Introduction
In the fast-paced world of electronics manufacturing, efficiency and precision are paramount. Enter the multifunctional full automatic PCB chip mounter, a game-changing device that automates the assembly process of printed circuit boards (PCBs). This sophisticated machine not only streamlines production but also enhances the quality of electronic devices by ensuring accurate placement of components.
What is a Multifunctional Full Automatic PCB Chip Mounter
A multifunctional full automatic PCB chip mounter is an advanced piece of equipment designed to automate the placement of electronic components onto PCBs. These machines utilize cutting-edge pick and place technology to ensure that each component is accurately positioned with minimal human intervention. The result? A more efficient assembly line where speed meets precision, making it an essential tool in modern electronics manufacturing.
Benefits of Using an Automatic Chip Mounter
The benefits of using an automatic chip mounter are manifold, starting with increased production speed. Unlike traditional soldering machines that rely heavily on manual labor, SMT machines can operate continuously, reducing assembly time significantly. Additionally, these machines minimize human error, leading to fewer defects and higher quality products—an essential factor in today’s competitive market.
Key Features of Modern SMT Machines
Modern SMT machines come equipped with a host of features designed to enhance their functionality and user experience. High-speed operation is complemented by advanced vision systems that ensure precise component placement every time. Furthermore, many machine SMT options now offer flexibility for various component sizes and types, making them adaptable for different projects while maintaining optimal performance levels.
Understanding Automatic Chip Mounters
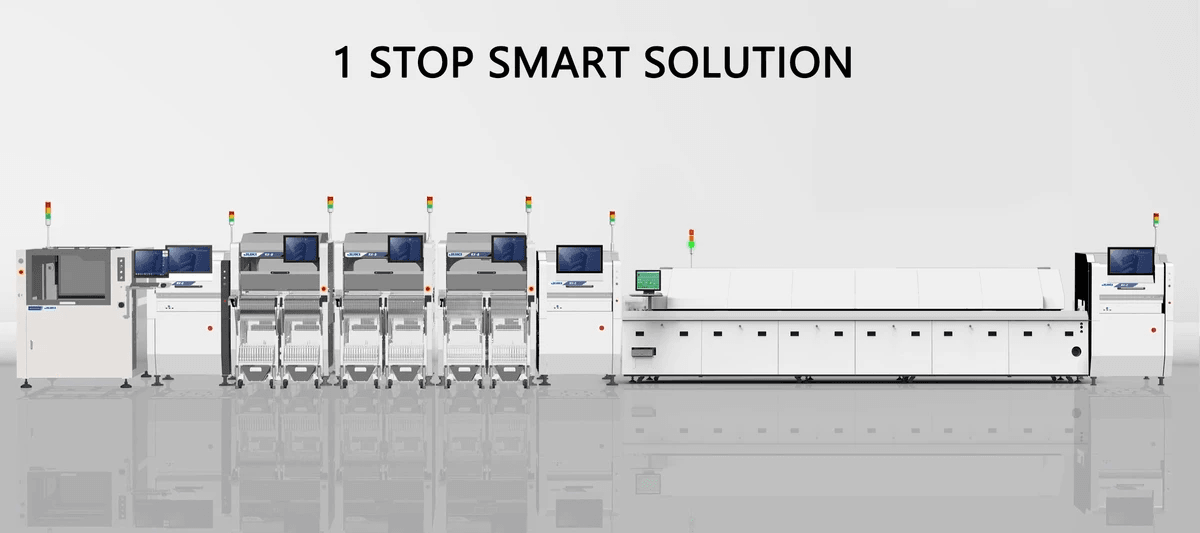
Automatic chip mounters are the unsung heroes of modern electronics manufacturing, streamlining the process of placing components on printed circuit boards (PCBs). These machines utilize advanced technology to ensure precision and speed, significantly enhancing productivity in PCB assembly. By automating this critical step, manufacturers can achieve higher quality and consistency compared to traditional methods.
How Automatic Chip Mounters Work
At the heart of an automatic chip mounter's operation is a sophisticated system that includes a pick and place machine mechanism. This machine pick and place process begins with loading components onto a feeder, where they are then accurately positioned for placement on the PCB. The SMT machine employs vision systems to identify the precise location for each component, ensuring that every piece is placed correctly and efficiently.
Once the components are picked up by suction nozzles, they are swiftly moved to their designated spots on the board. After placement, these components are typically secured using various soldering techniques provided by SMT soldering machines. This seamless integration of multiple processes allows for rapid production cycles while maintaining high standards of quality control.
Types of Automated PCB Assembly Machines
Automated PCB assembly machines come in various forms tailored to specific manufacturing needs. The most common types include standalone automatic chip mounters designed for high-volume production and hybrid systems that combine both surface mount technology (SMT) and through-hole mounting capabilities. Each type offers unique advantages depending on factors like production scale, complexity of designs, and budget constraints.
Another popular type is the selective soldering machine which works alongside pick and place machines to ensure robust connections in mixed technology boards. Additionally, there are inline systems that facilitate continuous production flow by integrating multiple processes into one cohesive unit—ideal for manufacturers aiming for maximum efficiency in their operations. By understanding these different types of automated equipment, businesses can select the right SMT machines that align with their operational goals.
Advantages Over Manual Soldering Machines
The shift from manual soldering machines to automatic chip mounters brings numerous benefits that cannot be overlooked. First off, precision is dramatically improved; automated systems reduce human error significantly while ensuring consistent placement accuracy across large batches of PCBs. This not only enhances product reliability but also minimizes rework costs associated with misplaced components.
Moreover, automatic chip mounters operate at much higher speeds than manual methods can achieve—resulting in shorter lead times and increased throughput for manufacturers. With reduced labor costs due to automation, companies can allocate resources more effectively while still meeting or exceeding customer expectations in terms of delivery timelines and product quality. Ultimately, embracing SMT machines over traditional soldering techniques paves the way toward greater innovation within electronics manufacturing.
The Role of Pick and Place Machines
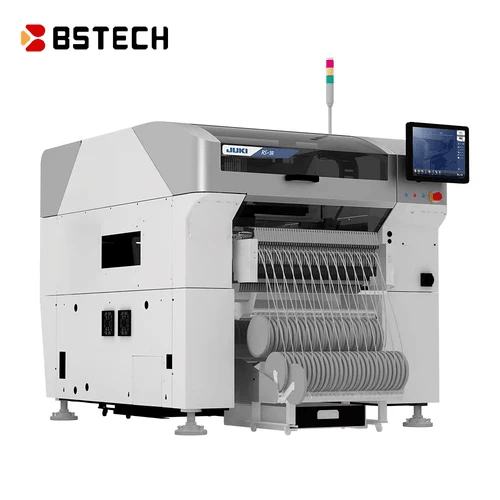
In the world of PCB assembly, the pick and place machine plays a pivotal role in enhancing efficiency and precision. These machines are designed to automate the process of placing components onto printed circuit boards (PCBs), significantly reducing human error and increasing production speed. By utilizing advanced technology, automatic chip mounters can handle a variety of components with remarkable accuracy, making them indispensable in modern electronics manufacturing.
Functionality of Pick and Place Machines
Pick and place machines operate by using a combination of vacuum suction and mechanical arms to accurately position electronic components on PCBs. The machine identifies each component's location through sophisticated vision systems, ensuring that every part is placed exactly where it needs to go. This functionality not only streamlines the assembly process but also allows for high-volume production runs where consistency is key—qualities that manual soldering machines simply cannot match.
The versatility of these machines further enhances their functionality; they can accommodate diverse component types, from tiny surface-mount devices (SMDs) to larger through-hole components. As a result, manufacturers can easily switch between different product lines without extensive reconfiguration—something that manual methods would struggle to achieve efficiently. This adaptability makes pick and place machines essential tools in any SMT machine setup.
Choosing the Right Pick and Place Machine
Selecting the right pick and place machine requires careful consideration of several factors tailored to your specific production needs. First, assess the types of components you will be working with; different machines cater to varying sizes and weights, so ensure compatibility with your PCB designs. Additionally, consider your production volume—high-output operations may benefit from more advanced models equipped with faster placement speeds.
Another crucial aspect is integration capabilities; choose a machine that can seamlessly connect with other SMT equipment such as soldering machines or inspection systems for a cohesive workflow. Features like programmable settings or user-friendly interfaces can also enhance usability while minimizing training time for operators. Ultimately, investing in the right pick and place machine will lead to greater efficiency in your PCB assembly processes.
Integration with Other SMT Equipment
The integration of pick and place machines within an SMT environment is vital for optimizing overall productivity in PCB assembly lines. When paired with soldering machines, these devices create a streamlined workflow where components are placed accurately before being securely soldered onto boards—reducing handling time significantly compared to traditional methods. Furthermore, integrating inspection systems ensures that any defects are caught early in the process, preventing costly errors down the line.
Moreover, modern SMT machines often feature software solutions that allow for real-time monitoring across various stages of production; this means adjustments can be made swiftly if issues arise during operation. Such connectivity not only enhances efficiency but also improves quality control throughout manufacturing processes—a critical factor when dealing with complex electronic products across various industries. Embracing automation through effective integration ultimately leads manufacturers toward greater competitiveness in today's fast-paced market.
Exploring Soldering Technologies

Soldering is a crucial process in PCB assembly, ensuring that components are securely attached to the circuit board. Various types of soldering machines play a significant role in this process, each designed to meet specific manufacturing needs. Understanding these machines can help manufacturers select the right equipment for their production lines.
Types of Soldering Machines in PCB Assembly
In the realm of PCB assembly, several types of soldering machines stand out, each serving unique functions. Wave soldering machines are ideal for through-hole components, providing a consistent solder joint by passing the PCB over a wave of molten solder. On the other hand, reflow ovens cater to surface mount technology (SMT), where an automatic chip mounter applies solder paste before components are placed and heated to create reliable connections.
Another popular option is selective soldering machines, which target specific areas on PCBs without affecting surrounding components. These machines offer precision and flexibility, making them perfect for complex assemblies with mixed technology. Each type of machine plays a vital role in ensuring quality and efficiency in electronic manufacturing processes.
Benefits of SMT Soldering Techniques
SMT soldering techniques have revolutionized the electronics industry by enhancing production speed and reducing costs. By utilizing an automatic chip mounter and associated SMT machines, manufacturers can achieve higher placement accuracy and faster cycle times compared to traditional methods. The compact nature of SMT components also allows for denser circuit designs, maximizing available space on PCBs.
Moreover, SMT soldering techniques contribute significantly to improved reliability due to better thermal management and reduced mechanical stress on components during assembly. This translates into longer lifespans for electronic devices while minimizing defects during production runs. As companies embrace these benefits, they position themselves competitively within an ever-evolving market landscape.
Innovations in Soldering Technology
The world of soldering technology continues to evolve with innovative advancements that enhance efficiency and quality in PCB assembly processes. One notable trend is the integration of smart features into SMT machines; this includes real-time monitoring systems that ensure optimal performance during operation. Such innovations enable manufacturers to quickly identify issues before they escalate into costly problems.
Additionally, advancements in lead-free solder materials have gained traction due to environmental regulations pushing for more sustainable practices within electronics manufacturing. These new materials often provide strong joints while being less harmful than traditional lead-based solders—an essential consideration as sustainability becomes increasingly important across industries. With ongoing research and development efforts focused on improving both performance and environmental impact, future trends promise even greater enhancements in machine pick-and-place capabilities as well as overall assembly efficiency.
Bensun Technology and Their Offerings

Bensun Technology has carved a niche in the realm of SMT solutions, providing cutting-edge equipment that enhances efficiency in PCB assembly. Their offerings include a range of automatic chip mounters and advanced soldering machines designed to meet the diverse needs of modern electronics manufacturing. With a strong emphasis on innovation, Bensun's machines are engineered to optimize production processes while ensuring high-quality outputs.
Overview of Bensun’s SMT Solutions
Bensun’s SMT solutions encompass a variety of state-of-the-art machines, including automatic chip mounters and versatile pick and place machines. These machines are tailored for different scales of production, from small batch runs to large-scale manufacturing operations. By integrating advanced technology with user-friendly interfaces, Bensun ensures that their machine SMT systems can be easily adopted by various manufacturers.
Moreover, Bensun's commitment to quality is evident in their rigorous testing and development processes for each soldering machine they produce. They prioritize reliability and precision, which are crucial for maintaining high standards in PCB assembly. This focus on excellence positions Bensun as a trusted partner for businesses looking to enhance their production capabilities with efficient SMT machines.
JUKI Pick and Place Machines Explained
JUKI pick and place machines represent the pinnacle of automation in PCB assembly, offering unparalleled speed and accuracy in component placement. These automatic chip mounters utilize sophisticated vision systems to ensure precise positioning of components on the printed circuit boards (PCBs). The integration of JUKI technology allows manufacturers to significantly reduce errors compared to traditional methods.
Bensun’s collaboration with JUKI means that customers benefit from top-tier technology combined with local support services tailored for their specific needs. The versatility of these pick and place machines makes them ideal for various applications—from consumer electronics to automotive components—adapting seamlessly to different production environments. With features like quick-change tooling and real-time monitoring systems, JUKI machines enhance productivity while minimizing downtime.
Investing in JUKI pick and place technology is not just about acquiring machinery; it's about embracing a future where efficiency meets innovation in electronic manufacturing processes. As companies continue seeking ways to streamline operations, these SMT machines stand out as essential tools for modern production lines.
Applications in Various Industries
The applications of Bensun’s automatic chip mounter extend beyond just one sector; they span across multiple industries including telecommunications, automotive, medical devices, and consumer electronics. In telecommunications, precision placement by machine pick and place technologies ensures reliable performance under demanding conditions—crucial for maintaining connectivity standards today.
In the automotive sector, where reliability is non-negotiable due to safety regulations, using advanced soldering techniques provided by Bensun helps manufacturers meet strict compliance requirements while enhancing product durability. Similarly, medical device manufacturers benefit from the consistent quality assurance offered by automated soldering machinery during PCB assembly—an essential aspect when dealing with life-saving devices.
Ultimately, adopting Bensun's SMT solutions translates into improved operational efficiency across industries while fostering innovation through automation technologies like machine SMT systems or sophisticated soldering methods. As these sectors evolve towards smarter manufacturing practices, investing in reliable equipment becomes increasingly vital.
Future Trends in PCB Automation
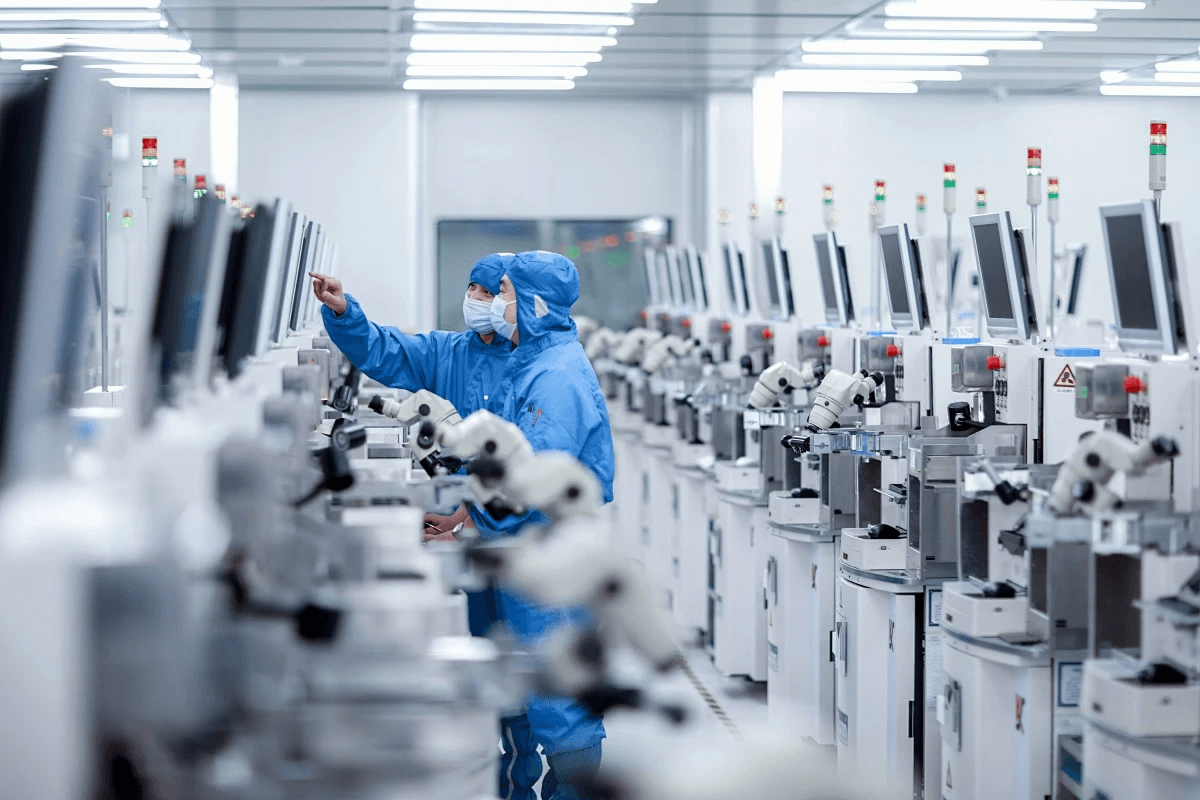
The landscape of PCB automation is rapidly evolving, driven by advancements in technology and the increasing demand for efficiency and precision. As industries embrace smart manufacturing, automatic chip mounters are becoming integral to production lines, ensuring high-quality assembly with minimal human intervention. This shift not only enhances productivity but also paves the way for more innovative soldering machines that can adapt to various manufacturing needs.
The Rise of Smart Manufacturing
Smart manufacturing represents a transformative approach that leverages connectivity and data analytics in production processes. In this environment, machine pick and place systems are optimized to communicate seamlessly with other SMT machines, leading to a more synchronized workflow. By utilizing real-time data, manufacturers can make informed decisions that streamline operations and enhance the performance of their automatic chip mounters.
Additionally, smart factories utilize IoT (Internet of Things) technology to monitor equipment health and predict maintenance needs, reducing downtime significantly. The integration of advanced sensors within pick and place machines allows for continuous feedback on performance metrics, ensuring that every component is placed accurately. This interconnectedness ultimately leads to improved quality control throughout the entire PCB assembly process.
Impact of AI on SMT Machines
Artificial Intelligence (AI) is making waves in the realm of SMT machines by enhancing their capabilities beyond traditional programming. With AI algorithms analyzing vast amounts of data from previous runs, automatic chip mounters can learn optimal placement strategies for different components over time. This evolution results in reduced waste and higher yield rates as the machine becomes adept at adjusting its techniques based on real-time conditions.
Moreover, AI-driven systems can predict potential issues before they arise—think predictive maintenance—but with a twist! They can also optimize soldering processes by identifying the best parameters for each specific job based on historical performance data. As a result, manufacturers using these intelligent SMT soldering solutions are seeing significant improvements in both speed and accuracy.
Sustainability in PCB Production
Sustainability has become a key consideration for manufacturers across all sectors, including PCB production. Modern automatic chip mounters are designed with energy efficiency in mind; they consume less power while maintaining high output levels compared to older models. Furthermore, innovations in soldering technology have led to eco-friendly materials that reduce harmful emissions during production.
Incorporating sustainable practices not only helps companies comply with regulations but also enhances their brand image among environmentally conscious consumers. By choosing advanced pick and place machines that prioritize sustainability without sacrificing performance or quality, businesses position themselves as leaders in responsible manufacturing practices. Ultimately, embracing sustainability within SMT processes will be critical as industries strive toward greener solutions without compromising productivity.
Conclusion
In the fast-paced world of electronics manufacturing, maximizing efficiency is paramount. SMT machines, particularly automatic chip mounters, play a crucial role in streamlining production processes and enhancing overall output quality. By reducing manual labor and minimizing errors, these machines allow companies to focus on innovation rather than repetitive tasks.
Maximizing Efficiency with SMT Machines
The integration of SMT machines into production lines can significantly enhance operational efficiency. Automatic chip mounters utilize advanced technology to ensure precise placement of components, which is essential for high-quality soldering processes. With the ability to handle various component sizes and types, machine pick and place systems adapt seamlessly to different assembly requirements, making them indispensable in modern manufacturing.
Moreover, the speed at which these machines operate cannot be overstated; they can assemble PCBs in a fraction of the time it would take manual methods. This rapid production capability not only boosts throughput but also allows manufacturers to meet tight deadlines without compromising quality. By investing in reliable SMT soldering solutions, businesses can achieve greater productivity while minimizing waste and costs.
Choosing Bensun for Your Equipment Needs
When it comes to selecting equipment for PCB assembly, Bensun Technology stands out as a leading provider of innovative solutions tailored for diverse industries. Their range of automatic chip mounters and pick and place machines are designed with cutting-edge technology that ensures precision and reliability in every operation. Choosing Bensun means opting for quality machinery that enhances your production capabilities while offering excellent support services.
Bensun’s commitment to customer satisfaction is evident through their comprehensive offerings that cater to both small-scale operations and large manufacturers alike. Their expertise in SMT machines guarantees that you receive equipment that meets your specific needs while staying ahead of industry trends. With Bensun's advanced soldering machines integrated into your workflow, you’ll experience an unparalleled boost in efficiency.
Embracing Automation in Electronics Manufacturing
The future of electronics manufacturing lies firmly within automation technologies like SMT machines and their associated components such as pick and place systems and soldering solutions. As industries continue embracing automation, they unlock new levels of productivity while maintaining high standards for quality control. The evolution towards automated processes signifies a shift from traditional methods towards smarter manufacturing paradigms.
Investing in automatic chip mounters not only prepares businesses for current demands but also positions them favorably for future challenges posed by rapid technological advancements. Adopting these innovations fosters sustainability by reducing resource consumption through efficient practices inherent in modern machine smt techniques. Ultimately, embracing automation is not just an option; it's a necessity for staying competitive in today's dynamic market landscape.