surface mount technology.
Conclusion
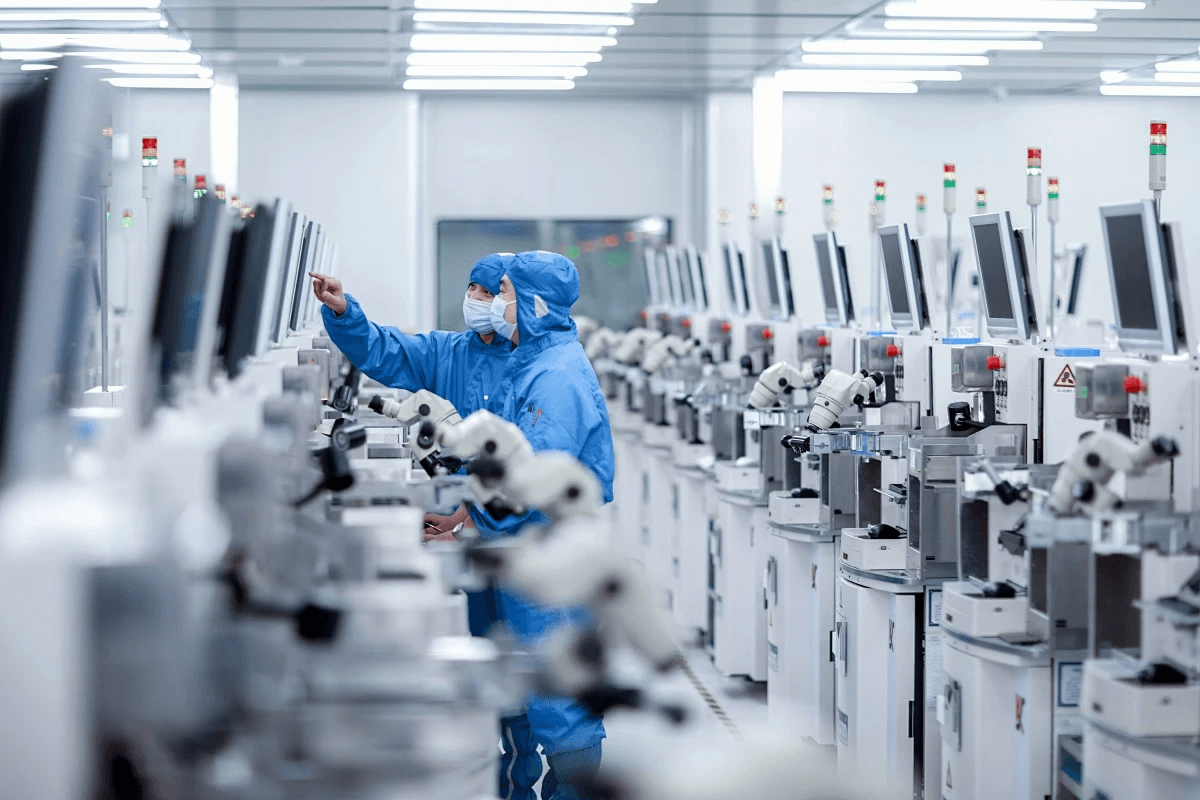
In wrapping up our exploration of SMT technology and the pivotal role of pick and place machines, it's clear that these innovations are more than just tools—they're the backbone of modern electronics manufacturing. As we look to the future, advancements in SMT surface mount technology promise to enhance efficiency, precision, and adaptability in production lines. The evolution of smt mounters will undoubtedly continue to shape how components are assembled, leading to smarter and more efficient manufacturing processes.
The Future of SMT Surface Mount Technology
The future of surface mount technology is bright, characterized by rapid advancements that aim to meet the ever-increasing demands for smaller, faster, and more reliable electronic devices. With ongoing research into materials science and automation, we can expect smt mounters to become even more sophisticated in their capabilities. Innovations such as AI-driven quality control systems and advanced robotics will further streamline the machine pick and place process, enhancing overall productivity while minimizing human error.
Advancements in Pick & Place Machines
Recent advancements in pick & place machines have revolutionized how components are handled during assembly. Enhanced vision systems now allow these machines to identify parts with greater accuracy while adjusting dynamically for different component sizes and shapes. Furthermore, improved software algorithms facilitate real-time data analysis during production runs, ensuring that any issues can be swiftly addressed without significant downtime—a win-win for manufacturers relying on smt technology.
Choosing the Right SMT Equipment Provider
Selecting the right SMT equipment provider is crucial for any business looking to optimize its production line with effective smt mounters or pick and place machines. Companies should consider factors such as reliability, customer support, technological innovation, and scalability when making their choice. A good provider not only offers high-quality equipment but also partners with clients throughout their journey in surface mount technology—ensuring they stay ahead in a competitive landscape.