Introduction
In the fast-paced world of electronics manufacturing, discovering SMT mounter machine solutions is key to staying competitive. Surface Mount Technology (SMT) has become a cornerstone of modern production processes, allowing manufacturers to produce smaller, more efficient devices at an unprecedented speed. At the heart of this revolution are pick and place machines, which are transforming how components are assembled onto circuit boards.
Discovering SMT Mounter Machine Solutions
The quest for optimal efficiency in electronics production leads many businesses to explore the capabilities of SMT mounter machines. These machines automate the placement of electronic components on printed circuit boards (PCBs), ensuring precision and reducing human error. By leveraging advanced technology in their operations, manufacturers can significantly enhance their output while maintaining high-quality standards.
Importance of SMT Technology in Manufacturing
SMT technology plays a crucial role in contemporary manufacturing by enabling the production of compact and lightweight electronic devices. This technique allows for a higher density of components on PCBs compared to traditional methods, making it indispensable for industries ranging from consumer electronics to automotive applications. As demand for miniaturized products continues to rise, embracing surface mount SMT becomes essential for manufacturers aiming to thrive in a competitive landscape.
How Pick and Place Machines Revolutionize Production
Pick and place machines have revolutionized production lines by streamlining the assembly process with remarkable speed and accuracy. With capabilities that include automated feeding systems and real-time monitoring, these machines maximize throughput while minimizing waste. The integration of such innovative technology not only enhances productivity but also allows manufacturers to adapt quickly to changing market demands without compromising quality.
What is Surface Mount Technology?
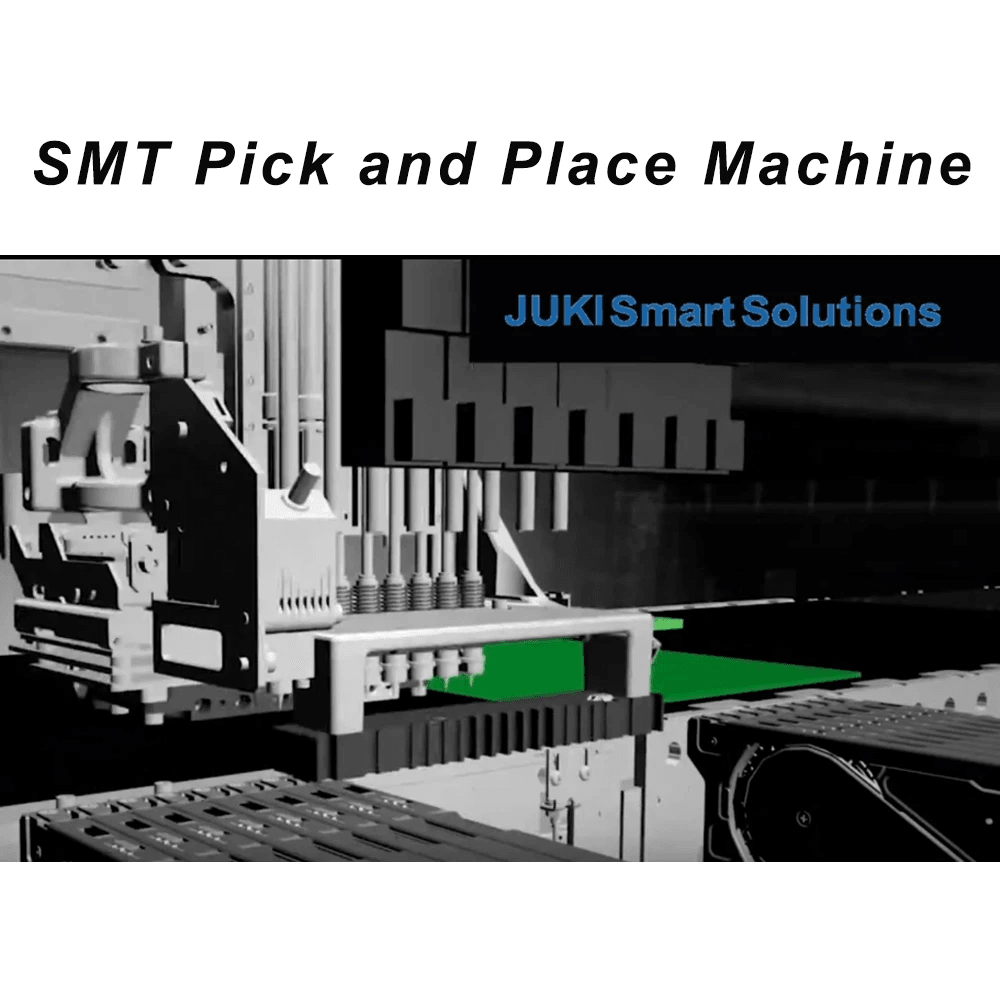
Surface Mount Technology (SMT) has transformed the landscape of electronic manufacturing, allowing for greater efficiency and miniaturization in circuit design. This innovative approach involves mounting components directly onto the surface of printed circuit boards (PCBs), eliminating the need for drilling holes. With the aid of advanced smt mounter machines and pick and place machines, SMT technology has become a cornerstone in modern production lines.
Definition of SMT and its Benefits
Surface Mount Technology (SMT) refers to a method where electronic components are mounted directly onto the surface of PCBs rather than being inserted through holes. One major benefit of SMT is its ability to support smaller and lighter designs, which is crucial in today's compact electronic devices. Additionally, SMT technology enhances manufacturing efficiency by allowing for higher component density and faster assembly speeds through automated processes using sophisticated pick & place machines.
Components Used in Surface Mount Technology
The components utilized in surface mount technology are typically smaller than their through-hole counterparts, including resistors, capacitors, diodes, and integrated circuits (ICs). These components often have flat leads or no leads at all, making them ideal for placement by smt mounter machines that can handle high-speed operations with precision. The use of these miniaturized parts not only contributes to more compact device designs but also improves performance by reducing signal paths.
Differences Between SMT and Through-Hole Technology
The primary distinction between surface mount technology (SMT) and through-hole technology lies in how components are attached to PCBs. While through-hole technology requires drilling holes into the board for component leads to pass through, SMT allows for direct mounting on surfaces without any need for drilling. This difference results in various advantages; SMT generally offers better electrical performance due to shorter connections while also significantly reducing board space requirements—an essential factor when considering machine pick and place operations.
The Role of SMT Mounter Machines
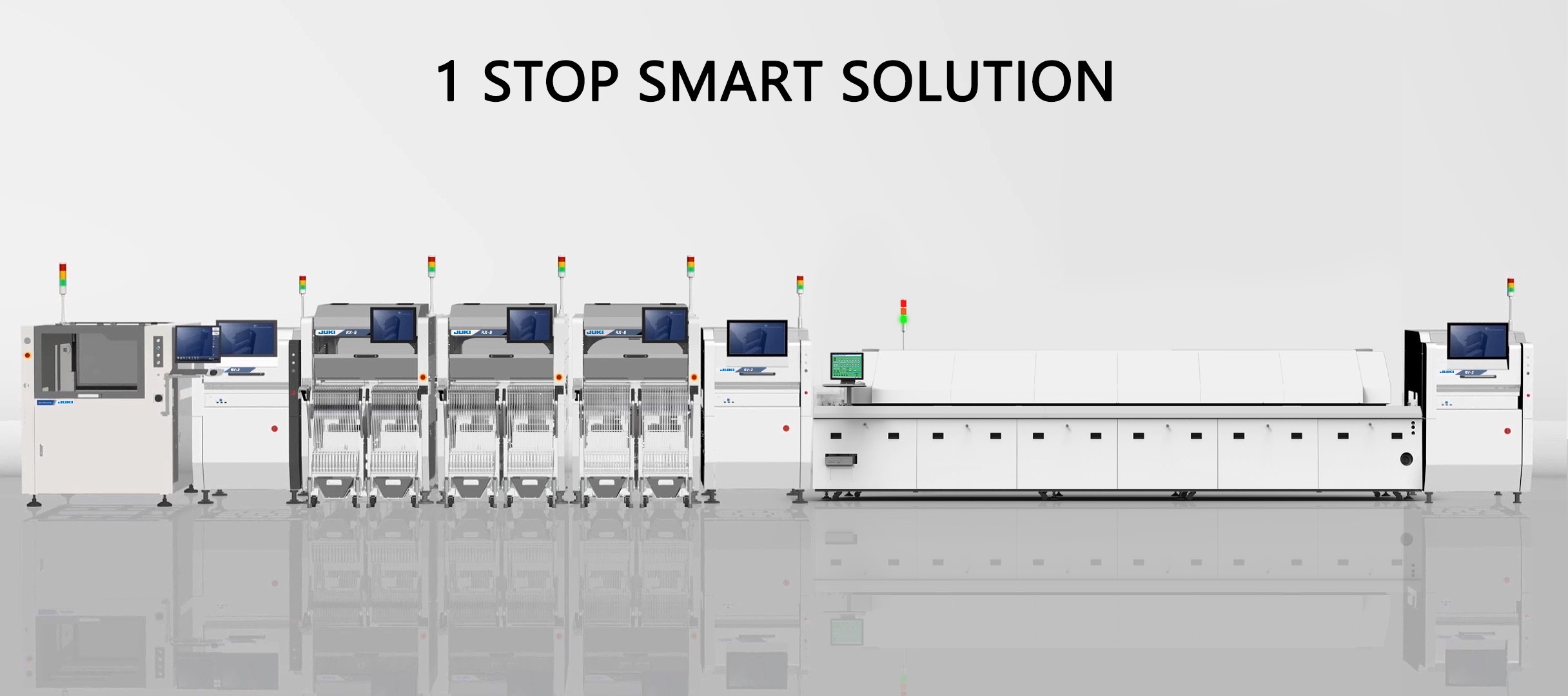
SMT mounter machines are the unsung heroes of modern electronics manufacturing, playing a pivotal role in the efficiency and quality of production. These machines automate the process of placing surface mount components onto printed circuit boards (PCBs) with incredible precision and speed. By leveraging advanced technology, pick and place machines streamline operations, ensuring that manufacturers can meet high demand without sacrificing quality.
Understanding the Pick and Place Process
At its core, the pick and place process involves several key steps that transform raw materials into fully functional electronic devices. First, the SMT mounter machine identifies components from a feeder system, swiftly picking them up with suction or mechanical grippers. Next, it accurately places these components onto designated spots on the PCB using sophisticated vision systems to ensure proper alignment—a critical factor in surface mount technology that guarantees reliable performance.
This process is highly dynamic; modern pick & place machines can handle a variety of component shapes and sizes while adapting to different production runs. As technology advances, these machines are becoming increasingly adept at managing complex layouts, which is essential for manufacturers looking to innovate their product lines. Ultimately, understanding this intricate process highlights why investing in high-quality SMT technology is vital for any manufacturer aiming for excellence.
Key Features of Modern SMT Mounting Machines
Modern SMT mounting machines come equipped with an array of features designed to enhance productivity and reduce downtime during operation. One standout feature is their ability to perform simultaneous placement actions; many advanced pick and place machines can position multiple components at once, significantly speeding up production cycles. Additionally, integrated software systems allow for real-time monitoring and adjustments—ensuring optimal performance throughout various stages of assembly.
Moreover, user-friendly interfaces make it easier for operators to program machine settings quickly and efficiently—reducing training time while maximizing output quality. High-resolution cameras provide precise alignment capabilities that are crucial in surface mount technology applications where even minor misalignments can lead to significant issues down the line. With these innovations combined, modern SMT mounter machines truly embody efficiency in action.
Why Efficiency Matters in SMT Production
In today’s fast-paced manufacturing landscape, efficiency isn’t just a buzzword; it’s a necessity for survival and growth within the industry. Efficient operation means reduced cycle times which directly translates into higher output rates without compromising quality—a win-win scenario for businesses utilizing SMT technology. Furthermore, streamlined processes reduce waste by minimizing errors during assembly; less rework means more profit margins stay intact.
Moreover, as consumer demands continue to rise alongside technological advancements like IoT devices or wearables requiring ever more complex PCBs—having an efficient surface mount smt setup becomes imperative for staying competitive in this market landscape. Investing in cutting-edge pick & place machinery not only enhances operational efficiency but also positions companies as leaders within their sectors by allowing them to adapt quickly to changing demands without missing a beat.
Leading SMT Mounter Brands to Consider
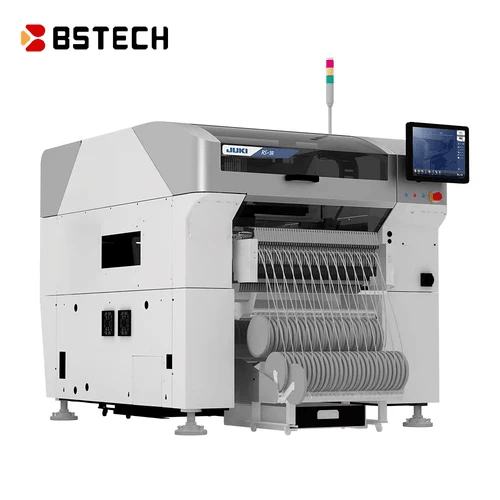
Bensun Technology: A Leader in SMT Solutions
Bensun Technology has carved a niche for itself as a powerhouse in SMT solutions, particularly with its advanced pick and place machines. Their commitment to innovation ensures that their smt mounter machines are equipped with cutting-edge features designed to enhance productivity and accuracy. With a focus on user-friendly interfaces and high-speed operation, Bensun's machines cater to various production needs while maintaining exceptional quality standards.
One of the standout aspects of Bensun's offerings is their adaptability; these pick & place machines can handle diverse component sizes and types, making them ideal for manufacturers looking to optimize their surface mount technology processes. Additionally, Bensun places great emphasis on customer support and training, ensuring that users can fully leverage their smt technology investments. This dedication positions Bensun as a top choice for companies aiming for excellence in SMT production.
Yamaha and Their Innovation in Pick & Place Machines
Yamaha has been synonymous with precision engineering for decades, and their contribution to pick and place machines is no exception. Known for their reliability and speed, Yamaha’s smt mounter machines incorporate innovative technologies that streamline manufacturing processes while reducing downtime. Their latest models feature intelligent vision systems that enhance placement accuracy—vital for complex circuit boards utilizing surface mount technology.
In addition to performance enhancements, Yamaha's commitment to sustainability sets them apart from competitors by integrating energy-efficient designs into their equipment. This not only reduces operational costs but also aligns with modern manufacturing's push toward eco-friendliness—a win-win situation! As manufacturers increasingly seek ways to improve efficiency without compromising quality, Yamaha remains at the forefront of providing solutions that meet these demands.
Panasonic’s Advancements in Surface Mount Technology
Panasonic has long been recognized as a trailblazer in electronics manufacturing—and when it comes to SMT mounter machines, they certainly don’t disappoint! Their state-of-the-art pick & place machines are engineered with robust features like advanced automation capabilities which significantly boost throughput rates while minimizing errors during assembly processes. Panasonic’s dedication to research means they continuously push boundaries within surface mount technology.
Moreover, Panasonic emphasizes seamless integration between different stages of production lines through smart connectivity options available on their equipment—allowing manufacturers greater flexibility when scaling operations or adapting designs quickly based on market needs. By investing heavily into enhancing user experience alongside technical advancements within smt surface mount technology itself; Panasonic solidifies its position as an industry leader worth considering.
Maximizing Efficiency with SMT Machines
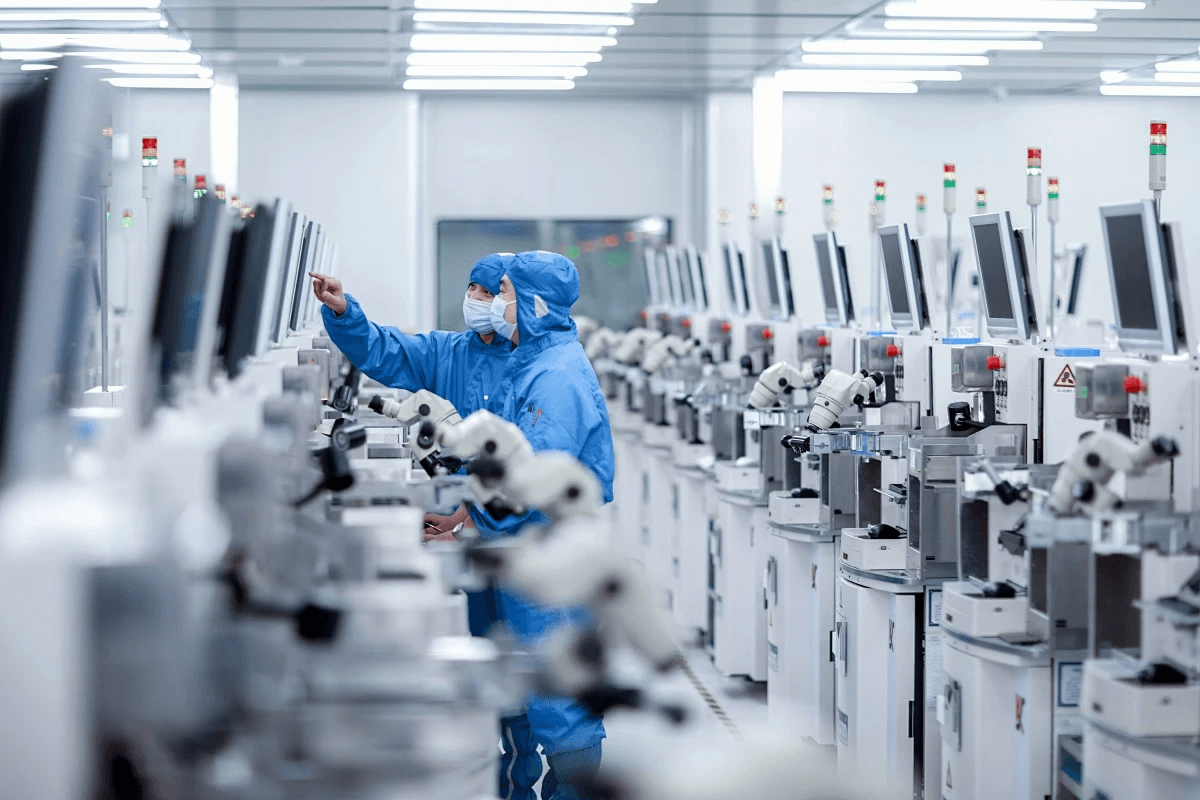
In the fast-paced world of electronics manufacturing, maximizing efficiency with SMT machines is crucial for staying competitive. With the right strategies, manufacturers can enhance the performance of their pick and place machines, ensuring that they meet production demands while maintaining high-quality standards. Here are some insights into optimizing machine pick and place operations, the importance of regular maintenance for SMT equipment, and how to effectively integrate SMT technology into production lines.
Tips for Optimizing Machine Pick and Place Operations
To get the most out of your pick and place machine, start by fine-tuning its settings for your specific production needs. Adjusting parameters like speed, placement accuracy, and component feeding can significantly enhance the overall efficiency of your surface mount technology process. Additionally, utilizing advanced software solutions can help streamline workflows and reduce cycle times in your SMT surface mount technology operations.
Another key aspect is to ensure that you are using high-quality components compatible with your SMT mounter machine. This not only reduces errors during assembly but also minimizes downtime caused by component jams or misplacements. Lastly, training operators on best practices for using pick & place machines will empower them to identify potential issues before they escalate, leading to smoother operations.
Importance of Regular Maintenance for SMT Equipment
Regular maintenance is essential to keep your SMT mounter machine running at peak performance. Just like any sophisticated piece of machinery, neglecting routine checks can lead to unexpected breakdowns that disrupt production schedules and inflate costs. Establishing a preventive maintenance schedule helps identify wear-and-tear issues early on and ensures that your pick and place machine remains reliable over time.
Moreover, performing regular cleaning on critical components such as nozzles and feeders will improve placement accuracy while extending the lifespan of your equipment. By prioritizing maintenance within your organization’s culture, you can foster an environment where quality control becomes second nature in every stage of the surface mount technology process.
Integrating SMT Technology into Production Lines
Integrating surface mount technology into existing production lines requires careful planning but offers immense rewards in terms of efficiency gains. When introducing an SMT mounter machine into a traditional assembly line setup, consider how it will interact with other machinery and processes involved in manufacturing. A well-thought-out integration plan ensures seamless collaboration between different technologies while optimizing overall workflow.
Additionally, leveraging automation tools alongside your pick & place machines can significantly reduce manual labor requirements while enhancing precision during assembly tasks. Implementing real-time monitoring systems allows manufacturers to track performance metrics easily; this data-driven approach enables continuous improvement across all stages of production involving surface mount technology. Embracing these advancements positions companies as leaders in innovation within their respective markets.
The Future of SMT Technology
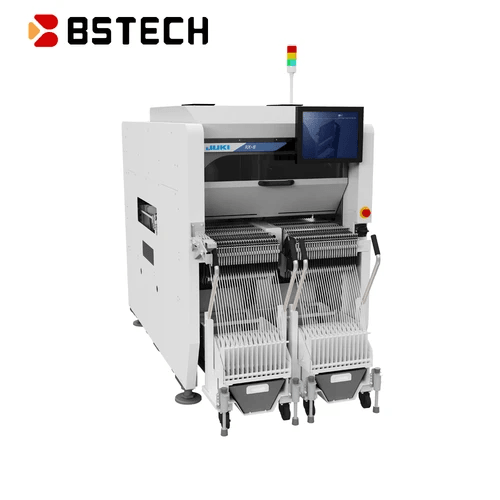
The landscape of SMT technology is continuously evolving, driven by innovation and the demand for higher efficiency in manufacturing processes. As we look forward, several emerging trends are shaping the future of surface mount technology, particularly in the realm of pick and place machines. These advancements promise to enhance productivity, reduce costs, and streamline operations for manufacturers globally.
Emerging Trends in SMT Surface Mount Technology
One significant trend is the miniaturization of components used in surface mount technology. As devices become smaller and more compact, the demand for advanced SMT mounter machines that can accurately handle these tiny parts increases. Additionally, there's a growing emphasis on smart technologies that integrate AI and machine learning into pick & place machines to optimize their performance through real-time data analysis.
Another notable trend is the shift towards environmentally friendly practices within SMT manufacturing processes. Companies are increasingly adopting sustainable materials and energy-efficient smt mounter machines to minimize their ecological footprint while maintaining high production standards. Furthermore, modular designs are gaining traction, allowing manufacturers to adapt their equipment easily as new technologies emerge.
Finally, enhanced connectivity through Industry 4.0 initiatives is revolutionizing how manufacturers operate their surface mount technology lines. With IoT-enabled devices and cloud-based solutions becoming commonplace in factories, real-time monitoring and remote management of pick and place machines are now feasible options for many businesses.
The Impact of Automation on SMT Manufacturing
Automation stands at the forefront of transforming SMT manufacturing processes today. The integration of automated systems into production lines significantly boosts efficiency by minimizing human error and increasing speed—two critical factors when it comes to machine pick and place operations. This shift not only enhances output but also allows skilled workers to focus on more complex tasks that require human intervention.
Moreover, automated smt mounter machines facilitate better quality control throughout the manufacturing process. By employing advanced sensors and imaging systems, these machines can detect defects or misalignments at unprecedented speeds—ensuring that only high-quality products make it through production lines while reducing waste significantly. Consequently, this automation trend fosters a culture of continuous improvement within organizations striving for excellence.
Lastly, as automation becomes more prevalent in surface mount technology applications, companies will need to invest in training programs for their workforce to adapt effectively to these changes. Upskilling employees will be essential not just for operating sophisticated machinery but also for understanding how to leverage data analytics generated from automated systems—ensuring long-term success in an increasingly competitive market.
Predictions for the Next Generation of SMT Mounters
Looking ahead, we can expect groundbreaking advancements from next-generation smt mounter machines that will redefine industry standards once again. One prediction is that future pick & place machines will incorporate even greater levels of precision with improved vision systems capable of identifying components with an accuracy level previously thought unattainable—ultimately leading to higher yields per batch produced.
Additionally, we might see increased collaboration between different types of machinery on production floors as manufacturers seek seamless integration across various stages—from assembly line robots working alongside smt technology solutions like pick and place machines—to ensure optimal workflow efficiency throughout every process step involved in creating electronic devices.
Finally, sustainability will likely play an even more significant role than ever before; upcoming models may utilize eco-friendly materials or energy-efficient designs aimed at reducing overall carbon footprints during operation without sacrificing performance levels required by modern electronics manufacturing standards—a win-win situation where profitability meets responsibility!
Conclusion
In the fast-paced world of electronics manufacturing, SMT mounter machines stand out as pivotal tools that unlock both efficiency and precision. The integration of surface mount technology has transformed traditional production methods, allowing for a level of automation and speed that was once unimaginable. By harnessing the capabilities of pick and place machines, manufacturers can streamline their operations while maintaining high-quality standards.
Unlocking Potential with SMT Mounter Solutions
The potential unlocked by SMT mounter solutions is immense, particularly in enhancing productivity and reducing waste. With advanced pick & place machine technology, companies can achieve faster assembly times without compromising on accuracy or reliability. This not only leads to cost savings but also opens up new avenues for innovation in product design and manufacturing processes.
Choosing the Right Pick and Place Machine for Your Needs
Selecting the right pick and place machine is crucial for maximizing your production capabilities. Factors such as component size, production volume, and budget all play significant roles in determining which SMT mounter machine is best suited for your specific needs. By carefully evaluating these aspects, you can ensure that you invest in equipment that aligns with your operational goals while leveraging the benefits of surface mount technology.
Staying Ahead with Bensun Technology’s Innovations
Bensun Technology continues to lead the charge in SMT advancements, offering state-of-the-art solutions that keep manufacturers ahead of industry trends. With a focus on enhancing performance through innovative designs in their smt mounter machines, Bensun ensures that users benefit from improved efficiency and reliability. By staying updated with their latest offerings, businesses can maintain a competitive edge in an ever-evolving market landscape.