Introduction
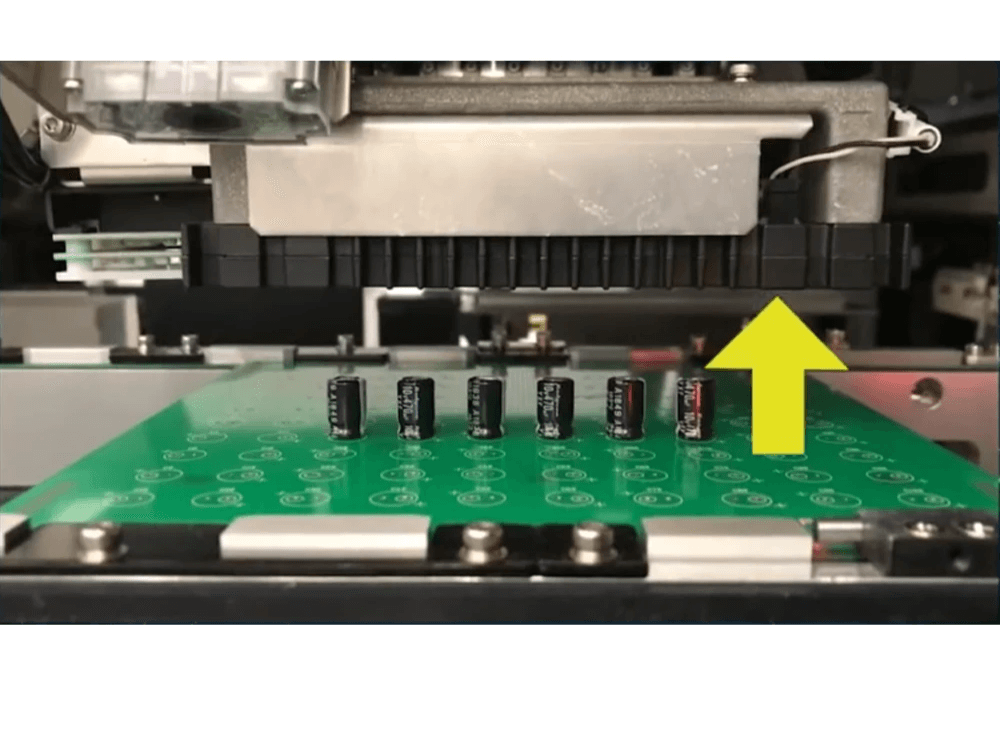
In the ever-evolving world of electronics, understanding surface mount PCB assembly is crucial for both manufacturers and hobbyists alike. This innovative technology has transformed how circuits are designed and assembled, leading to more compact and efficient electronic devices. By delving into the intricacies of what surface mount technology (SMT) entails, we can appreciate its significance in modern electronics.
Understanding Surface Mount PCB Assembly
So, what is surface mount in PCB? Simply put, it refers to a method where electronic components are mounted directly onto the surface of printed circuit boards (PCBs). Unlike traditional methods that require drilling holes for component leads, SMT allows for a more streamlined design process that results in smaller and lighter devices.
Key Benefits of Surface Mount Technology
The advantages of surface mount technology are numerous and compelling. First off, SMT significantly reduces the size and weight of electronic assemblies, making it ideal for today's portable gadgets. Additionally, the efficiency gained through automated SMT processes means faster production times and lower costs—an attractive proposition for manufacturers looking to stay competitive.
Common Applications of SMT in Electronics
Surface mount technology finds its way into a wide array of applications across various industries. From smartphones to medical devices and automotive systems, SMT plays an integral role in ensuring reliability and performance. As we explore further into this topic, we'll uncover how these technologies work together to shape our everyday electronics landscape.
What is Surface Mount in PCB?
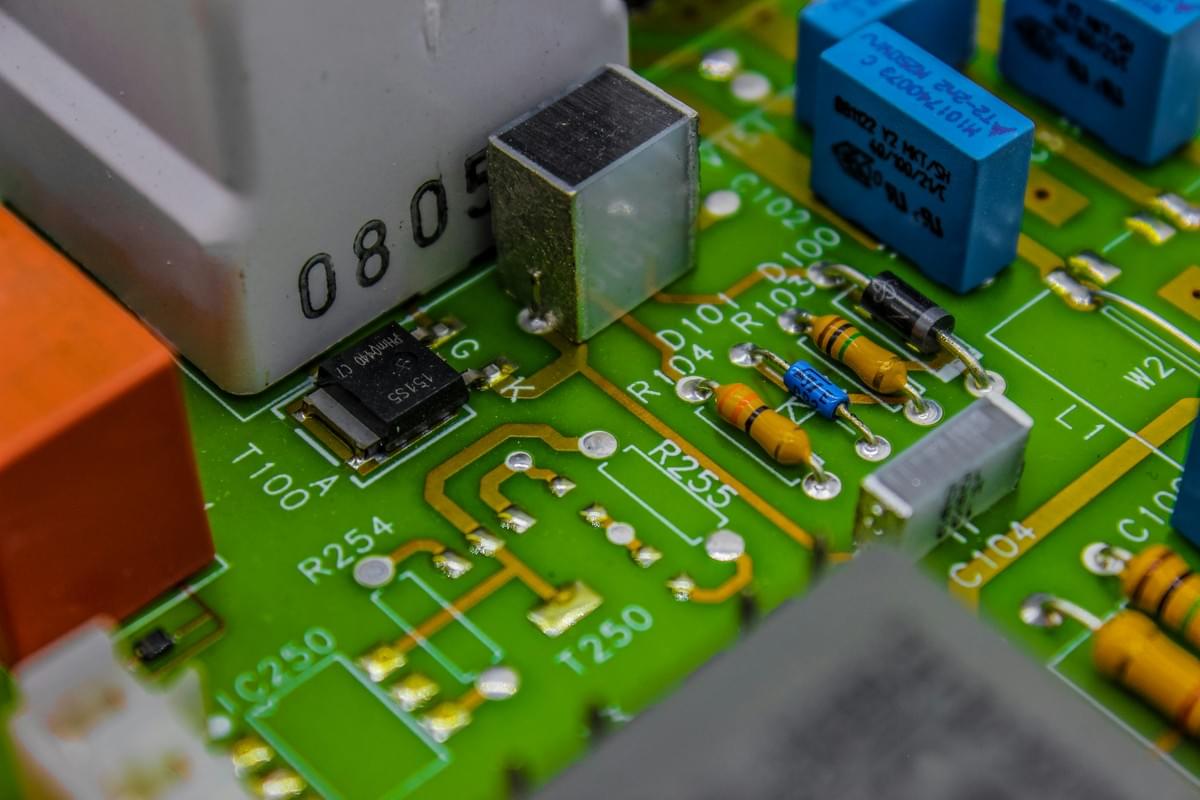
Surface mount technology (SMT) has revolutionized the world of printed circuit boards (PCBs), offering a compact and efficient way to assemble electronic components. But what is surface mount in PCB? Simply put, it involves mounting electronic components directly onto the surface of a PCB rather than through holes, which was the traditional method. This innovative approach not only saves space but also enhances performance, making it a go-to choice for modern electronics.
Definition and Overview of SMT
Surface mount technology (SMT) refers to a method of assembling electronic components onto PCBs without the need for drilling holes. In this process, components are soldered directly onto pads on the surface of the board, allowing for greater density and reduced size compared to traditional methods. Understanding what is surface mount in PCB helps clarify why it's become essential in today’s fast-paced electronics industry.
Components Used in Surface Mount Assembly
In surface mount PCB assembly, various types of components are utilized, including resistors, capacitors, integrated circuits (ICs), and more specialized devices like sensors and connectors. These components are designed specifically for SMT applications, featuring flat leads or no leads at all that allow them to sit flush against the board's surface. The choice of components significantly impacts both performance and design flexibility when considering what is a surface mount assembly.
Advantages Over Traditional Methods
One major advantage of SMT over traditional through-hole mounting (THM) is its ability to accommodate smaller component sizes while maximizing board space—perfect for today's compact devices! Additionally, SMT processes typically lead to faster manufacturing times due to automated equipment like SMT machines that streamline assembly operations. When exploring what is the difference between SMT and THM, efficiency and cost-effectiveness often tip the scales towards SMT as the preferred choice.
What is a Surface Mount Assembly?
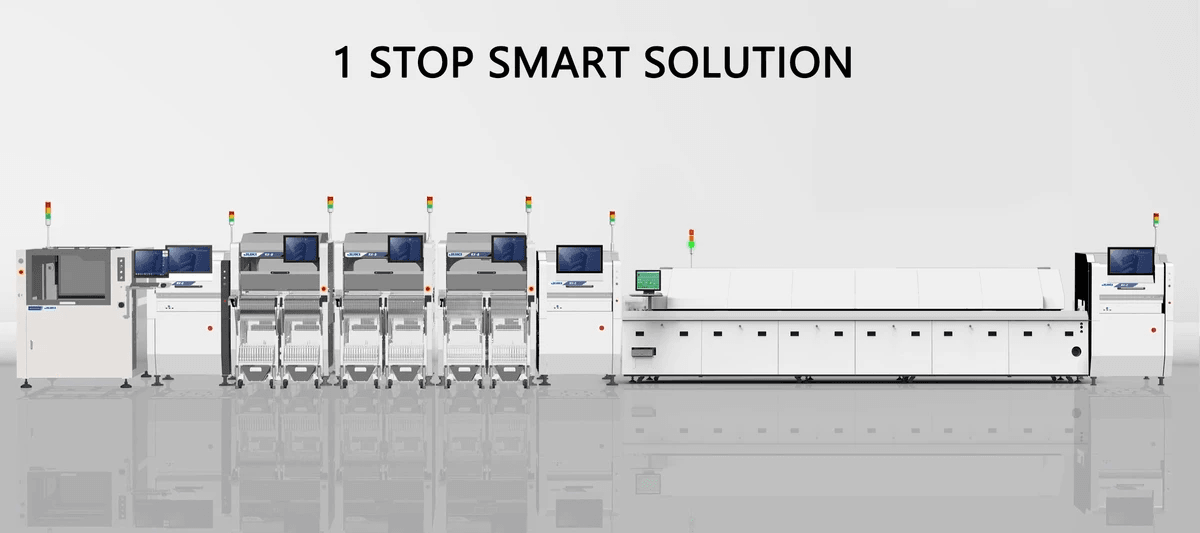
When diving into the world of electronics, one of the key concepts to grasp is what a surface mount assembly actually entails. Essentially, surface mount PCB assembly refers to the technique where electronic components are mounted directly onto the surface of printed circuit boards (PCBs). This method has revolutionized how we design and manufacture electronic devices, enabling greater efficiency and compactness.
The Process of SMT Assembly
The SMT process begins with preparing the PCB by applying solder paste to specific pads where components will be placed. Next, components are accurately positioned on these pads using advanced SMT machines that ensure precision placement—because who wants crooked resistors? Once all components are in place, the board undergoes reflow soldering, which melts the solder paste to create strong electrical connections. This streamlined process not only enhances productivity but also allows for higher component density compared to traditional methods.
Role of SMT Machines in the Process
SMT machines play a pivotal role in making surface mount assembly efficient and reliable. These machines automate much of the work involved in placing components on PCBs, reducing human error and speeding up production times significantly. From pick-and-place machines that position components with astonishing accuracy to reflow ovens that ensure optimal soldering conditions, these tools are indispensable for modern electronics manufacturing.
Quality Control Measures in SMT
Quality control measures in SMT are critical to ensuring that every surface mount PCB assembly meets industry standards and performs as intended. Techniques such as automated optical inspection (AOI) check for defects like misaligned or missing components before they become costly problems down the line. Additionally, functional testing is often conducted post-assembly to verify that each board operates correctly under various conditions—because nobody wants a malfunctioning device ruining their day!
The Difference Between SMT and THM
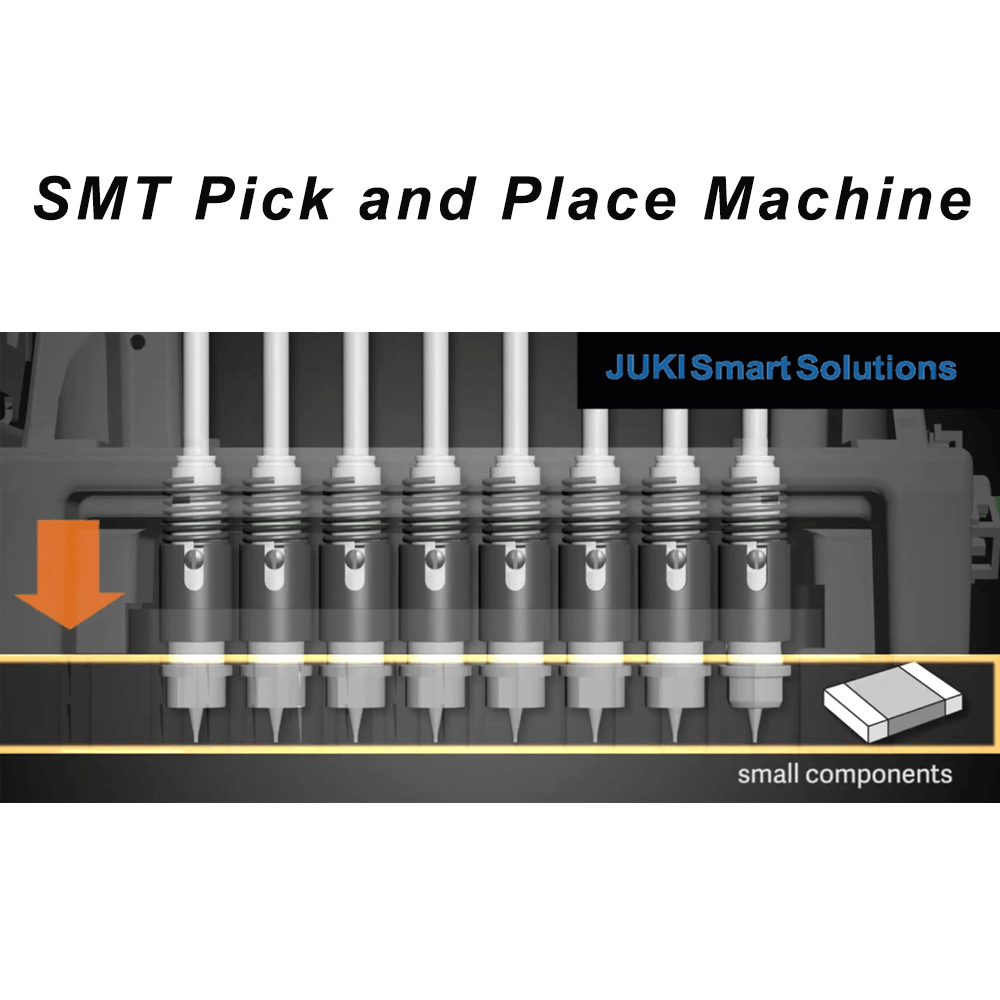
When diving into the world of PCB assembly, understanding the difference between Surface Mount Technology (SMT) and Through-Hole Mount Technology (THM) is crucial. Both methods have their unique advantages and applications, shaping how electronic devices are manufactured. In this section, we will explore what THM is, compare efficiency and cost between SMT and THM, and discuss scenarios where each method shines.
Understanding Through-Hole Mount Technology
Through-Hole Mount Technology (THM) is a traditional method of PCB assembly that involves inserting components through holes drilled in the circuit board. These components are then soldered on the opposite side, forming a robust mechanical bond. While this technique offers excellent durability—especially for larger components—it can be more labor-intensive compared to surface mount PCB assembly.
THM is particularly well-suited for applications requiring high structural integrity or where components might experience stress or vibration. For example, in aerospace or automotive sectors, THM ensures that critical parts stay securely attached during operation. However, as technology advances and miniaturization becomes essential in electronics design, many manufacturers are shifting towards surface mount technology.
Comparing Efficiency and Cost
When evaluating SMT versus THM in terms of efficiency and cost-effectiveness, surface mount PCB assembly tends to have the upper hand in most scenarios. SMT allows for denser packing of components on a circuit board due to its smaller size compared to through-hole counterparts. This not only optimizes space but also reduces production time since SMT machines can automate much of the assembly process.
In contrast, THM generally requires more manual labor due to its nature of inserting components through holes—a process that can slow down production rates significantly. Additionally, while initial setup costs for SMT may be higher because of specialized equipment like SMT machines, the long-term savings from reduced labor costs often make it a more economical choice overall. As manufacturers seek ways to streamline processes while keeping costs down, it's clear why many are leaning towards surface mount technology.
Application Scenarios for Each Method
Both SMT and THM have their place in electronic manufacturing depending on specific application needs. Surface mount technology excels in compact consumer electronics such as smartphones or tablets where space is at a premium—here's where you’ll find densely packed circuits utilizing advanced SMT processes for efficiency. Moreover, industries focusing on high-speed production often prefer SMT due to its automation capabilities.
On the flip side, applications requiring additional strength or robustness may still rely on through-hole mounting techniques; think heavy-duty power supplies or military-grade equipment where reliability is non-negotiable. Each method has its strengths based on project requirements—understanding these differences helps engineers choose wisely between what is surface mount in PCB designs versus traditional methods like THM.
In conclusion, while both technologies serve their purpose well within different contexts of electronic manufacturing today’s trends favor surface mount technology due to its efficiency gains and cost-effectiveness over time—making it an attractive option for modern projects.
The Difference Between SMT and SMD
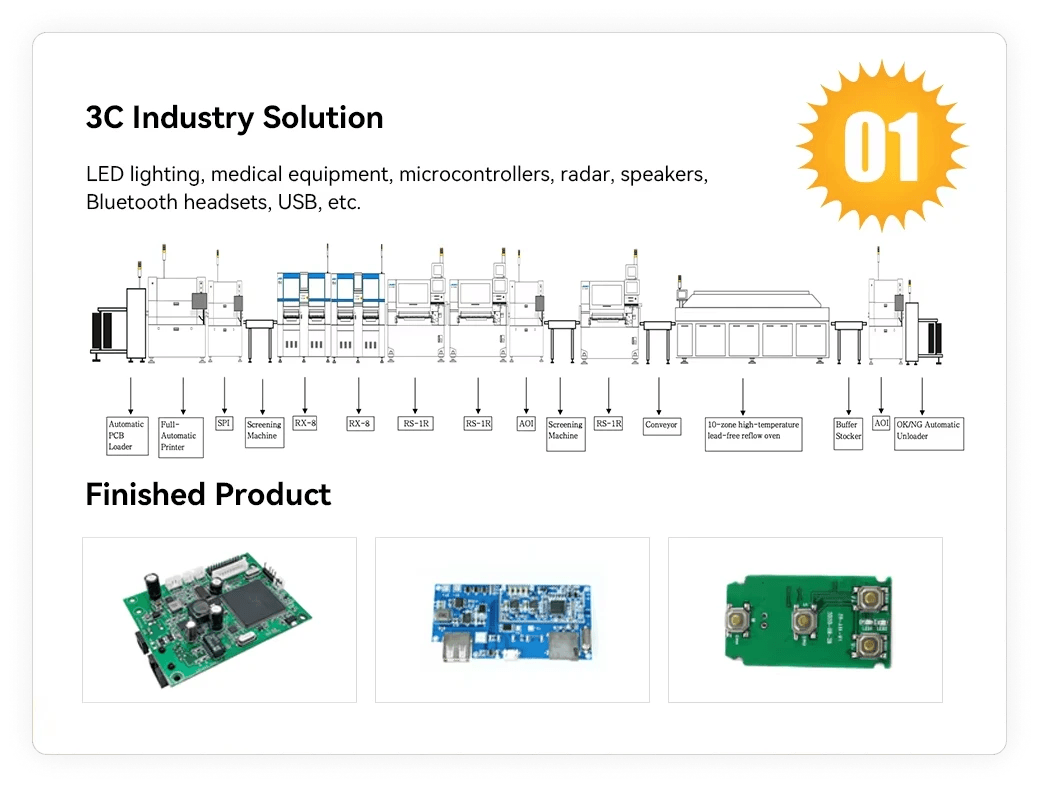
When diving into the world of surface mount PCB assembly, it's essential to understand the distinction between Surface Mount Technology (SMT) and Surface Mount Devices (SMD). While they may seem interchangeable at first glance, these terms represent different aspects of electronic assembly that play critical roles in modern electronics. In this section, we’ll clarify these concepts and explore their implications for design and project selection.
Clarifying Surface Mount Devices vs. SMT
To put it simply, SMT refers to the entire process of assembling electronic components onto a circuit board without the need for through-holes, while SMD denotes the actual components designed specifically for this method. Surface mount devices are typically smaller than their through-hole counterparts, allowing for more compact designs in surface mount PCB assembly. Understanding this distinction is crucial when discussing what is surface mount in PCB? because it helps delineate the technology from its components.
In essence, SMT encompasses everything from soldering techniques to machine operations involved in placing SMD on a printed circuit board. This means that while all SMDs are part of an SMT assembly process, not all elements involved in SMT are classified as SMDs themselves. Recognizing this difference can significantly impact your approach when considering what is a surface mount assembly? and how best to implement it.
Design Implications of SMD
The choice between using SMDs versus traditional components has significant design implications due to their size and layout flexibility. When opting for surface mount devices in your designs, you can achieve higher component density on your boards, which is particularly beneficial for compact electronics like smartphones or wearables. This shift towards smaller devices also influences thermal management considerations since more heat-generating components are packed closer together.
Moreover, designing with SMDs often leads to shorter signal paths which can enhance performance by reducing latency—a crucial factor when considering what is the difference between SMT and THM? The ability to design high-frequency circuits with minimal interference makes SMDs increasingly attractive in modern applications where speed matters most. Thus, understanding these design implications will guide you toward making informed decisions about your next project.
Choosing Between SMT and SMD for Projects
When deciding whether to use SMT or focus on specific surface mount devices like SMDs for your projects, consider factors such as cost-effectiveness and manufacturing capabilities available at your disposal. If you're looking at high-volume production runs where efficiency reigns supreme, embracing both SMT processes alongside tailored SMD choices will likely yield better results—think faster production times without compromising quality!
Additionally, evaluating your project's requirements against the benefits offered by each approach can help you determine which method aligns best with your goals; after all, understanding what is a surface mount assembly? involves knowing how each component plays its part within that framework. Ultimately, balancing design preferences with practical constraints will ensure you make an informed decision that suits both functionality and budgetary needs.
Exploring the SMT Process
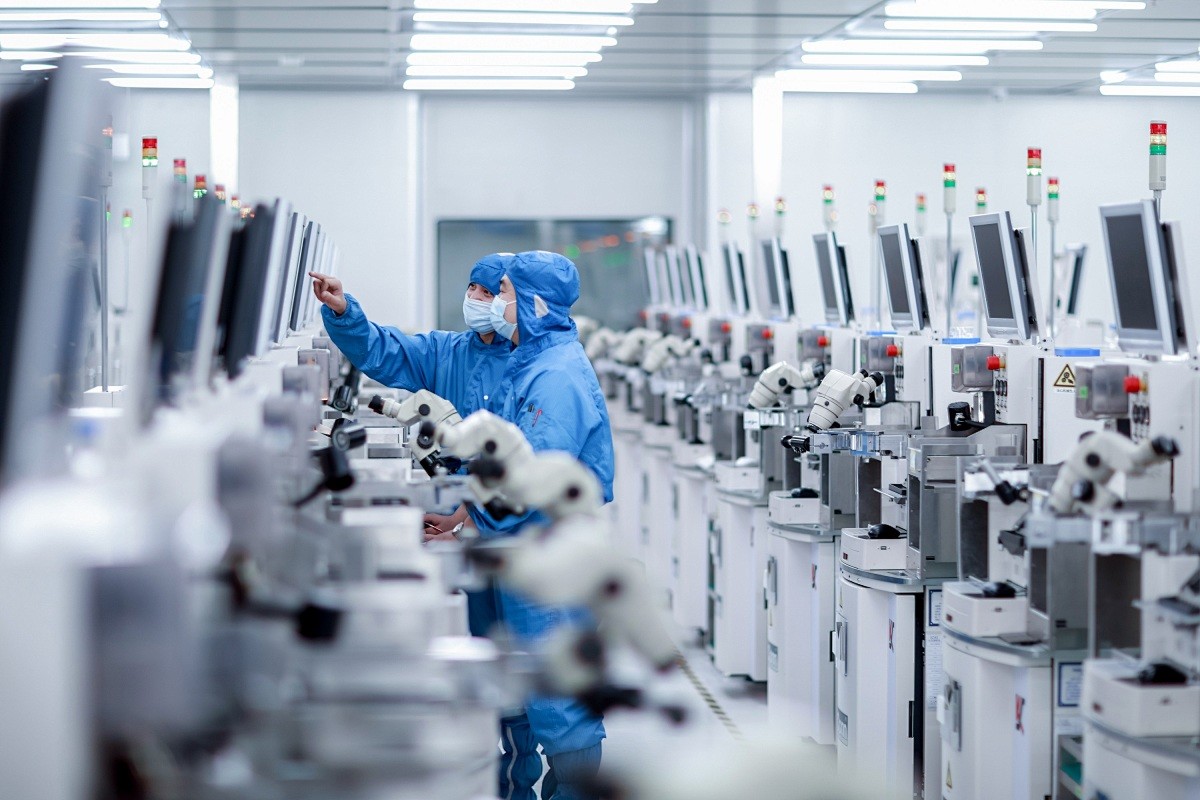
The surface mount PCB assembly process is a fascinating journey from design to final product, showcasing the intricate dance of technology and precision. Understanding this process is crucial for anyone involved in electronics, whether you're a hobbyist or a professional engineer. Let’s dive into the step-by-step breakdown of SMT, explore the essential tools and equipment used, and take a look at some of the latest innovations in SMT technology.
Step-by-Step Breakdown of SMT
The SMT process begins with designing the printed circuit board (PCB) layout using specialized software that incorporates surface mount technology specifications. Once the design is finalized, it transitions into production where components are placed on the PCB using an SMT machine that accurately positions each piece according to the design layout. After placement, solder paste is applied to specific pads on the board before it undergoes reflow soldering—a critical step that ensures all components are securely attached.
Next comes inspection and testing, where quality control measures ensure that every connection meets industry standards. This involves automated optical inspection (AOI) systems that check for misaligned components or insufficient solder joints—essentially asking, What is a surface mount assembly? in terms of quality assurance! Finally, once everything checks out, boards are packaged and shipped off to their next destination—whether that's further assembly or direct delivery to customers.
Tools and Equipment Used in SMT
The success of surface mount PCB assembly heavily relies on advanced tools and equipment designed specifically for efficiency and accuracy. At the heart of this setup lies the SMT machine—an automated marvel that takes care of component placement with pinpoint precision. Complementing these machines are stencils used for applying solder paste evenly on pads, ensuring optimal connections during reflow.
Additionally, various types of inspection equipment play crucial roles throughout the process; from AOI systems to X-ray machines for inspecting hidden solder joints beneath components—these tools help answer questions like What is the difference between SMT and THM? by emphasizing how automation enhances reliability over traditional methods. Lastly, hand tools such as tweezers or soldering irons may be employed for manual adjustments or repairs when necessary.
Innovations in SMT Technology
As technology evolves at breakneck speed, so too does surface mount PCB assembly innovation! One notable advancement includes enhanced pick-and-place machines equipped with artificial intelligence (AI), which optimize component placement based on real-time data analysis—making them faster and more accurate than ever before. Furthermore, advancements in solder materials have led to improved thermal management capabilities within devices; this addresses concerns about overheating while maximizing performance longevity.
Moreover, industry trends now emphasize eco-friendly practices within manufacturing processes; innovations such as lead-free solders have become standard practice due to regulatory changes aimed at reducing environmental impact—a clear indication that sustainability matters even within high-tech fields like electronics! As we continue exploring what makes up effective surface mount PCB assembly processes today—and beyond—we can only anticipate more exciting developments ahead!
Conclusion
In the rapidly evolving landscape of electronics, surface mount PCB assembly stands out as a pivotal technology driving innovation and efficiency. As we look to the future, advancements in SMT processes will continue to enhance performance, reduce costs, and enable more compact designs. The integration of smart technologies into SMT machines is likely to redefine standards in quality control and production speed, making surface mount assembly even more attractive for manufacturers.
The Future of Surface Mount PCB Assembly
The future of surface mount PCB assembly is bright as manufacturers increasingly adopt automation and AI-driven technologies. Innovations in the SMT process will not only streamline production but also improve accuracy and reduce waste, leading to a more sustainable approach in electronics manufacturing. Moreover, as consumer demand for smaller and smarter devices grows, the need for efficient surface mount assembly techniques will become even more critical.
Why Choose Bensun Technology for SMT Needs
When it comes to selecting a partner for your SMT needs, Bensun Technology stands out with its commitment to quality and cutting-edge solutions. With extensive experience in what is surface mount in PCB processes, they leverage advanced SMT machines that ensure precision and reliability in every project. Their expertise not only encompasses what is a surface mount assembly but also extends to providing tailored solutions that meet specific client requirements.
Final Thoughts on SMT Industry Trends
As we delve deeper into the nuances of what is the difference between SMT and THM or explore what is the difference between SMT and SMD, it's clear that each technology has its place in modern electronics design. However, with its superior efficiency and adaptability, surface mount PCB assembly continues to dominate many applications across various industries. Keeping an eye on emerging trends can help businesses stay ahead of the curve while choosing suitable methods like the SMT process or utilizing state-of-the-art SMT machines.