Introduction
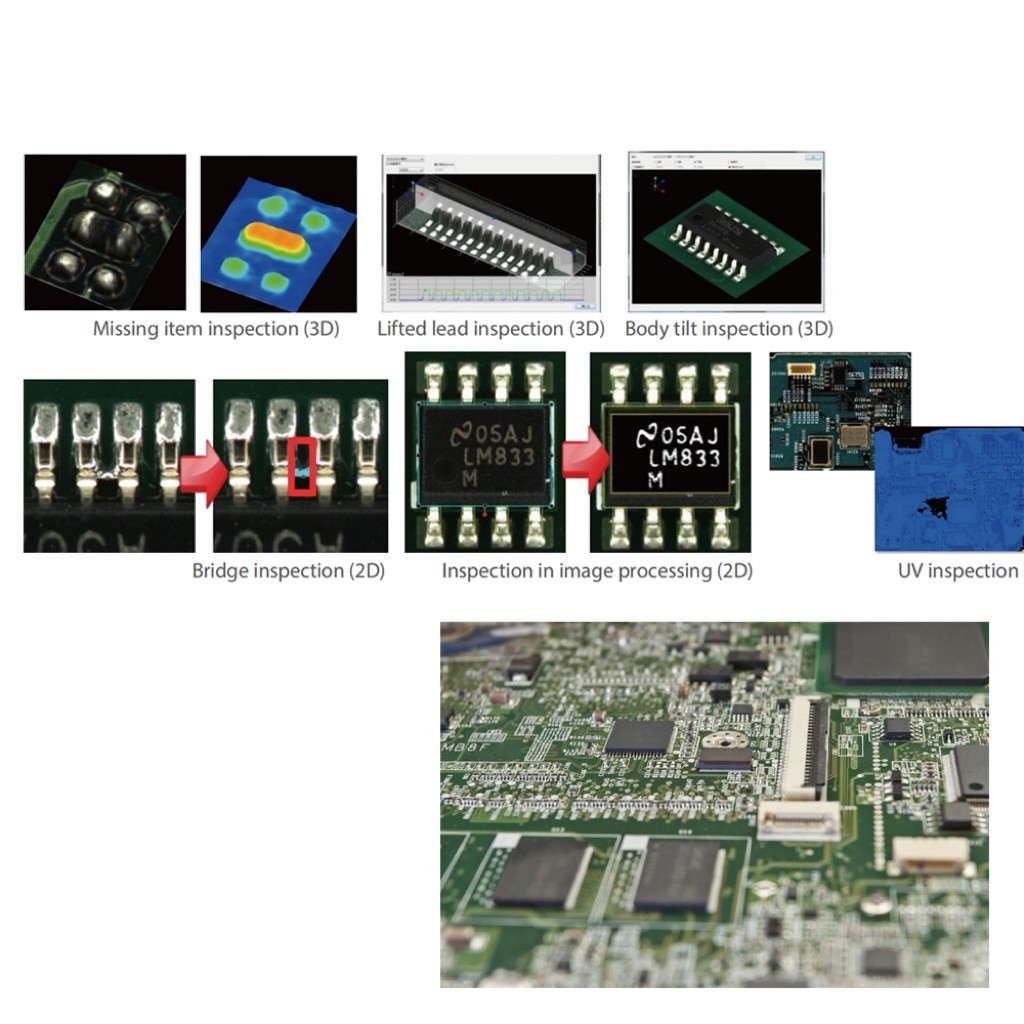
In the ever-evolving world of electronics, understanding the nuances of different assembly technologies is crucial for both manufacturers and hobbyists alike. Among these technologies, through hole technology and PCB surface mount assembly stand out as two primary methods for mounting components onto printed circuit boards (PCBs). Each method has its own unique advantages, applications, and considerations that can significantly impact the efficiency and performance of electronic devices.
Understanding Through Hole Technology
Through hole technology involves the insertion of component leads through holes drilled in a PCB, followed by soldering on the opposite side. This method is known for providing robust mechanical connections and is particularly favored in high-stress environments. However, while it offers durability, it can be more labor-intensive compared to other methods like surface mount assembly.
Exploring PCB Surface Mount Assembly
PCB surface mount assembly (SMA) represents a modern approach where components are mounted directly onto the surface of a PCB without the need for drilled holes. This technique allows for higher density circuit designs and smaller overall board sizes, making it ideal for compact electronic devices. As we delve into this topic, we will address questions such as What is a surface mount assembly? and What is surface mount in PCB? to clarify its significance in contemporary manufacturing.
Importance of Choosing the Right Method
Selecting between through hole technology and PCB surface mount assembly can greatly influence production costs and product performance. Factors such as component size, application requirements, and manufacturing capabilities play pivotal roles in this decision-making process. Understanding these differences will not only help you choose wisely but also enable you to ask informed questions like How to make a surface mount PCB? or explore terms like What is the difference between SMD and SMT?
What is Through Hole Technology?
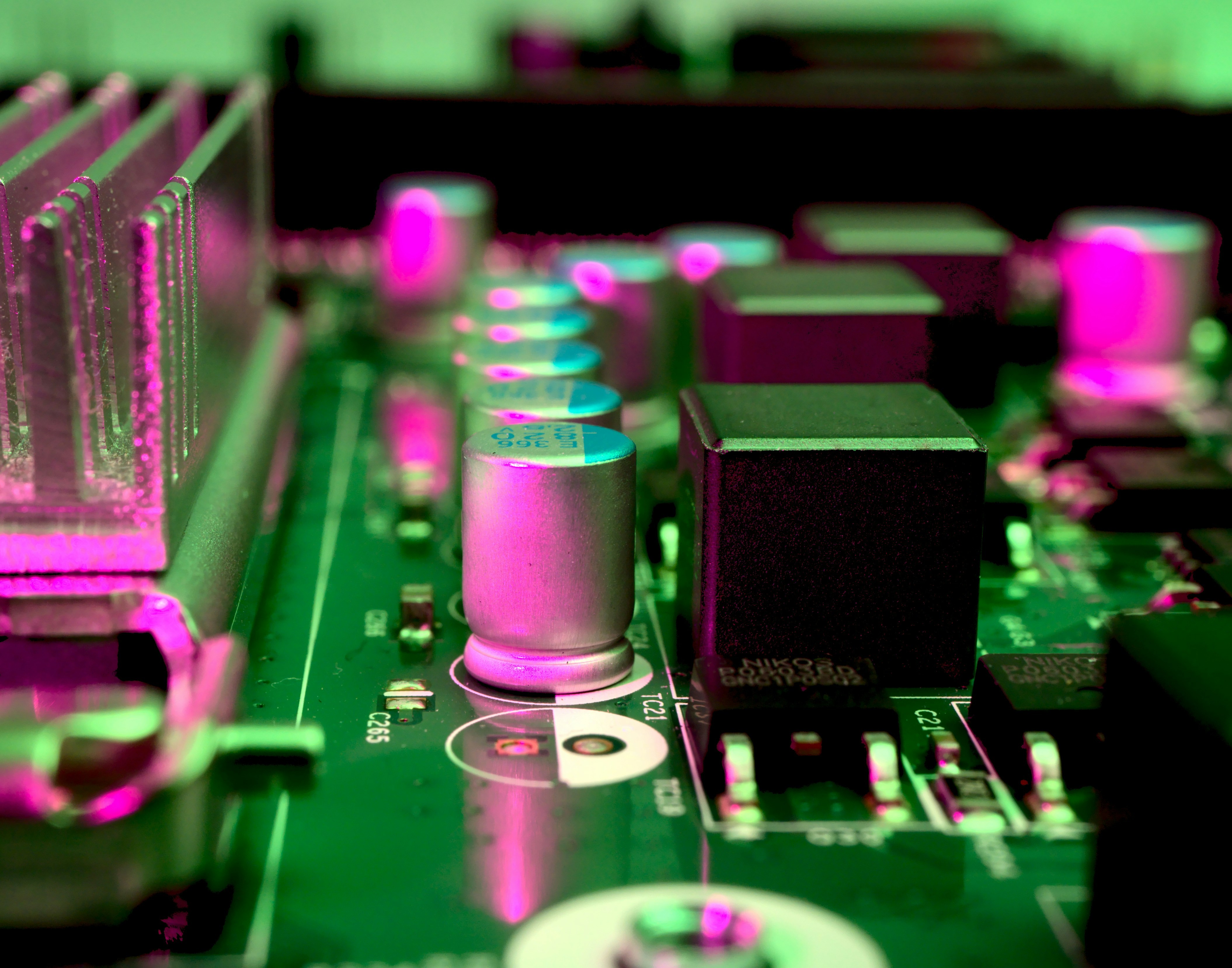
Through hole technology (THT) is a method used in electronic circuit assembly where components are inserted into holes drilled into a printed circuit board (PCB) and soldered on the opposite side. This technique has been around for decades and is fundamental to many electronic devices. Understanding through hole technology is crucial, especially when considering options like PCB surface mount assembly.
Definition and Components
Through hole technology involves components that have leads or pins that pass through the PCB's holes. These leads are then soldered to pads on the opposite side, creating a robust connection that can withstand mechanical stress. Common components used in THT include resistors, capacitors, diodes, and integrated circuits, making it versatile for various applications.
Advantages of Through Hole Assembly
One of the main advantages of through hole assembly is its durability; connections made with this method tend to be more resistant to physical stress compared to surface mount counterparts. Additionally, THT allows for easier repair and replacement of components due to their accessibility from both sides of the PCB. Moreover, through hole technology can accommodate larger components that might not fit well with surface mount options.
Common Applications of Through Hole
Through hole technology finds its niche in applications requiring high reliability and performance under challenging conditions, such as aerospace and military electronics. It's also prevalent in prototyping environments where modifications are frequent since it allows for easy component changes without extensive rework on the PCB layout. Finally, many educational kits utilize through hole technology because it provides a clear understanding of basic electronic principles.
What is PCB Surface Mount Assembly?

PCB surface mount assembly is a modern method of attaching electronic components to printed circuit boards (PCBs) using surface mount technology (SMT). Unlike traditional through-hole technology, where components are inserted into drilled holes, surface mount assembly places components directly onto the board's surface. This innovative approach allows for more compact designs and higher component density, making it a preferred choice for many manufacturers.
Definition and Key Features
So, what is a surface mount assembly? In essence, it involves soldering components that have small pads instead of leads that go through the PCB. Key features include smaller component sizes, which enable tighter spacing on the board; automated assembly processes that significantly speed up production; and the ability to use both sides of the PCB for mounting components. This technique has revolutionized PCB design by allowing engineers to create more complex circuits in less space.
Benefits of Surface Mount Technology
The benefits of surface mount technology are numerous and compelling. First off, it allows for higher circuit density due to smaller component sizes; this means you can fit more functionality into a smaller area—ideal for today's compact gadgets! Additionally, PCB surface mount assembly typically results in lower manufacturing costs because it can be automated easily, reducing labor costs while increasing production speed. Lastly, SMT often enhances electrical performance by minimizing lead inductance and resistance.
Typical Uses of Surface Mount Assembly
Surface mount assembly finds its way into a variety of applications across multiple industries. You’ll commonly see it in consumer electronics like smartphones and tablets where space is at a premium but performance cannot be compromised. Other typical uses include automotive electronics, medical devices, and telecommunications equipment—all areas where high reliability and compactness are crucial. With such versatility in applications, it's clear why many pcb surface mount assembly manufacturers prefer this method over traditional techniques.
What is the Difference Between SMD and SMT?
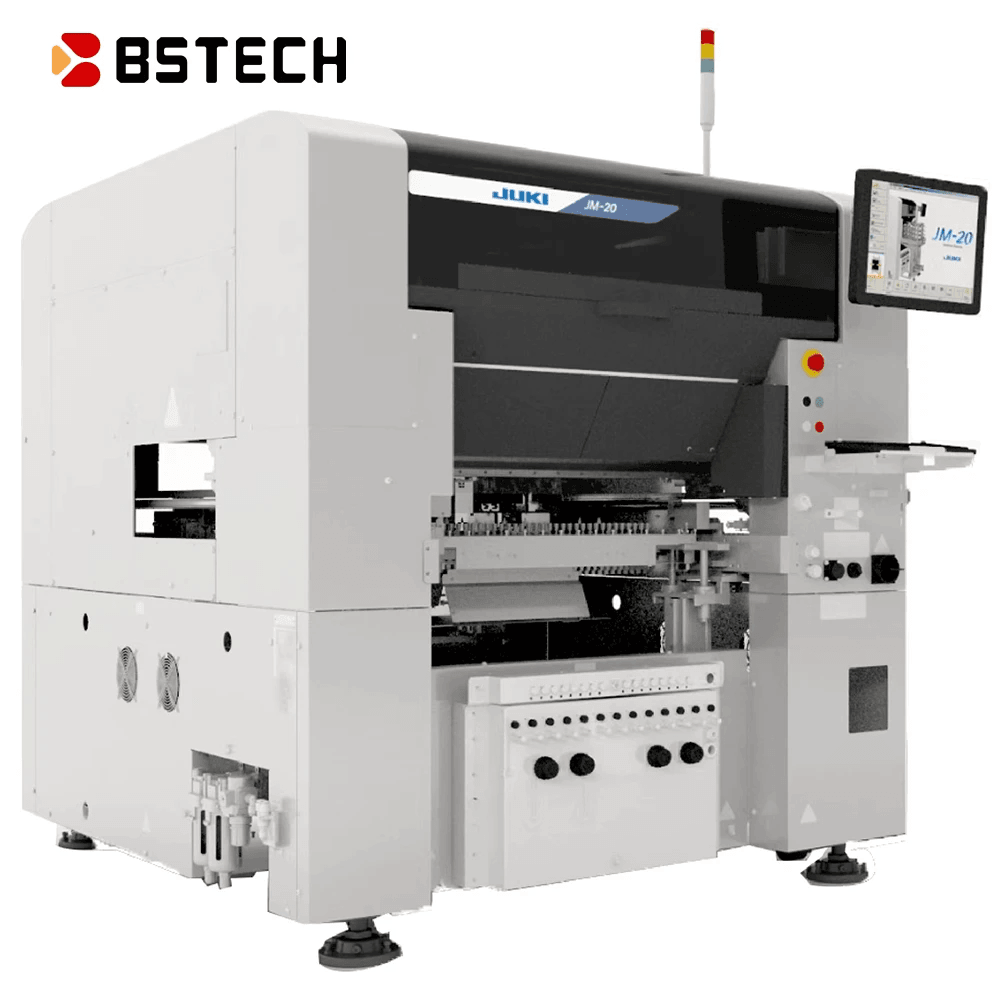
When navigating the realm of PCB surface mount assembly, it's essential to understand the nuanced terms associated with it. SMD (Surface-Mount Device) and SMT (Surface-Mount Technology) are often used interchangeably, but they refer to different concepts within the assembly process. To clarify, SMD refers specifically to the components that are mounted on the PCB, while SMT refers to the entire technology and methods used for mounting these components.
Clarifying Terminology
Understanding what is a surface mount assembly is key in distinguishing between SMD and SMT. In essence, SMDs are components designed for surface mounting, which means they do not have leads that go through holes in a PCB like traditional through-hole components. On the other hand, SMT encompasses all techniques and processes involved in placing these SMDs onto PCBs during assembly.
The distinction matters because it influences how we approach design and production in PCB manufacturing. For example, knowing what is surface mount in PCB can help engineers choose suitable components for their designs while considering factors like size, weight, and performance. This clarity aids manufacturers in selecting appropriate pcb surface mount assembly kits tailored to their specific needs.
Key Differences in Techniques
The primary difference between SMD and SMT lies in their roles within the assembly process: one refers to the actual devices while the other describes how those devices are assembled onto a board. In terms of techniques, SMT typically employs automated machinery for precision placement of SMDs on PCBs, leading to faster production rates compared to manual methods often associated with through-hole technology.
Moreover, when discussing how to make a surface mount PCB, one must consider that using SMT allows for higher component density on boards due to smaller sizes of SMDs. This efficiency not only saves space but also enhances performance by reducing signal paths—an advantage over traditional through-hole assemblies where larger components may take up more room on a board.
Impact on Design and Production
The differences between SMD and SMT significantly impact both design considerations and production workflows for pcb surface mount assembly manufacturers. By utilizing SMT techniques with SMDs, designers can create more compact circuit boards that accommodate advanced functionalities without increasing size or weight—a crucial factor for modern electronic devices.
Additionally, understanding these differences helps businesses evaluate pcb surface mount assembly price trends effectively as they determine whether investing in automated systems or sticking with manual processes aligns better with their production goals. The choice between using SMDs or opting for traditional methods can influence overall project costs as well as time-to-market strategies.
In conclusion, recognizing what is the difference between SMD and SMT equips engineers and manufacturers alike with critical insights necessary for making informed decisions about their PCB designs and assemblies—ultimately leading them toward successful product development.
How to Make a Surface Mount PCB?
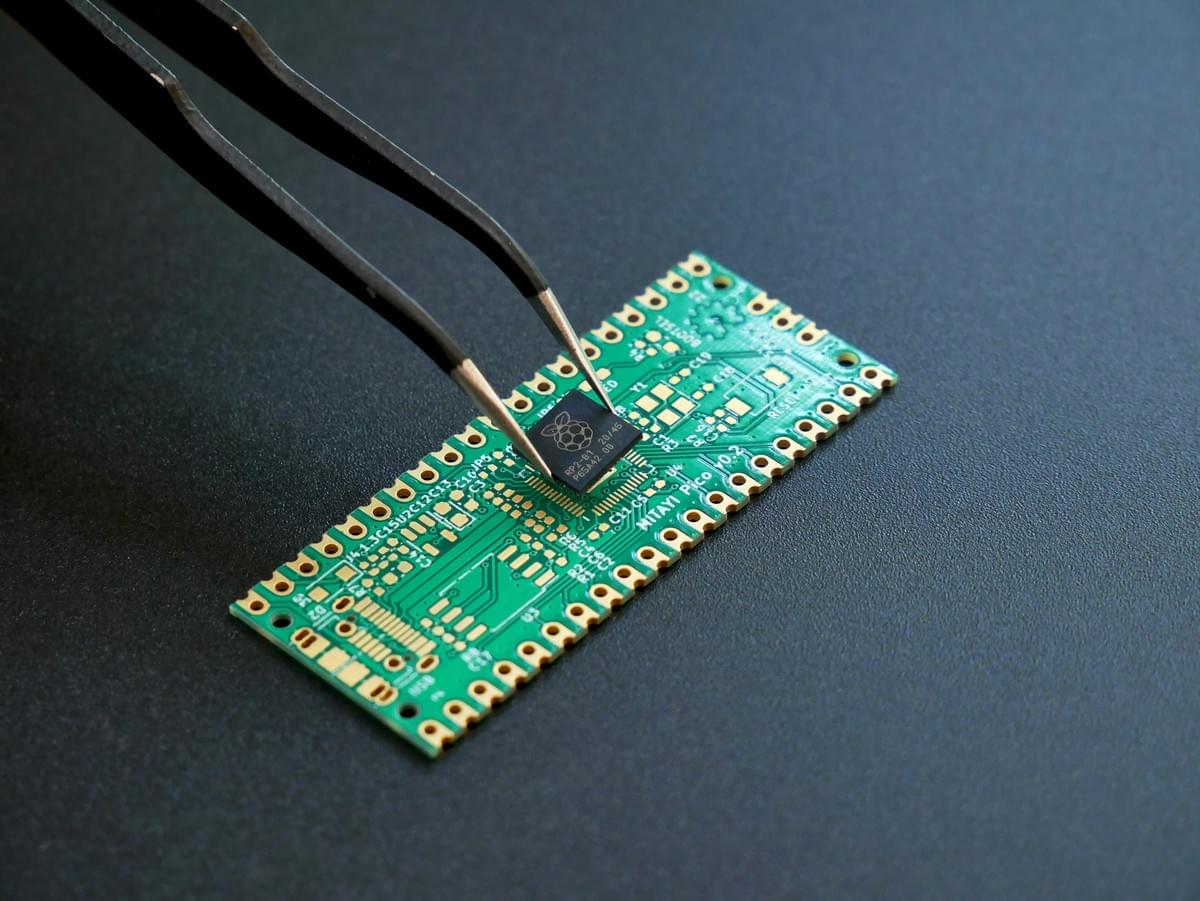
Creating a surface mount PCB can be an exciting endeavor, transforming your electronic ideas into tangible products. The process requires precision, the right tools, and an understanding of what is surface mount in PCB technology. Whether you’re a hobbyist or a professional looking to utilize pcb surface mount assembly, this guide will set you on the right path.
Step-by-Step Process Overview
To kick things off, start with designing your PCB layout using software that supports surface mount technology (SMT). Once your design is ready, print the layout onto a copper-clad board and etch it to create traces that will connect components. After preparing the board, apply solder paste to the pads where your components will sit; this step is critical in ensuring proper adhesion during assembly.
Next comes placing the components on the board—this requires precision since surface mount devices (SMD) are much smaller than their through-hole counterparts. Once all components are positioned correctly, it’s time for soldering; you can use either reflow ovens or hot air guns depending on your setup. Finally, inspect your work for any misalignments or soldering issues before testing the assembled PCB.
Essential Tools and Materials
To successfully execute a pcb surface mount assembly project, you'll need some essential tools and materials at hand. Start with a good quality soldering station or reflow oven tailored for SMD work; these are indispensable for achieving reliable connections without damaging sensitive components. Additionally, having tweezers specifically designed for handling small parts will make component placement much easier.
You’ll also require solder paste and stencil for applying it accurately onto pads—this ensures optimal solder joints during heating processes. Other materials include a suitable substrate (like FR-4), various SMD components from resistors to ICs based on your design requirements, and cleaning agents to remove flux residue post-assembly. Lastly, consider investing in a pcb surface mount assembly kit that includes all necessary items for beginners.
Tips for Successful Assembly
When embarking on how to make a surface mount PCB effectively, keep these tips in mind: first and foremost, ensure that your workspace is clean and well-lit; this helps prevent errors while handling tiny components. Secondly, double-check component orientation before soldering; reversing an SMD can lead to costly mistakes that might require reworking or scrapping altogether.
Moreover, practice patience—especially if you're new to pcb surface mount assembly techniques—as rushing can lead to oversight of critical details like alignment or insufficient solder application. Lastly, familiarize yourself with what is the difference between SMD and SMT since understanding their characteristics will enhance both design efficiency and production quality as you delve deeper into electronics manufacturing.
Comparing Costs: Through Hole vs Surface Mount

PCB Surface Mount Assembly Price Trends
The price of PCB surface mount assembly has seen a notable shift over the years. As demand for smaller and more efficient electronics grows, manufacturers have adapted their pricing strategies accordingly. While traditional through hole methods might seem cheaper at first glance, the long-term savings associated with surface mount technology often make it a more attractive option.
Moreover, advancements in manufacturing techniques have contributed to lowering the overall costs of PCB surface mount assembly kits. The increased competition among PCB surface mount assembly manufacturers has also driven prices down while maintaining quality standards. Consequently, businesses can benefit from reduced production costs without compromising on performance.
Factors Influencing Cost
Several factors play a pivotal role in determining the overall cost of both through hole and surface mount assemblies. First and foremost is the complexity of the design; intricate layouts requiring advanced technology will naturally incur higher expenses. Additionally, component selection significantly impacts pricing—some components used in a surface mount assembly may be more expensive than their through hole counterparts.
Labor costs are another critical consideration; while automated processes can streamline PCB surface mount assembly, skilled technicians are still needed for quality assurance and troubleshooting. Moreover, lead times can influence pricing as well; if you need rapid prototyping or short runs, expect to pay a premium for expedited services. Understanding these factors will help you make informed decisions about which method best suits your project needs.
Evaluating Cost-Effectiveness
To truly assess cost-effectiveness between through hole and surface mount technologies, it's essential to look beyond initial pricing alone. Consider not just what is spent upfront but also potential savings over time due to improved efficiency and reduced material waste associated with pcb surface mount assembly methods.
For instance, while assembling a simple circuit might be cheaper with through hole techniques initially, if you're planning on scaling production or require high-density designs later on—surface mounting could save significant resources in both time and money down the line. By evaluating long-term implications alongside immediate costs—companies can align their choices with overall business goals effectively.
In summary, when considering pcb surface mount assembly price trends alongside various influencing factors like design complexity or labor requirements—you'll find that making an informed choice can lead to substantial benefits for your projects moving forward.
Conclusion
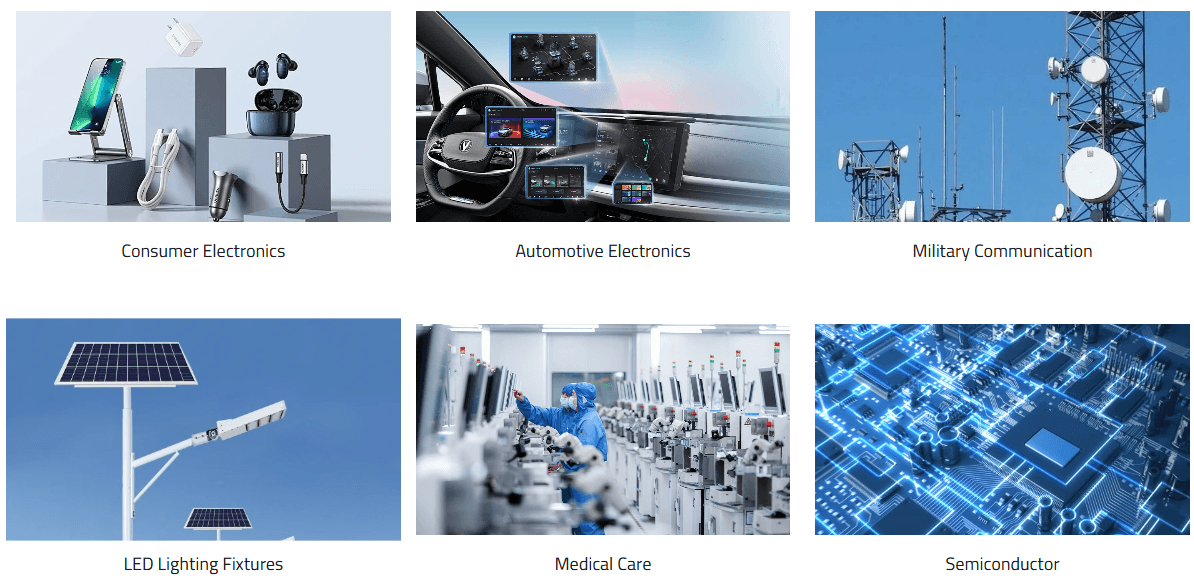
In the grand debate of through hole vs. surface mount technology, several key takeaways emerge that can help guide your decisions in PCB assembly. Through hole technology offers robust connections and is often favored for its durability, particularly in high-stress environments. On the other hand, PCB surface mount assembly shines with its space-saving design and rapid production capabilities, making it ideal for modern electronics.
Key Takeaways on Through Hole vs Surface Mount
First off, understanding what is a surface mount assembly is crucial for any PCB designer or manufacturer. Surface mount technology (SMT) allows components to be mounted directly onto the surface of PCBs, promoting a compact layout compared to traditional through hole methods. Additionally, knowing the difference between SMD (Surface Mount Device) and SMT can clarify which components best suit your project needs.
When evaluating how to make a surface mount PCB, consider not just the initial design but also how it impacts manufacturing efficiency and cost-effectiveness over time. The benefits of using a PCB surface mount assembly kit cannot be overstated; they streamline production by providing all necessary components in one package. Ultimately, each method has its unique advantages that cater to different applications.
Bensun Technology's Role in PCB Manufacturing
Bensun Technology stands at the forefront of PCB manufacturing by offering expertise in both through hole and surface mount techniques. Their commitment to quality ensures that every pcb surface mount assembly produced meets industry standards while accommodating customer-specific requirements. With an array of services tailored to various needs—ranging from prototyping to full-scale production—Bensun is a go-to partner for many looking into pcb surface mount assembly manufacturers.
Their innovative approaches not only enhance efficiency but also reduce costs associated with pcb surface mount assembly price fluctuations in the market. By utilizing advanced machinery and skilled technicians, Bensun helps clients navigate challenges like component sourcing and design adjustments seamlessly. Their role as a reliable partner means you can focus more on innovation while they handle the intricacies of manufacturing.
Making Informed Choices for PCB Assembly
When faced with choices about which method to use for your next project, it's essential to weigh all factors carefully—including cost implications such as those associated with pcb surface mount assembly price trends and required tools like soldering kits or reflow ovens. Understanding what is surface mount in PCB can provide clarity on whether this approach aligns with your product goals or if traditional methods are more suitable given your specific application requirements.
Ultimately, making informed choices involves considering both technical specifications and practical aspects like budget constraints or time-to-market pressures when deciding between through hole and SMT options. As you explore these avenues further, remember that investing time into research will pay off significantly when it comes down to selecting suitable solutions tailored specifically for your needs.